Streamlining Jewelry Production: The Impact of Casting Automation Technologies
The introduction of automated casting systems has dramatically transformed the fine jewelry industry…….
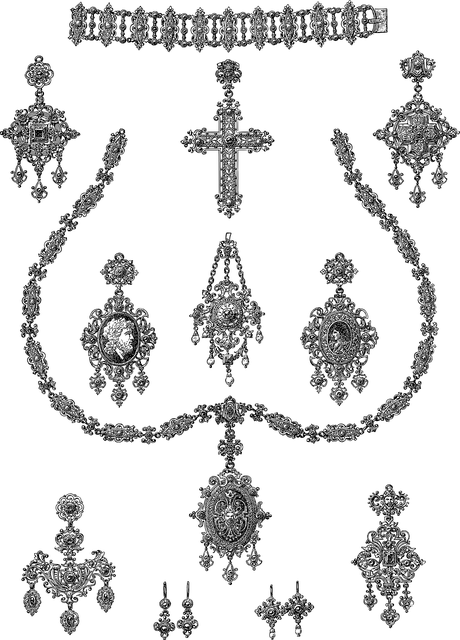
The introduction of automated casting systems has dramatically transformed the fine jewelry industry, significantly enhancing production efficiency for both small-scale artisans and large manufacturers. These systems employ advanced robotics and computer-aided design to streamline the entire casting process, from mold creation to metal pouring, resulting in shorter turnaround times, greater precision, and consistency in finished pieces. The integration of these technologies has not only made labor-intensive tasks easier but also spurred innovation in materials and design complexity within the jewelry sector. Jewelry casting automation represents a commitment to both technological advancement and sustainability, enabling artisans to produce high-quality pieces with less manual input, leading to substantial time and cost savings. The precision of these automated systems ensures that intricate designs are consistently replicated, adhering closely to the designer's vision. This shift from traditional manual casting methods like lost-wax to modern automation has been a game-changer, accelerating production while expanding design possibilities, and reflecting a new era in fine jewelry craftsmanship that is both efficient and of high quality. The investment in this technology is recouped through long-term operational efficiencies, including waste reduction, lower labor costs, and the ability to scale production according to demand, thereby supporting sustainable growth and providing a competitive advantage in the fine jewelry industry.
Exploring the transformative impact of technology on the jewelry industry, this article delves into the burgeoning field of jewelry casting automation. It charts the evolution from traditional craftsmanship to sophisticated, high-precision automated systems, offering insights into the key components and cutting-edge technologies driving this revolution. We will examine how jewelers can unlock new efficiencies in production, maximize profitability, and stay at the forefront of innovation by adopting these advanced casting techniques. Join us as we explore the intersection of tradition and technology, where automation meets artistry in the world of jewelry making.
- Unlocking Efficiency in Jewelry Production: The Role of Casting Automation
- The Evolution of Jewelry Casting Techniques: From Traditional to Advanced Automated Systems
- Key Components and Technologies in Jewelry Casting Automation
- Maximizing Profitability with Jewelry Casting Automation: A Cost-Benefit Analysis
Unlocking Efficiency in Jewelry Production: The Role of Casting Automation
In the realm of fine jewelry production, the integration of casting automation has significantly unlocked efficiency across various scales, from small-scale artisans to large-scale manufacturers. This technological advancement in jewelry casting processes not only accelerates the turnaround time for intricate pieces but also enhances the precision and consistency of castings. By leveraging advanced robotics and automated systems, the entire process from mold creation to metal pouring is streamlined, reducing the likelihood of human error and minimizing waste. This shift towards automation in jewelry casting not only optimizes labor-intensive tasks but also allows for greater experimentation with new materials and design complexities, pushing the boundaries of what can be achieved in the jewelry industry.
The adoption of casting automation in the jewelry sector is a testament to the industry’s commitment to innovation and sustainability. By implementing these cutting-edge technologies, jewelers are able to produce high-quality pieces with less manual intervention, which translates to significant time savings and cost reductions. The precision afforded by automated systems also means that intricate details can be consistently replicated, ensuring that each piece meets the exacting standards set by the designer. As a result, jewelry casting automation is not just a trend but a transformative force in the industry, setting a new standard for excellence and efficiency in jewelry production.
The Evolution of Jewelry Casting Techniques: From Traditional to Advanced Automated Systems
The craft of jewelry casting has undergone a remarkable transformation over the centuries, evolving from manual and labor-intensive processes to sophisticated automated systems that enhance precision and efficiency. Traditionally, jewelry casting involved intricate handcrafting techniques such as lost-wax casting, where artisans meticulously carved wax models that were later cast in metal through a series of heated stages. This method, while producing exquisite results, was time-consuming and required a high level of skill.
With the advent of modern technology, the jewelry industry has embraced automation to revolutionize casting processes. Contemporary jewelry casting now utilizes advanced machinery like CNC (Computer Numerical Control) machines and 3D printing technology, which enable designers to translate their digital models directly into tangible pieces with unprecedented accuracy. These systems not only speed up production but also allow for complex designs that were previously unattainable with traditional methods. The integration of robotics in the casting process further streamlines operations, ensuring consistency and quality across large-scale productions. This technological leap has made jewelry casting more accessible while maintaining the artistry and intricacy that are hallmarks of the industry.
Key Components and Technologies in Jewelry Casting Automation
Jewelry casting automation represents a significant advancement in the field of fine jewelry production, integrating sophisticated machinery and advanced technologies to streamline the casting process. Central to this automated system are the key components such as precision investment casting machines, which replicate intricate jewelry designs with remarkable consistency and detail. These machines utilize patterns or molds that are created through a digital process, ensuring high accuracy and reducing the potential for human error. The automation also incorporates high-resolution 3D printers that produce wax models directly from CAD (Computer-Aided Design) files, bypassing traditional wax carving methods. These wax models serve as the basis for the investment casting process.
Furthermore, jewelry casting automation relies on a combination of robotics and computer control systems to manage the entire casting cycle, from flask preparation to pouring, cleaning, and deburring the castings. The use of programmable logic controllers (PLCs) allows for precise temperature control in furnaces, optimizing metal melting processes. Similarly, robotic arms execute tasks such as dipping, which involves coating the wax models with a refractory material to create a mold, and handling hot casting components post-casting, ensuring both safety and efficiency. Advanced quality control systems are integrated to inspect the finished pieces, maintaining high standards of excellence and minimizing waste. The synergy of these technologies not only accelerates production times but also enables artisans to focus on design innovation rather than manual labor, pushing the boundaries of what is possible in jewelry casting.
Maximizing Profitability with Jewelry Casting Automation: A Cost-Benefit Analysis
In the realm of fine jewelry production, jewelry casting has emerged as a pivotal process that blends artistry with precision engineering. Automation within this process offers a multifaceted approach to maximizing profitability for jewelry manufacturers. By integrating advanced technologies such as robotics and computer-aided design (CAD), casting operations can achieve greater consistency, reduced human error, and increased production speeds. These enhancements not only streamline the workflow but also allow for more intricate and detailed designs that were previously challenging to produce manually. The cost implications of adopting such automation are initially significant, with investments in machinery and software. However, this upfront expenditure is often offset by the long-term savings accrued from reduced material waste, lower labor costs, and the ability to scale production in response to market demands without compromising on quality or design complexity.
Furthermore, the integration of jewelry casting automation leads to a reduction in the time it takes to bring a piece from conception to completion. This acceleration of the casting process translates into faster turnaround times and the ability to meet tight deadlines for clients or specific market windows. The consistency of automated casting also contributes to a more uniform final product, which can enhance brand reputation and customer satisfaction. From a cost-benefit perspective, the initial investment in automation technology is recouped through these operational efficiencies, ultimately leading to a higher net profit margin for businesses that embrace this technological shift. It’s evident that jewelry casting automation is not merely an upgrade in production methods but a strategic move towards sustainable growth and enhanced competitiveness within the fine jewelry industry.