Optimal Maintenance and Inspection of Ring Terminals for Reliable Performance
Regular maintenance is key to extending the lifespan and ensuring the safety and performance of rin…….
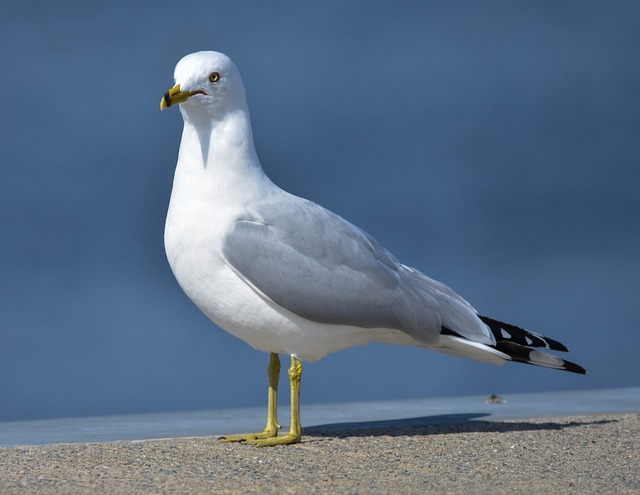
Regular maintenance is key to extending the lifespan and ensuring the safety and performance of ring terminals within electrical systems. These components are prone to wear and corrosion over time, particularly when exposed to harsh conditions or mishandled. A systematic visual inspection at regular intervals post-exposure is necessary to detect any deformation, corrosion, or signs of wear on the terminal body, contact surfaces, and seal areas that could let in moisture or contaminants. Cleaning with non-abrasive agents and applying protective lubricants as per manufacturer's instructions are essential steps for maintaining ring terminals, safeguarding against future corrosion and ensuring smooth operation. Precision tools should be used when tightening connections to avoid overtightening and potential damage. Detailed maintenance records help monitor performance and compliance with safety regulations. A diligent maintenance program that includes regular inspections, cleaning, monitoring for wear or corrosion, and functional testing is vital for the reliability of ring terminals in various applications. This routine not only minimizes the risk of sudden failures but also ensures optimal performance and contributes to the overall efficiency and safety of electrical systems utilizing these components.
When it comes to ensuring the reliability and longevity of electrical connections, ring terminal maintenance and inspection stand as pivotal practices. This article delves into best practices for regular inspection of ring terminals, detailing comprehensive maintenance strategies that safeguard against operational disruptions. It also addresses common issues in ring terminal systems, providing actionable insights to maintain their integrity. Understanding these protocols is not just about upkeep; it’s a commitment to safety and performance within various industrial applications.
- Best Practices for Regular Inspection of Ring Terminals
- Comprehensive Maintenance Strategies for Ring Terminals
- Identifying and Addressing Common Issues in Ring Terminal Systems
Best Practices for Regular Inspection of Ring Terminals
Regular inspection and maintenance of ring terminals are critical for ensuring their longevity, safety, and reliability in electrical connections. To maintain optimal performance, it is recommended to conduct visual inspections at regular intervals, especially after exposure to harsh environments or following any mishandling. Key areas to focus during these inspections include the terminal’s body for deformation or signs of corrosion, the contact surfaces for wear or oxidation, and the seal points for any breaches that could lead to ingress of moisture or contaminants.
During maintenance, it is essential to clean and lubricate the ring terminals as per the manufacturer’s guidelines. The use of appropriate cleaning agents, free from abrasive particles, will remove dirt without damaging the terminal. Subsequently, applying a suitable lubricant will protect against future corrosion and ensure smooth operation. Additionally, when tightening any connections, care should be taken to avoid overtightening, which could lead to damage or deformation of the terminal’s body. Utilizing calibrated tools can help prevent this issue. Regularly scheduled inspections and maintenance, coupled with a meticulous approach to handling and installation, will extend the service life of ring terminals and maintain their electrical integrity under continuous operation. It is also advisable to document all maintenance activities to track performance over time and ensure compliance with safety standards.
Comprehensive Maintenance Strategies for Ring Terminals
Regular maintenance of ring terminals is imperative for ensuring their longevity and reliable performance. A comprehensive maintenance strategy should include a detailed inspection schedule, routine cleaning protocols, and systematic checks for wear and tear. The frequency of maintenance activities depends on the usage conditions and environment in which the ring terminals operate. For instance, terminals exposed to harsh weather or corrosive substances may require more frequent attention than those in controlled indoor environments.
During each inspection, visual assessments should be conducted to identify any signs of physical damage or deterioration. This includes checking for cracks, deformation, and signs of corrosion that could compromise the connection integrity. Additionally, terminals should be functionally tested to verify proper operation, including secure cable connections and unimpeded conduction. Lubrication of moving parts is another critical aspect of maintenance, as it can prevent premature wear and ensure smooth operation. By implementing these maintenance strategies, users can prolong the life of their ring terminals and maintain a safe and efficient electrical connection system. Regular upkeep not only reduces the likelihood of unexpected failures but also ensures that the equipment operates at peak efficiency, ultimately contributing to the overall reliability of the electrical system it is part of.
Identifying and Addressing Common Issues in Ring Terminal Systems
Regular maintenance and inspection are critical for ensuring the reliability and longevity of ring terminal systems, which are integral components in electrical connections. Over time, various issues can arise within these systems that may compromise their performance. Common problems include corrosion, loose or damaged terminals, and over-torqued connections. Corrosion is particularly prevalent, as it can be caused by environmental factors such as moisture, salt, dust, and industrial pollutants. This can lead to poor electrical conductivity and potentially cause circuit failures or fires if left unaddressed. To mitigate this, a routine inspection should include checking for signs of corrosion and applying appropriate protective coatings as needed.
Another frequent issue is the loosening of terminals due to vibrations and movements in their operational environment. This can result in poor contact and increased resistance, potentially leading to overheating and further damage. It is essential to tighten any loose terminals to the manufacturer’s specified torque values to avoid the risk of over-tightening, which can deform the terminal or the conductor. Regularly scheduled maintenance should involve a thorough examination of all ring terminal connections to ensure they are secure and properly tightened. Additionally, visual inspections should be conducted to identify any nicks, cuts, or deformation in the terminals themselves. Addressing these issues promptly not only prevents electrical failures but also ensures the continued safety and efficient operation of the ring terminal system.