Mastering Jewelry Casting: Industry Standards and Techniques
Jewelry casting is a fundamental technique in fine jewelry craftsmanship, involving intricate proces…….
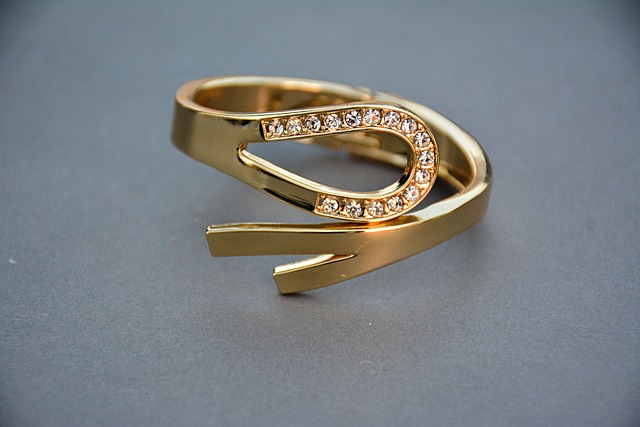
Jewelry casting is a fundamental technique in fine jewelry craftsmanship, involving intricate processes like investment casting and lost-wax casting. Investment casting, or "lost foam," uses a mold made from a foam pattern covered in refractory material to capture fine details with a superior surface finish. Lost-wax casting involves creating a wax replica of the jewelry piece, encased in refractory material to form a mold which, after the wax is removed, allows for molten metal to produce a solidified piece that closely resembles the original design. Both methods are integral to producing a diverse range of jewelry items from classic to elaborate pieces, showcasing the quality and craftsmanship of the jewelry industry. The choice of materials—gold (in varying karats), silver (including sterling), and platinum—each with distinct properties and visual appeal, as well as base metals like pewter and brass for larger-scale production, affects the weight, shine, color, and durability of the final product. Investment cement plays a crucial role in lost-wax casting, providing precision and durability, and must be selected carefully to ensure high standards of quality. Precision and tolerance during the casting process are critical for producing high-quality jewelry that is both durable and aesthetically pleasing, with advancements in CAD/CAM technology enhancing these aspects. The commitment to precision and adherence to stringent industry standards results in jewelry that combines functionality with exquisite design, ensuring customer satisfaction and reinforcing the significance of casting in the fine jewelry sector.
In the intricate art of jewelry making, casting stands as a pivotal technique, blending artistry with precision engineering. This article delves into the industry standards that govern the jewelry casting process, from the selection of materials to the application of advanced technologies. We will explore the traditional lost-wax casting method and its modern enhancements, the critical role of investment cement, the precise requirements for molds and metal alloys, and the stringent quality control measures that ensure each piece reflects excellence. Furthermore, we will examine regulatory compliance, environmental impact, and the transformative effect of 3D printing on this craft. With a comprehensive look at best practices, training, global trends, and a peek into the future, this article provides a comprehensive overview of the jewelry casting industry’s standards and innovations.
- Overview of Jewelry Casting Techniques
- Materials Commonly Used in Jewelry Casting
- The Role of Investment Cement in Lost-Wax Casting
- Precision and Tolerance Standards in Jewelry Casting
Overview of Jewelry Casting Techniques
Jewelry casting is a critical process in the creation of intricate and detailed fine jewelry pieces. This process involves pouring molten metal into a mold to form the desired shape, allowing for precise replication of complex designs. The two primary techniques used in the jewelry casting industry are investment casting and lost-wax casting. Investment casting, also known as the “lost foam” method, uses a foam pattern filled with refractory material, creating an enveloping mold that captures fine details effortlessly. This technique is particularly favored for its ability to produce pieces with a high level of surface finish and detail.
Lost-wax casting is another prevalent jewelry casting technique where a wax replica of the final piece is made and then coated with a refractory material, forming a hardened shell that becomes the mold. Once the mold hardens, it is heated to remove the wax, leaving a cavity exact in shape to the desired jewelry item. The mold is then filled with molten metal, which cools and solidifies into a near-perfect replica of the original wax model. Both methods require meticulous attention to detail and precision, ensuring that the resulting pieces meet the high standards of the fine jewelry industry. These casting techniques are integral to the production of everything from rings and pendants to elaborate statement pieces, showcasing the durability, beauty, and craftsmanship synonymous with jewelry casting.
Materials Commonly Used in Jewelry Casting
In the realm of jewelry casting, a variety of materials are employed to create intricate and durable pieces. The most common materials include precious metals such as gold, silver, and platinum, each chosen for their inherent qualities and aesthetic appeal. Gold is available in different karats, with 24K being pure gold, while 18K and 14K gold are alloys mixed with other metals to enhance durability and strength. Silver, often used in its sterling form, which is an alloy of 92.5% silver and 7.5% other metals like copper, is prized for its affordability and shine. Platinum, known for its robustness and purity, is a favored material due to its white color and hypoallergenic properties. Additionally, base metals such as pewter, brass, and nickel silver, an alloy of copper, nickel, and zinc, are also used in jewelry casting, particularly for mass-produced items where cost efficiency is a priority. Each material brings its own set of characteristics to the final piece, influencing factors like weight, luster, color, and longevity. Jewelry casting processes must be tailored to accommodate these diverse materials, ensuring that the resulting pieces meet industry standards for quality and craftsmanship.
The Role of Investment Cement in Lost-Wax Casting
In the realm of jewelry casting, investment cement plays a pivotal role in the lost-wax casting process. This critical material, specifically formulated for precision casting, serves as a mold that captures the intricate details of the original wax model. When the wax is melted away, the investment cement remains, creating a hollow cavity that perfectly replicates the design’s shape and contours. The quality of the investment cement directly influences the final product’s durability and finish. High-grade investments ensure that the metal cast accurately reflects the artist’s intent, with a fine surface texture that often eliminates the need for extensive post-casting finishing. Selection of the right type of investment cement is crucial, as it must withstand high temperatures without cracking or deforming, and must also allow for consistent and precise pouring of molten metal. The investment material undergoes stringent industry standards to ensure consistency and reliability, making it an indispensable component in the jewelry casting industry.
Advancements in investment cement technology have led to a variety of products designed for different casting applications. These enhancements cater to diverse metal types and casting sizes, from delicate pieces like engagement rings to larger ornamental items. The properties of investment cements, such as their burnout rate and resistance to shrinkage, are meticulously controlled to ensure the highest quality casts. Jewelers and foundry operators must adhere to strict standards when preparing the investment slurry, from the correct mix ratio to the curing time, to achieve a flawless mold. The precision of the casting process is largely dependent on the investment cement’s ability to accurately reproduce the design, which underscores its importance in the jewelry manufacturing industry.
Precision and Tolerance Standards in Jewelry Casting
In the realm of jewelry casting, precision and tolerance standards are paramount for producing high-quality pieces that meet consumer expectations and industry benchmarks. The casting process in jewelry manufacturing involves melting precious metals like gold, silver, and platinum before pouring them into molds to create the desired shapes and designs. To ensure the integrity and consistency of the final products, strict precision standards are applied during every stage of the casting procedure. These standards dictate the exactness required for measurements, temperatures, and mold preparation, which together contribute to the dimensional accuracy and surface finish of the cast items. Tolerance levels are also critical; they define the acceptable deviations from a nominal dimension, allowing for some variation while maintaining the overall quality of the jewelry. Adherence to these tolerance standards is crucial for producing pieces that fit together seamlessly during assembly, such as rings with settings and bands, ensuring that each piece not only reflects the beauty of the design but also the durability and luster expected from fine jewelry.
Advancements in casting technology have led to more precise control mechanisms, which further refine the accuracy of the casting process. These advancements include the use of sophisticated casting machines equipped with computer-aided design (CAD) and computer-aided manufacturing (CAM) capabilities. The integration of these technologies enables jewelry manufacturers to achieve high precision and tight tolerance standards, resulting in consistently excellent outcomes that meet both industry standards and customer satisfaction. The commitment to maintaining these high standards is a testament to the dedication of the jewelry casting industry to crafting pieces that are not only beautiful but also durable and reliable for everyday wear.