Electrical Resistance in Ring Terminals: Understanding Key Factors
Ring terminals, with their circular design and metal bodies, provide secure electrical connections a…….
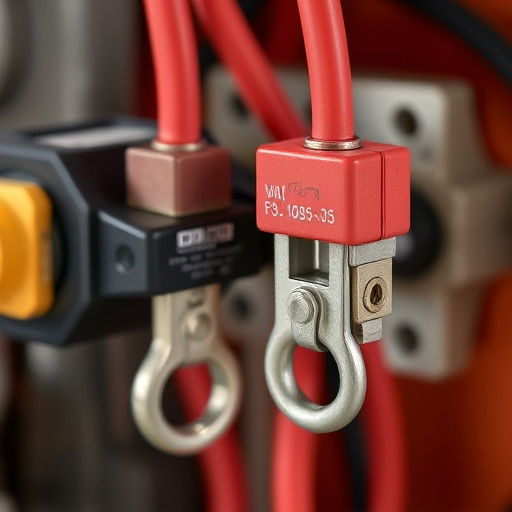
Ring terminals, with their circular design and metal bodies, provide secure electrical connections across industries. Their structural strength prevents short circuits and heat build-up, making them essential for safe current transmission. Electrical resistance, influenced by metal type, dimensions, and surface preparation, is crucial for optimal performance in diverse environments. Regular resistance testing using ohmmeters ensures system reliability by identifying issues early, a vital step in maintaining electrical systems in automotive, industrial, and marine settings.
“Ring terminals, essential components in electrical systems, offer reliable connections through their unique design. This article delves into the intricacies of electrical resistance within these terminals, exploring its fundamental role and impact on performance. We’ll dissect the factors influencing resistance, providing insights for measurement and calculation. Understanding the consequences of high resistance is key to ensuring system reliability. Additionally, we’ll uncover strategies to minimize resistance, highlighting best practices for optimal ring terminal applications.”
- Understanding Ring Terminals: Basic Concept and Structure
- The Role of Electrical Resistance in Ring Terminals
- Factors Affecting Resistance in These Components
- Measuring and Calculating Resistance in Ring Terminals
Understanding Ring Terminals: Basic Concept and Structure
Ring terminals are a type of electrical connection component designed for easy and efficient wiring in various applications. They are characterized by their unique circular or annular shape, which allows them to be securely crimped around wires. This basic concept ensures a robust physical and electrical bond between the terminal and its connected wire, making ring terminals a preferred choice in many industries.
The structure of a ring terminal typically consists of a metal body that is flattened into a thin disk with a central opening. The opening accommodates the insertion of a wire, which is then crimped or compressed within the terminal’s jaws. This compression creates a reliable electrical contact by maximizing the surface area in direct contact with the wire. The design also often includes additional features like tine or wing-like projections that help in holding the wire firmly in place, enhancing the terminal’s overall strength and durability.
The Role of Electrical Resistance in Ring Terminals
In the realm of electrical connectivity, ring terminals play a pivotal role due to their unique design and functionality. These terminals are not just mechanical connectors; they serve as critical components that facilitate the transmission of electrical currents with minimal loss. Electrical resistance, a fundamental property in ring terminals, plays a dual role. On one hand, it ensures that only authorized currents pass through, acting as a safeguard against short circuits and power surges. This feature is particularly crucial in demanding industrial settings where robust connections are non-negotiable.
On the other hand, managing electrical resistance in ring terminals optimizes current flow, preventing excessive heat build-up that could lead to insulation damage or even fires. By carefully controlling this variable, manufacturers can tailor the terminals for specific applications, ensuring top-notch performance and reliability across diverse environments. In essence, understanding and manipulating electrical resistance is key to harnessing the full potential of ring terminals in today’s bustling electrical landscapes.
Factors Affecting Resistance in These Components
Several factors play a significant role in determining the electrical resistance in ring terminals. One of the primary considerations is the material used for manufacturing. Different metals have varying resistivities, with copper and aluminum being commonly used due to their low resistivity, resulting in lower resistance values compared to steel or brass terminals.
Another critical factor is the size and dimensions of the ring terminal, particularly its diameter and thickness. Narrower strands or thinner walls can lead to increased resistance as they limit the flow of current. Conversely, larger diameters promote better conductivity. Additionally, factors like surface finish and cleaning also matter; a well-polished surface ensures minimal contact resistance, whereas oxidation or dirt buildup can significantly impact resistance.
Measuring and Calculating Resistance in Ring Terminals
Measuring resistance in ring terminals is a crucial step in ensuring electrical systems function optimally and safely. This process involves utilizing specialized equipment, such as an ohmmeter or multimeter, to determine the terminal’s resistance value. By applying a small voltage across the terminal and measuring the resulting current, technicians can calculate resistance using Ohm’s Law: Resistance (R) = Voltage (V) / Current (I).
Accurate calculations are essential for identifying potential issues within wiring systems. High resistance in ring terminals may indicate loose connections, corrosion, or damage to the terminal itself, requiring prompt attention. Conversely, low resistance could signal a faulty component or an improperly installed terminal. Regular testing and monitoring of resistance levels help maintain the integrity of electrical systems, ensuring reliable performance in various applications, including automotive, industrial, and marine environments.