Preventing Failures in Ring Terminals: A Comprehensive Guide
Ring terminals are essential components for securely connecting electrical wires, offering durable …….
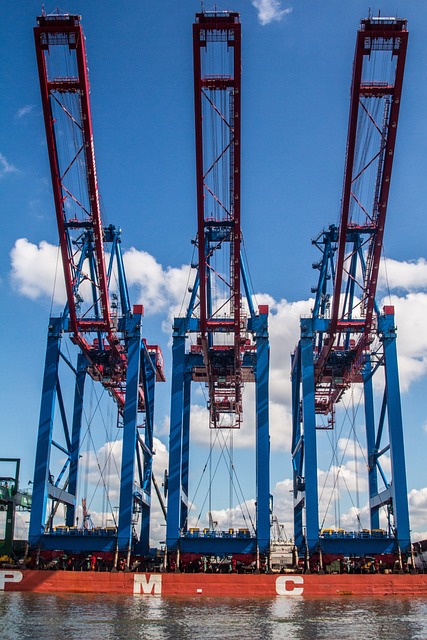
Ring terminals are essential components for securely connecting electrical wires, offering durable and weatherproof attachments that ensure the functionality and longevity of electrical systems across various environments. Their robust design features a metal ring within an insulating body that accommodates wire insertion and clamping, with materials like rubber, silicone, or PVC chosen for their resistance to environmental factors and high temperatures. Compatibility with different wire sizes and types is achieved through the use of metals such as brass, aluminum, or stainless steel, which also cater to varying conductivity needs and environmental conditions. Set screws maintain a tight fit around the wire to prevent slippage and ensure stable connections. Proper maintenance and regular inspections are crucial for preserving the electrical integrity of ring terminals over time, guarding against wear, damage, and safety risks associated with corrosion, loose connections, or poor solder joints. The longevity and reliability of these terminals depend on careful selection of materials, precise manufacturing processes, and strict adherence to quality control standards. Regular inspection, maintenance, and following manufacturer guidelines are indispensable for ensuring the optimal performance and safety of ring terminals in demanding environments. Adhering to these practices can significantly enhance their durability and prevent premature degradation, contributing to consistent performance throughout their service life.
When examining the reliability and longevity of electrical systems, ring terminals play a pivotal role. These components secure electrical conductors to various devices and are integral to safety and performance. This article delves into the intricacies of ring terminal functionality and design, shedding light on their critical role in electrical connections. It also explores common failure points, such as corrosion and material degradation, and their underlying causes. Understanding material considerations is crucial for maintaining ring terminal integrity, a factor often overlooked but vital for ensuring long-term reliability. By adhering to best practices for installation, maintenance, and operation, and implementing strategic preventative measures, the lifespan of ring terminals can be significantly extended, thereby safeguarding against electrical system failures.
- Understanding Ring Terminal Functionality and Design
- Common Failure Points in Ring Terminals and Their Causes
- Material Considerations and Their Impact on Ring Terminal Integrity
- Best Practices for Installation, Maintenance, and Safe Operation of Ring Terminals
- Strategic Preventative Measures to Extend the Lifespan of Ring Terminals
Understanding Ring Terminal Functionality and Design
Ring terminals are robust connectors that provide a reliable and secure means of attaching electrical wires to various types of equipment and machinery. Their functionality is centered around ensuring a strong, weatherproof, and durable connection, which is crucial for the performance and longevity of electrical systems in diverse environments. The design of ring terminals typically involves a metal ring with an integral insulating body, into which the wire is inserted and securely clamped. This combination of metal and insulation protects against corrosion and environmental factors such as moisture and vibration, which could otherwise compromise the integrity of the electrical connection.
The design of these terminals is meticulously engineered to accommodate different wire sizes and types, accommodating a wide range of applications. The insulating body of the terminal is available in various materials including rubber, silicone, or PVC, each chosen for specific conditions such as high temperature resistance, oil, or chemical exposure. Additionally, the metal portion can be made from brass, aluminum, or stainless steel to suit different conductivity needs and environments. The construction of ring terminals often incorporates set screws to ensure a tight fit around the wire, preventing slippage and ensuring a stable connection. Proper installation is key to the functionality of these terminals; it involves stripping the wire insulation to the correct length, inserting it into the terminal, and securing it with the set screws. Regular maintenance and inspection are also vital to ensure that the ring terminals remain functional over time, maintaining their electrical integrity and preventing potential failure due to wear or damage.
Common Failure Points in Ring Terminals and Their Causes
Ring terminals, crucial components in electrical systems, are subject to failure at various points, which can compromise the integrity and functionality of the entire system. One common failure point is at the terminal-to-conductor interface. This junction is prone to issues such as corrosion, loose connections, or poor solder joints, all of which can significantly reduce electrical conductivity and cause potential safety hazards. The use of incompatible materials or improper terminal tightening can exacerbate these problems, leading to eventual failure.
Another frequent point of failure is the insulation of the ring terminals themselves. Degradation of the insulation can occur due to environmental factors like UV exposure, extreme temperatures, or mechanical stress from vibrations and movements. Additionally, insulation breakdown might be attributed to electrical overloads or improper installation techniques. Regular maintenance, which includes visual inspections and resistance testing, is essential to detect these issues early and prevent potential failures that could lead to short circuits or system breakdowns. It is imperative for users to adhere to manufacturer specifications and industry best practices when installing and maintaining ring terminals to ensure their longevity and reliability.
Material Considerations and Their Impact on Ring Terminal Integrity
When addressing ring terminal failure, material considerations are paramount in ensuring the integrity and longevity of these components. Ring terminals, which serve as critical electrical connections between wires and various conductive elements, must withstand a range of environmental conditions and electrical loads. The choice of materials for both the conductor and the insulation is crucial, as it affects their resistance to corrosion, mechanical stress, and thermal cycling. For instance, copper alloys are frequently used for conductors due to their high electrical conductivity and durability. However, the environment in which the ring terminal operates can dictate the type of copper alloy required, as some are more resistant to certain corrosives than others. Similarly, the insulation material must be selected based on its ability to withstand the operational temperature range, UV exposure, and potential contact with chemicals or solvents.
The integrity of ring terminals is also influenced by the quality of the materials’ preparation and the subsequent manufacturing processes. Inadequate cleaning and preparation can lead to poor electrical contacts and increased resistance over time. Additionally, if the insulation is not applied uniformly or if it contains impurities, it can compromise the ring terminal’s performance and safety. It is essential that manufacturers adhere to strict quality control measures during production to ensure that the final product meets the necessary standards for electrical integrity. Employing high-quality materials, meticulous preparation, and stringent manufacturing processes collectively contribute to a reliable and long-lasting ring terminal, which can significantly reduce the likelihood of failure in critical applications.
Best Practices for Installation, Maintenance, and Safe Operation of Ring Terminals
When installing ring terminals, it is imperative to adhere to the manufacturer’s guidelines and industry standards to ensure optimal performance and safety. Proper installation begins with selecting the correct size and type of ring terminal for the application, considering factors such as cable diameter, voltage ratings, and environmental conditions. Upon receipt, inspect the ring terminals for any damage during shipping that might compromise their integrity. When fitting the ring terminal onto the conductor, ensure a snug fit without over-tightening, which can lead to deformation or damage to both the terminal and the cable. Utilize appropriate tools and follow torque specifications precisely to maintain conductivity and prevent future failures.
Regular maintenance is equally crucial for the longevity and reliability of ring terminals. Visual inspections should be conducted periodically, especially after exposure to harsh environments or following any mechanical stress. Look for signs of corrosion, wear, or looseness that could impair electrical connections or lead to potential hazards. Cleaning and lubrication of the terminal can help maintain its functionality, and any identified issues should be addressed promptly. Employ proper labeling practices to denote maintenance history and ensure that all ring terminals are up-to-date with their service records. In terms of safe operation, always follow electrical safety protocols and avoid overloading connections, which can cause excessive heat and accelerate terminal degradation. By implementing these best practices for installation, maintenance, and operation, users can significantly reduce the risk of ring terminal failure and ensure continued reliability in their applications.
Strategic Preventative Measures to Extend the Lifespan of Ring Terminals
To effectively extend the lifespan of ring terminals, it is imperative to implement strategic preventative measures. Proactive maintenance and inspection are crucial for early detection of potential issues that could lead to failure. Regularly examining ring terminals for signs of wear, corrosion, or damage can prevent subsequent electrical problems and reduce the risk of catastrophic failure. Employing appropriate environmental protection measures, such as using protective caps when not in use and ensuring proper sealing against moisture, is vital. Additionally, selecting the correct size and type of ring terminal for the application can mitigate stress and strain on the terminals during operation. Utilizing materials that match the conductivity requirements and environmental conditions of the specific application will further enhance their longevity.
Furthermore, adhering to manufacturer guidelines and industry standards is essential for optimal performance. Routine cleaning and application of suitable lubricants can maintain the integrity of the connections, ensuring smooth conduction of electricity. Incorporating robust quality control processes during manufacturing and installation further minimizes the risk of terminal failure. Regular training for personnel involved in handling ring terminals should also be a part of the preventative strategy to ensure proper usage and maintenance. By prioritizing these measures, one can significantly reduce the likelihood of unexpected failures and ensure that ring terminals function reliably over their intended lifespan.