Engineering Fortune: The Manufacturing Precision Behind Casino Dice
Casino dice undergo a rigorous manufacturing process to ensure their integrity and consistency, whi…….
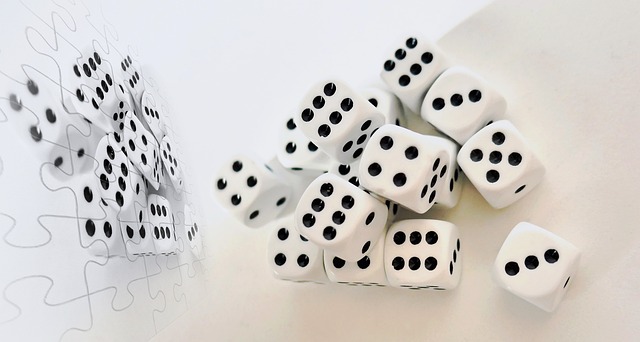
Casino dice undergo a rigorous manufacturing process to ensure their integrity and consistency, which are paramount for maintaining fair play in games like craps. They are meticulously crafted from high-quality materials such as polyresin composites or acrylic/resin, with precise measurements and strict quality control to guarantee uniform density, weight distribution, and resistance to manipulation. The selection of pigments for coloring is done to maintain stability without affecting integrity over time. Post-manufacturing, each die undergoes comprehensive testing, including checks for dimensions, balance, bounce consistency, and randomness, with optical scanning verifying edge and face regularity. Rigorous repetitive throw tests confirm the dice' performance over time. Packaging is managed to protect against damage and is tamper-evident, often featuring unique serial numbers for traceability. The distribution network is designed to adhere to cold chain protocols and navigate transportation regulations, ensuring timely delivery while maintaining product quality. Throughout, the industry upholds compliance with gaming commissions and health safety standards, demonstrating a commitment to responsible and fair gaming practices, which in turn upholds player trust and confidence.
Casino dice, integral to the games of chance they serve, are meticulously crafted through a sophisticated manufacturing process that ensures fairness and durability. This article delves into the intricate steps of material selection, composition analysis, and design specifications that go into creating these essential gaming tools. From the initial choice of raw polymer to the precise molding techniques that shape them, each phase is scrutinized under rigorous quality control measures and testing standards. Furthermore, the journey concludes with an examination of packaging, distribution, and regulatory compliance in the dynamic casino dice industry. Understanding this process provides a clear perspective on the science and artistry behind these seemingly simple yet pivotal components of casino entertainment.
- Material Selection and Composition Analysis for Casino Dice
- Design Specifications and Tolerances in Casino Dice Fabrication
- The Molding Process: From Raw Polymer to Precision-Cut Dice
- Quality Control Measures and Testing Standards for Gaming Dice
- Packaging, Distribution, and Regulatory Compliance in the Casino Dice Industry
Material Selection and Composition Analysis for Casino Dice
Casino dice, integral to games of chance like craps and gambling-centric entertainment, are meticulously crafted to meet stringent standards of fairness and integrity. The selection of materials for casino dice is paramount, as it influences both their durability and the randomness of their fall. Typically, dice used in casinos are made from a polyresin composite, which is chosen for its excellent balance between density and hardness. This material ensures that each die has a consistent weight distribution, reducing the likelihood of bias or manipulation. The composition analysis of casino dice involves precise measurements of the resin and any additives used to achieve a uniform density across all individual dice within a set. This is crucial for maintaining the game’s integrity, as inconsistencies in weight or material could potentially affect the outcome of a roll.
The manufacturing process begins with the careful mixing of the polyresin base with any necessary pigments to achieve the desired color. These pigments are chosen not only for their visual appeal but also for their stability and inertness, ensuring they do not alter the die’s properties over time or through repeated use. After the mixture is poured into molds, it undergoes a curing process that solidifies the dice into their iconic shape and size. The resulting polyresin dice are then subjected to rigorous testing to verify their quality and performance. Each die is weighed and measured to confirm its mass and dimensions adhere to the standards set by gaming authorities, ensuring that casino dice provide a fair and random outcome for players.
Design Specifications and Tolerances in Casino Dice Fabrication
In the meticulous realm of casino dice manufacturing, design specifications play a pivotal role in ensuring fairness and consistency, which are paramount to the integrity of games like craps and roulette. The dimensions of the dice must adhere to stringent standards set by gaming authorities to prevent any manipulation or irregularities. Each die is crafted with precision, with a specified weight, size, and shape that conform to regulatory requirements. The material used, typically a high-quality plastic or resin, undergoes rigorous testing to guarantee durability and resistance to environmental factors. Manufacturers employ advanced machinery capable of cutting and shaping the dice with exacting tolerances; these machines are programmed to produce dice that meet the narrowest margins of error, often within a few micrometers. The edges and faces of the dice are scrutinized under high-magnification lenses to ensure they exhibit no imperfections or irregularities that could influence gameplay. This commitment to exactness in design specifications and tolerances is crucial for maintaining the trust and confidence of casino operators and players alike, as well as for upholding the regulations set forth by gaming commissions worldwide. The integrity of the dice is not just a matter of chance but a cornerstone of the gaming experience in casinos across the globe.
The Molding Process: From Raw Polymer to Precision-Cut Dice
The manufacturing process of casino dice is a meticulous operation that transforms raw polymer into precision-cut gaming essentials. This journey from raw material to a finished product begins with the selection of high-quality polymers, such as resin or acrylic, which are chosen for their durability and consistency under various environmental conditions. These materials are then carefully melted and poured into specialized molds designed to create the six-sided cubic shape characteristic of casino dice. The molds are crafted with precision to ensure that each die has precisely measured edges and flat faces, a critical aspect for the dice to roll fairly and accurately. After the polymer solidifies into the desired form, the freshly minted dice are removed from the molds and subjected to a series of processes to refine their surfaces.
Once extracted, the raw dice undergo a cutting-edge process known as CNC (Computer Numerical Control) machining. This sophisticated technique employs computerized controls and automated tools to precisely carve out the numerical values on each die face. The CNC machines are programmed with precise specifications to ensure that the numbers are deeply etched, enhancing legibility and preventing wear over time. After this process, the dice undergo stringent quality control checks to confirm their integrity, accuracy of roll, and compliance with regulatory standards. This commitment to precision and quality ensures that casino dice manufactured through this process meet the high expectations set by players and casinos alike.
Quality Control Measures and Testing Standards for Gaming Dice
Casino dice are integral components of various games, from craps to Sic Bo, and their integrity is paramount to maintaining fair play and trust in gaming establishments. Manufacturers adhere to stringent quality control measures to ensure each die meets rigorous standards. The manufacturing process begins with the selection of raw materials; high-quality acrylic or resin is preferred for its durability and consistency. Once shaped, the dice undergo a series of precise measurements to verify their dimensions comply with industry regulations. This meticulous step ensures that each die falls within the acceptable tolerance ranges, guaranteeing fair roll outcomes.
After dimension verification, the dice progress to testing standards specific to gaming equipment. These tests include assessments for balance, bounce consistency, and randomness in outcomes. A precise optical scanning system checks the die’s edges and faces for irregularities that could influence the result of a cast. Additionally, each die is subjected to repeated throws under controlled conditions to evaluate its performance over time. This ensures that the dice maintain their integrity and provide consistent results under the dynamic conditions found in casino settings. Only when a die passes all these tests does it earn its place among the casino’s gaming inventory, ensuring a trustworthy and enjoyable experience for players.
Packaging, Distribution, and Regulatory Compliance in the Casino Dice Industry
In the realm of casino gaming, the integrity and consistency of dice are paramount for fair play and player confidence. Post-manufacturing, dice undergo rigorous quality control checks to ensure they meet stringent industry standards. Once validated, the packaging process is meticulously executed to protect the dice from damage during transport. High-quality, tamper-evident packaging is essential to maintain the integrity of the product from production line to end user. This packaging must adhere to regulatory requirements and often includes unique serial numbers for traceability.
Distribution channels for casino dice are strategically managed to ensure timely delivery while maintaining the cold chain necessary to preserve the dice’s quality. Distributors must comply with regional and international transportation regulations, which can vary significantly. The logistics network is designed to navigate these complexities, ensuring that each set of dice arrives at its destination within the required timeframe and ready for play. Compliance with regulatory bodies such as gaming commissions and health safety standards is a continuous requirement throughout the distribution process, underscoring the commitment to responsible and fair gaming practices.