Digital Weaving Revolution: Transforming Traditional Craft into Modern Textile Innovation
Digital weaving technology has revolutionized the textile industry by combining advanced computer-ai…….
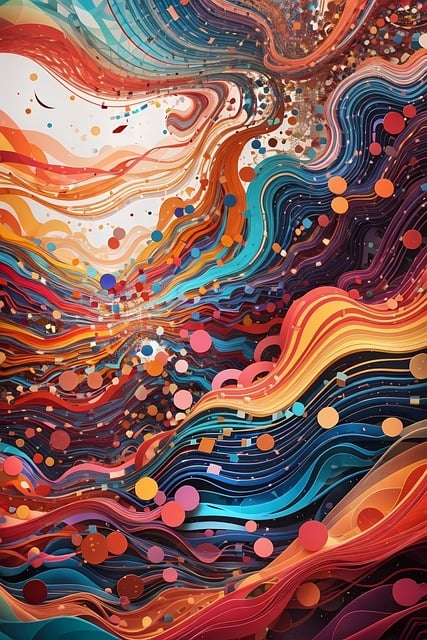
Digital weaving technology has revolutionized the textile industry by combining advanced computer-aided design (CAD) with automated looms, enabling a level of design intricacy and pattern versatility far beyond traditional methods. This innovative approach leverages precise programming to create complex fabric patterns with minimal waste, significantly accelerating production while also empowering designers to push the boundaries of textile artistry. The integration of sensors and automation within the weaving process ensures consistent quality and facilitates real-time monitoring and adjustments, leading to superior fabric quality and operational efficiencies. Digital weaving's adaptability supports mass customization, allowing for individual needs to be met without compromising on speed or quality. This modern fusion of technology with craftsmanship not only enhances the aesthetic and functional aspects of woven fabrics but also sets a foundation for future advancements in smart textiles and sustainable practices within the industry. Keywords: digital weaving, computer-aided design (CAD), automated looms, fabric production efficiency, creative potential in textile design, sensor integration, mass customization, smart textiles.
digital weaving technology has revolutionized the textile industry, offering unprecedented precision, design versatility, and efficiency. This article delves into the transformative journey of weaving, tracing its evolution from traditional looms to the sophisticated digital systems that now shape the fabric of modernity. We’ll explore the intricacies of digital weaving technology, its pivotal role in contemporary textile production, and how it’s reshaping design innovation. From the integration of artificial intelligence to the environmental implications and future trends, this comprehensive guide illuminates the multifaceted impact of digital weaving across various sectors, including fashion, smart manufacturing, and art. Join us as we unravel the threads connecting tradition with technology and examine how mastery of these systems is shaping the craft for the next generation of weavers.
- The Evolution of Weaving: From Traditional Looms to Digital Precision
- Understanding Digital Weaving Technology: A Comprehensive Guide
- Key Components of Digital Weaving Systems
- The Advantages of Digital Weaving in Modern Textile Production
- How Digital Weaving Enhances Design Flexibility and Innovation
The Evolution of Weaving: From Traditional Looms to Digital Precision
The practice of weaving, a craft as ancient as human civilization itself, has undergone a remarkable transformation over the centuries. Traditionally, weaving was conducted on mechanical looms that required skilled artisans to manually operate, thread by thread, creating intricate patterns and textures with a high degree of dexterity and patience. These manual processes, while capable of producing beautiful fabrics, were limited by human precision and the physical constraints of traditional looms. Over time, technological advancements began to interweave with this timeless art, giving rise to automated jacquard looms in the 19th century, which significantly enhanced the complexity and variety of designs that could be produced.
In the modern era, digital weaving technology has revolutionized the industry, bringing unprecedented precision and versatility to the craft. Computer-aided design (CAD) software now allows designers to conceptualize and visualize patterns and textures on screens before they are physically woven. This digital transition has enabled the creation of complex designs with intricate details that were once impossible to achieve. The integration of robotics within looms has further streamlined the process, allowing for 24/7 production capabilities without sacrificing the quality or creativity inherent in hand-woven textiles. Digital weaving technology not only speeds up the production time but also unlocks new possibilities for designers and manufacturers to push the boundaries of what is possible in the realm of woven materials. This technological evolution has positioned weaving at the forefront of digital innovation, ensuring that the craft remains both relevant and integral to the textile industry.
Understanding Digital Weaving Technology: A Comprehensive Guide
Digital weaving technology represents a significant leap forward in the textile industry, blending traditional craftsmanship with advanced digital capabilities to produce intricate patterns and designs with unprecedented precision and versatility. This innovative approach enables weavers to transcend the limitations of manual weaving methods by integrating computer-aided design (CAD) software, which allows for the precise programming of complex patterns that can be woven into fabrics repeatedly and consistently. The result is a diverse range of textiles with customizable features, from the subtle variations in texture to the intricate details of elaborate designs, all produced with great efficiency and minimal waste.
The essence of digital weaving technology lies in its ability to automate and optimize the weaving process, which includes the selection of yarn types, the adjustment of the loom settings, and the monitoring of the fabric’s quality throughout production. This automation not only speeds up the creation of fabrics but also ensures a level of consistency and quality that is difficult to achieve by hand. Moreover, digital weaving opens up new possibilities for designers and artists who can now push the boundaries of textile artistry, leveraging software tools to experiment with new patterns and explore the potential of various materials in ways previously not feasible. This fusion of technology and tradition enhances the capabilities of artisans and sets a new standard for innovation in the weaving domain.
Key Components of Digital Weaving Systems
Digital weaving technology represents a significant advancement in the textile industry, integrating advanced components to automate and enhance traditional weaving processes. At the core of this technology lies the digital control system, which orchestrates the intricate movements of the loom through programmable logic controllers (PLCs) and computer-aided design (CAD) software. This system allows for precise pattern programming, adapting to various weaving structures and designs with ease. The high-speed electronic drives regulate the motion of the shuttle and mechanical components, ensuring synchronization and reducing human intervention to a minimum. Additionally, sensors monitor the weaving process in real-time, providing feedback to adjust tension, yarn path, and density for consistent quality across the fabric.
Sensors and cameras positioned throughout the weaving system collect data on thread consumption, pattern accuracy, and material integrity. This data is critical for maintaining optimal performance and preventing issues such as thread breaks or pattern misalignments. Moreover, digital monitoring systems can predict maintenance needs, alerting operators to potential failures before they cause significant disruptions. The integration of smart technology within the weaving process not only streamlines production but also lays the groundwork for future advancements in customization and sustainability within the textile industry. With these components working harmoniously, digital weaving systems pave the way for a new era of efficiency and innovation in fabric manufacturing.
The Advantages of Digital Weaving in Modern Textile Production
Digital weaving technology has revolutionized the textile industry by introducing a level of precision, efficiency, and versatility that traditional weaving methods cannot match. This modern approach utilizes computer-aided design (CAD) systems to create intricate patterns with ease, allowing for rapid prototyping and testing before actual weaving commences. The integration of sensors and automation in looms enables real-time monitoring and adjustment of the weaving process, leading to consistent quality and reduced material wastage. This not only speeds up production cycles but also significantly lowers costs associated with manual corrections and labor-intensive processes.
Furthermore, digital weaving opens a vast array of design possibilities that were previously unattainable. Designers can now experiment with an extensive range of yarn types, patterns, and colors, pushing the boundaries of creativity in textile production. The technology’s adaptability also allows for mass customization, catering to individual customer preferences while maintaining high production rates. This fusion of technology and tradition not only enhances the aesthetic appeal of woven fabrics but also their functionality, durability, and performance characteristics. Digital weaving stands as a testament to human ingenuity in harmonizing innovation with craftsmanship in the textile realm.
How Digital Weaving Enhances Design Flexibility and Innovation
Digital weaving technology has revolutionized the textile industry by significantly enhancing design flexibility and fostering innovation in ways that were previously unimaginable. Traditional weaving techniques, while rich in history, often limited designers to rigid patterns and materials. Conversely, digital weaving technologies like computer-aided design (CAD) systems and automated jacquard looms allow for intricate and complex designs to be woven with precision and ease. Designers can now experiment with various yarns, textures, and colors, creating unique fabrics that respond to the latest fashion trends or cater to the demands of different industries, such as medical textiles or automotive interiors. The integration of sensors and IoT devices further expands the possibilities, enabling fabrics to be interactive and smart, with applications ranging from wearable technology to architectural applications. This evolution in weaving not only broadens the scope of what is possible but also speeds up the prototyping process, allowing for rapid iteration and a more dynamic exchange between design intent and material outcome, thus propelling the textile industry into a new era of innovation.