Mastering Control Panel Wiring with Optimal Ring Terminal Solutions
Ring terminals are essential for secure and reliable electrical connections in control panel wiring…….
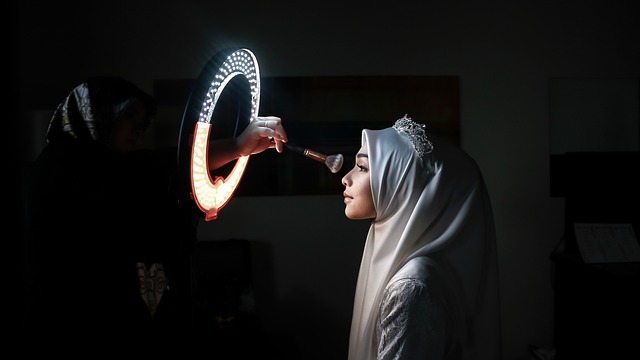
Ring terminals are essential for secure and reliable electrical connections in control panel wiring, serving as robust fittings that withstand various industrial conditions. The correct choice of ring terminal size and material is paramount to prevent issues like corrosion, loosening, or overheating, ensuring system integrity and safety against electrical risks. Professionals must carefully install these terminals by accurately cutting and stripping wires before securing them within the terminal to the appropriate tension. Utilizing anti-seize compounds can further enhance the performance and longevity of the connections. In selecting ring terminals, material choices like copper alloy, aluminum, or stainless steel are critical for performance and durability under specific environmental challenges. Properly matching the metal type with the right insulation—such as PVC or silicone rubber—ensures additional safety and consistent power transmission. Adherence to industry standards set by national electrical codes and regular maintenance is vital for the long-term reliability of these terminals, making them a cornerstone of dependable control panel wiring systems. Advanced locking ring terminals offer enhanced security against vibration, shock, and environmental stressors, ideal for applications where safety, efficiency, and durability are non-negotiable. Regular inspections and protection against corrosion are essential to maintain their performance over time.
When constructing robust control panel wiring, selecting the appropriate ring terminals is paramount. This article delves into the essential aspects of ring terminals, guiding readers through material choices, standard sizes, and installation techniques that promote secure and reliable connections. We’ll explore the importance of insulation for elemental protection and examine advanced features like locking mechanisms for critical applications. Additionally, we’ll address common issues to ensure your wiring operates at peak performance. Understanding ring terminals is not just about connecting wires; it’s about ensuring the integrity and safety of your control panel system.
- Understanding Ring Terminals: A Comprehensive Guide for Control Panel Wiring
- Material Considerations: Choosing the Right Ring Terminal for Your Application
- Ring Terminal Sizes and Standards: What You Need to Know for Efficient Wiring
- Installation Best Practices: Ensuring Secure and Reliable Connections with Ring Terminals
- The Role of Insulation in Ring Terminals: Protecting Your Control Panel Wiring from the Elements
- Advanced Features: Locking Ring Terminals and Their Benefits for Critical Applications
- Troubleshooting Common Issues with Ring Terminals in Control Panel Wiring
Understanding Ring Terminals: A Comprehensive Guide for Control Panel Wiring
Ring terminals serve as critical components in control panel wiring, ensuring secure and reliable electrical connections. These fittings, also known as ring connectors or lugs, are designed to wrap around conductors such as wires or cables, providing a solid anchoring point that withstands the rigors of industrial environments. When selecting ring terminals for control panel wiring, it is imperative to consider the appropriate size and material to match the gauge of the wire and the operating conditions it will encounter. The correct ring terminal minimizes the risk of corrosion, loosening, or overheating, which could lead to system failure or electrical hazards.
Proper installation of ring terminals is a skill that combines technique with an understanding of the physical and electrical properties of the wiring system. It involves cutting the wire to the correct length, stripping the insulation to expose the appropriate amount of conductor, and then inserting and securing the wire within the terminal. The terminal should be tightened to the manufacturer’s specifications to ensure a snug fit without causing damage to the wire. Additionally, the use of anti-seize compounds or lubricants can facilitate easier installation and prevent corrosion at the connection point. Understanding the intricacies of ring terminals and their role in control panel wiring is essential for electrical professionals who aim to create safe, efficient, and durable electrical systems.
Material Considerations: Choosing the Right Ring Terminal for Your Application
When selecting ring terminals for control panel wiring, material considerations are paramount to ensure optimal performance and longevity. The choice of material affects the terminal’s durability, resistance to environmental factors, and overall reliability under varying conditions. Ring terminals can be manufactured from a variety of materials such as copper alloy, aluminum, and stainless steel, each with its unique properties and suitability for different applications. Copper alloy ring terminals offer excellent conductivity and are resistant to corrosion, making them ideal for general-purpose electrical connections. For applications that require lightweight components without compromising on conductivity, aluminum ring terminals are a suitable alternative. They are also anodized to enhance their resistance to weathering and environmental factors. When operating in harsh conditions where corrosion and high salinity are concerns, stainless steel ring terminals provide superior protection due to their inherent strength and resistance to rust and oxidation. It is essential to consider the specific requirements of your application, including temperature ranges, exposure to chemicals, moisture, and mechanical stress, to select the most appropriate material for your ring terminal. This will guarantee a secure and long-lasting connection that meets the necessary safety and efficiency standards. Additionally, the correct choice of insulation material, such as PVC or silicone rubber, complements the selection of metal types to further protect against electrical shorts and ensure safe and reliable power transmission in control panel wiring.
Ring Terminal Sizes and Standards: What You Need to Know for Efficient Wiring
When working with control panel wiring, selecting the appropriate ring terminal size and adhering to industry standards is paramount for efficient and safe electrical connections. Ring terminals serve as the interface between conductors and various types of hardware, such as bolts, nuts, or conduit entries. The correct ring terminal not only ensures a secure and reliable connection but also prevents potential wire damage and electrical hazards.
Ring terminals come in a variety of sizes to accommodate different wire gauges and diameters. It is essential to choose the right size to maintain the integrity of the electrical circuit. For example, a ring terminal that is too small for the wire can cause excessive compression which may lead to insulation damage or even conductor deformation. Conversely, a ring terminal that is too large may not provide a secure enough connection. Industry standards, such as those outlined by the National Electrical Manufacturers Association (NEMA), provide guidelines on the appropriate sizes for different wire types and gauges. These standards ensure compatibility and safety across various applications. When wiring control panels, it is crucial to consult these standards to select the correct ring terminal that aligns with the American Wire Gauge (AWG) specifications. Properly sized ring terminals facilitate efficient wiring practices by reducing the likelihood of connectivity issues and ensuring compliance with electrical codes and safety protocols. This attention to detail not only protects the investment in equipment but also safeguards personnel and operational continuity. Understanding the nuances of ring terminal sizes and adhering to these standards is a critical component of effective wiring practices for control panels.
Installation Best Practices: Ensuring Secure and Reliable Connections with Ring Terminals
When engaging in control panel wiring, using ring terminals is a critical step to ensure secure and reliable connections. The installation of ring terminals should adhere to specific best practices to guarantee the integrity of electrical connections. Firstly, it is imperative to select the appropriate size of ring terminal for the gauge of wire being used. This match ensures optimal contact and conduction of electricity. Secondly, proper cleaning of both the wire and the terminal’s contacts before assembly is crucial for a high-quality connection. Oxidation or debris can compromise the electrical interface, leading to poor connections or even fire hazards.
During installation, inserting the wire into the ring terminal should be done with care to avoid damaging the conductor. The wire must be centered within the terminal’s body to allow for uniform pressure around the conductor when the terminal is tightened. Utilizing a proper tool, such as a wrench designed for this purpose, applies the necessary tension without overtightening, which could deform or cut into the wire insulation. Additionally, ensuring that the ring terminal is positioned on the wire in such a way that it does not impede movement or function of the control panel components is essential for the longevity and functionality of the system. Proper labeling of terminals, if necessary, enhances maintenance and troubleshooting efficiency. By following these installation best practices, technicians can achieve robust, durable connections with ring terminals that meet industry standards and provide long-term reliability in control panel wiring applications.
The Role of Insulation in Ring Terminals: Protecting Your Control Panel Wiring from the Elements
Ring terminals play a pivotal role in the integrity and functionality of control panel wiring by serving as the interface between conductive wires and their respective connections. A critical aspect of ring terminals is their insulation, which safeguards the electrical circuitry from environmental factors and potential electrical hazards. The quality of insulation in ring terminals directly impacts the longevity and performance of the control panel wiring system. It is designed to withstand a variety of harsh conditions, including exposure to moisture, dust, and chemicals, which could otherwise compromise the integrity of the circuit.
The insulation materials used in ring terminals are carefully selected based on their resistance to chemical attack, temperature extremes, and mechanical wear. These materials, such as rubber or thermoplastic elastomers, provide a protective barrier that not only ensures the continuity of the electrical signal but also prevents electrical leakage and short circuits. Additionally, the insulation contributes to the overall durability and reliability of the wiring, ensuring that the control panel operates safely and efficiently under various conditions. By selecting ring terminals with appropriate insulation for specific applications, users can rest assured that their control panel wiring will remain protected from the elements, thereby enhancing system longevity and performance.
Advanced Features: Locking Ring Terminals and Their Benefits for Critical Applications
Ring terminals serve as a critical component in control panel wiring, particularly in applications where reliability and safety are paramount. Advanced locking ring terminals offer enhanced performance by providing a secure connection that resists disconnection due to vibration or shock. These terminals are engineered with an internal locking mechanism that ensures the wire remains firmly attached to the terminal, even under harsh environmental conditions. This feature is especially beneficial in critical applications such as industrial machinery, medical devices, and renewable energy systems where a stable connection is essential for consistent operation. The locking mechanism also simplifies maintenance by reducing the likelihood of accidental disconnections during routine checks or adjustments, thus minimizing downtime and increasing overall system reliability. Furthermore, these terminals are often designed with corrosion-resistant materials and robust construction to withstand varying temperatures and environmental factors, ensuring long-term durability and performance in demanding environments. When selecting ring terminals for such applications, prioritizing those with locking features will contribute significantly to the safety and efficiency of the system.
Troubleshooting Common Issues with Ring Terminals in Control Panel Wiring
When integrating ring terminals into control panel wiring, professionals may encounter various issues that can affect the functionality and safety of the system. One common problem is improper tightening, which can lead to loose connections. This not only compromises the electrical connection but also poses a risk of arcing and potential fire hazards. To address this, it’s crucial to follow manufacturer guidelines for torque specifications to ensure a secure fit without overtightening, which could damage the terminal or the conductor.
Another frequent issue is the selection of an incorrect ring terminal size for the gauge of wire being used. Using a ring terminal that is too small can result in poor contact and potentially lead to overheating and failure. Conversely, a ring terminal that is too large may cause excessive wear on the conductor insulation or even lead to insulation failure. To prevent such problems, it’s imperative to select a ring terminal that matches the wire gauge according to the national electrical codes and standards. Additionally, corrosion can be a significant concern in environments with high humidity or salt content in the air. Regular inspection and application of appropriate corrosion-resistant compounds can mitigate this issue and ensure the longevity and reliability of ring terminal connections in control panel wiring.