Modernizing Elegance: The Role of Jewelry Casting in Contemporary Design
Jewelry casting is an integral aspect of modern jewelry design, encompassing traditional methods li…….
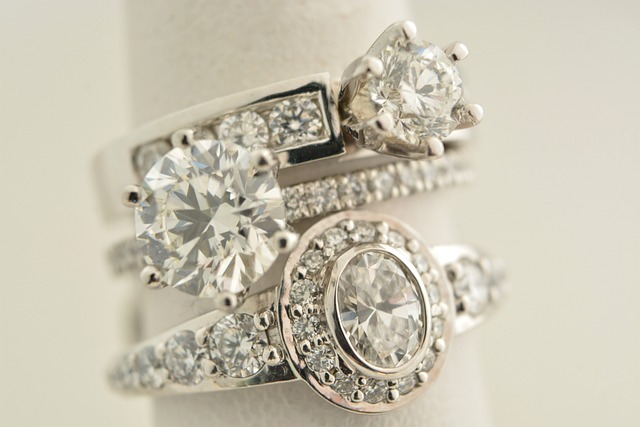
Jewelry casting is an integral aspect of modern jewelry design, encompassing traditional methods like lost-wax and investment casting, as well as cutting-edge techniques such as vacuum casting and 3D wax injection molding. These processes enable artisans to craft intricate designs with high precision, utilizing molds to accurately replicate detailed jewelry pieces. Lost-wax casting involves creating a wax model that is encased in refractory material and burned away, while the investment casting method uses a silica slurry mold that hardens to form a cavity for metal. Vacuum casting removes air from the wax before pouring to minimize defects. 3D wax injection molding further enhances these methods by offering unprecedented detail and efficiency, making complex patterns more accessible. As technology advances, jewelry casting continues to evolve, offering innovative solutions that push creative boundaries while honoring a legacy that dates back millennia. These advancements have democratized the design process, allowing jewelers to produce high-quality pieces with greater speed and a wider range of materials. The jewelry industry now benefits from these modern casting techniques, which combine artisanal craftsmanship with technological sophistication to meet the diverse demands of contemporary consumers.
In the realm of fine jewelry design, casting stands as a pivotal technique that marries artistic vision with technical precision. This article delves into the intricate world of jewelry casting, exploring its indispensable role in modern jewelry design. We will traverse the evolution of casting methods, from time-honored traditions to cutting-edge advancements, and uncover the diverse techniques that shape the future of this craft. From the meticulous application of wax injection molding to the intricate art of investment casting, we’ll examine the materials and processes that bring exquisite pieces to life. The integration of 3D printing and sustainable practices further expands the possibilities for jewelers worldwide. As we navigate through the design considerations, economic implications, and regulatory standards, it becomes clear that jewelry casting is a cornerstone of the industry’s innovation and artistry. Join us as we explore the transformative impact of digital design on this ancient technique and highlight case studies of notable designers who have left an indelible mark with their cast creations.
- Overview of Jewelry Casting Techniques
- The Evolution of Jewelry Casting Methods
- Types of Molds Used in Jewelry Casting
- – Wax Injection Molding
Overview of Jewelry Casting Techniques
In the realm of modern jewelry design, casting is a pivotal technique that enables designers to translate their visions into tangible pieces with intricate details and complex structures. Jewelry casting involves creating molds from models of the desired designs, typically made from wax or other materials that can be melted away post-casting. This process allows for the replication of detailed patterns, ensuring each piece maintains the intended precision and aesthetic. There are several casting methods employed in the jewelry industry, including lost-wax casting, investment casting, and vacuum casting. Lost-wax casting, one of the oldest and most widely used techniques, involves a wax model being encased in a refractory material, which, upon heating, vaporizes the wax, leaving a cavity into which molten metal is poured to form the final piece. Investment casting, another variant, uses a slurry of silica or other materials to create a mold that, once set, is burned out to leave a precise cavity for the molten metal. Vacuum casting, a more modern approach, employs a vacuum to remove air and bubbles from the wax before casting, resulting in higher-quality castings with fewer defects. These methods are integral to jewelry casting, allowing designers to produce pieces that range from mass-produced items to highly individualized artisan works. The choice of technique often depends on factors such as the complexity of the design, the type of material used, and the desired outcome in terms of surface finish and detail. As technology advances, new casting methods continue to emerge, offering even greater possibilities for designers to innovate and push the boundaries of jewelry design.
The Evolution of Jewelry Casting Methods
Jewelry casting has undergone significant transformations over the centuries, transitioning from rudimentary practices to sophisticated methods that are integral to modern jewelry design. The earliest casting techniques, such as lost-wax casting, have ancient origins and were employed by civilizations including the Egyptians and Greeks. These traditional methods laid the foundation for contemporary practices, which now incorporate advanced technologies like 3D printing and computer-aided design (CAD). Today, jewelers integrate these cutting-edge tools to create precise and intricate molds that facilitate the production of complex designs with greater efficiency and accuracy. This evolution in casting methods has democratized jewelry design, allowing designers to bring their most elaborate visions to life without the constraints of manual crafting limitations. The integration of high-tech solutions in the casting process has not only expedited the production time but also expanded the variety of materials that can be used, from precious metals like gold and silver to innovative alloys and composites. As a result, the jewelry industry continues to innovate, pushing the boundaries of design and functionality while maintaining the artisanal quality that has defined jewelry casting for millennia.
Types of Molds Used in Jewelry Casting
In the realm of modern jewelry design, jewelry casting plays a pivotal role in shaping the intricate and diverse pieces that adorn wearers today. This process involves creating molds that are crucial for the production of various jewelry items. The types of molds used in jewelry casting can be categorized into investment casting molds and lost-wax casting molds, each with its unique applications and benefits.
Investment casting molds are typically used for more complex designs and larger production runs. These molds are created using a process where a silicone rubber mold is made from an original wax model of the jewelry piece. Once the mold is set, it is filled with a refractory material to form the investment. After curing, the investment mold is heated to burn out the wax patterns, leaving behind a cavity that will be filled with molten metal under high pressure. The resulting pieces are highly detailed replicas of the original design, showcasing the precision and versatility of this casting method.
Lost-wax casting molds, on the other hand, are used for smaller batches or individual pieces. Similar to investment casting, this process begins with a master wax model. However, instead of creating an investment around it, the wax model is affixed to a sprue and flask system that allows for the introduction of molten metal. The wax is then removed, either through melting or by gas pressurization, leaving behind the negative space of the jewelry design within a plaster or resin mold. Once the mold is filled with metal and cooled, the resulting piece is a direct casting of the original wax model, capturing even the finest details. Both methods are integral to the jewelry casting process, enabling designers to bring their visions to life with consistency and complexity that would be challenging to achieve by hand.
– Wax Injection Molding
Jewelry casting has undergone a transformative evolution with the advent of wax injection molding, a technique that significantly enhances the efficiency and intricacy of modern jewelry design. This advanced method allows for the creation of complex patterns and detailed textures that were previously unattainable through traditional lost-wax casting processes. Wax injection molding involves injecting molten wax into a hardened plastic or metal mold, which precisely replicates the designed piece. The precision of this technique enables jewelry designers to produce intricate and elaborate designs with consistent quality and detail. This process is particularly beneficial for high-volume production as it reduces the likelihood of defects and allows for rapid turnaround times. The result is a near-perfect wax model that can be used directly for investment casting or further refined if necessary. The ability to reproduce intricate patterns at scale has made wax injection molding an indispensable tool in the jewelry casting field, revolutionizing how designers bring their visions to life and cater to diverse consumer preferences.