Organic Elegance: Mastering Jewelry Casting for Unique Designs
The article provides a comprehensive overview of the jewelry casting process, particularly as it ap…….
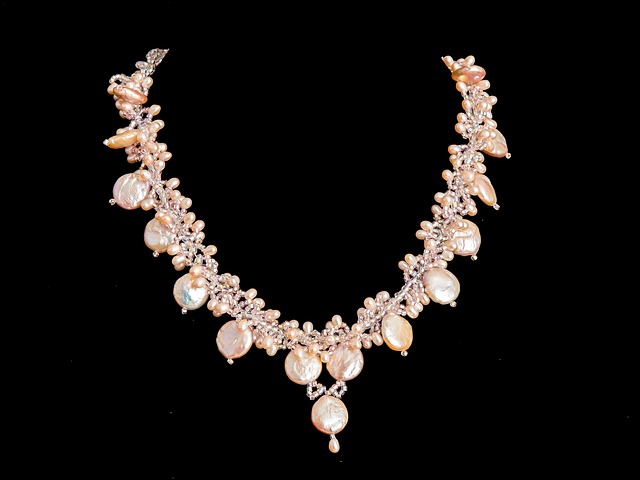
The article provides a comprehensive overview of the jewelry casting process, particularly as it applies to creating organic-inspired designs. This technique allows artisans to consistently and precisely reproduce intricate patterns and textures in precious metals like silver and gold. The casting involves melting these materials into molds crafted from detailed wax or resin models, which can be hand-carved or made using 3D printing technology. The lost-wax casting method is ideal for organic designs due to its ability to capture complex details. The choice of materials—such as silver with its tarnish-resistant properties, gold for durability and luster, or titanium for strength and lightness—is critical in ensuring the final jewelry pieces are both aesthetically pleasing and durable. Model making is a pivotal part of this process, as it translates the artist's vision into a tangible scale model that becomes the direct blueprint for casting. The precision of these models ensures that the resulting jewelry maintains the organic forms and textures intended by the designer. Mastery of jewelry casting and model making is essential for creating high-quality pieces that embody the natural inspiration at their core, appealing to those who appreciate craftsmanship, detail, and artisanal jewelry.
Jewelry casting transcends the ordinary, giving rise to pieces that are both wearable art and tangible expressions of creativity. This article delves into the intricate world of organic jewelry casting, detailing the process from concept to creation. We’ll explore the essentials of jewelry casting, the selection of suitable materials, the artistry involved in model making, and cutting-edge advancements that elevate this craft. Join us as we shed light on the techniques that breathe life into designs, ensuring each piece is a testament to the artisan’s skill.
- Understanding the Jewelry Casting Process: An Overview
- Material Selection for Organic Jewelry Casting: Choosing the Right Metals and Alloys
- The Art of Model Making: Crafting the Perfect Mold for Your Designs
- Innovations in Jewelry Casting: Advancements and Techniques for Organic Pieces
Understanding the Jewelry Casting Process: An Overview
The craft of creating organic jewelry designs often involves a meticulous process known as jewelry casting. This method allows artisans to replicate intricate patterns and designs with precision and consistency. In jewelry casting, a material such as silver or gold is melted and poured into a mold that has been carefully crafted to capture every detail of the intended design. The mold is typically made from a wax or resin model that has been carved or 3D printed to match the design’s contours. Once the molten metal cools and solidifies within the mold, it takes on the exact shape of the original model. This process, also known as lost-wax casting, is particularly adept at producing pieces with organic forms and textures that are challenging to achieve through other means. The resulting jewelry boasts a level of detail and beauty that is both hypnotic and unique, making it a favorite among collectors and enthusiasts alike. Additionally, the versatility of this process allows for a wide range of jewelry types, from statement pieces to delicate, fine jewelry, each imbued with the artisan’s signature style and craftsmanship. Understanding the intricacies of the jewelry casting process is essential for anyone interested in the field, as it not only shapes the final product but also dictates the quality and character of the organic designs that emerge from this ancient yet timeless technique.
Material Selection for Organic Jewelry Casting: Choosing the Right Metals and Alloys
When it comes to casting organic jewelry designs, the selection of metals and alloys plays a pivotal role in achieving both the desired aesthetic and functional integrity. Jewelry casting involves pouring molten metal into a mold to create intricate pieces that embody the essence of organic forms. The choice between metals such as sterling silver, 18-karat gold, and various alloys like titanium or palladium hinges on factors including durability, hypoallergenic properties, and the natural appeal each material presents.
Sterling silver, a blend of pure silver with other metals, typically copper or nickel, is a popular choice for casting due to its workability and tarnish-resistant qualities. Its reflective surface and malleable nature allow for detailed casts that capture the organic textures and shapes seamlessly. On the other hand, 18-karat gold offers a richer hue than 24-karat gold, which makes it more resistant to wear and tear, enhancing its longevity and appeal. Additionally, modern alloys like titanium provide both strength and a lightweight feel, making them suitable for intricate designs that require a robust yet fine structure. Each material offers unique characteristics that can be leveraged to highlight the organic nature of the jewelry design, ensuring the final piece is not just a replica but an enhancement of the original inspiration. When mastering the art of jewelry casting, understanding the nuances of each metal and alloy is crucial for creating pieces that are as enduring as they are enchanting.
The Art of Model Making: Crafting the Perfect Mold for Your Designs
In the realm of organic jewelry design, the art of model making stands as a pivotal step in the jewelry casting process. Artisans meticulously sculpt the ideal representation of their designs in clay or wax, ensuring that every intricate detail is captured precisely. This model serves as a direct blueprint for the final piece, translating the artist’s vision into a form that can be utilized for casting. The precision of these models is crucial; they must accurately reflect the nuances of the design to ensure a seamless transition from concept to tangible creation. Once complete, the model undergoes a process where it is encased in a mold material, typically silicone or plaster, which captures every contour and texture. This mold becomes the vessel through which molten metal will flow, taking the shape of the original design. The skillful creation of this mold is a blend of artistry and technical expertise, as it must withstand the high temperatures and pressures of the casting process while producing a high-fidelity replica of the model. Jewelry casting relies heavily on the integrity of these molds to achieve the organic textures and natural beauty that define this craft. Artisans who master the art of model making and mold creation can produce jewelry pieces that are not only faithful to their initial vision but also possess a tactile allure that resonates with those who appreciate the fusion of nature and wearable art.