Revolutionizing Automotive Design: The Impact of Advanced Weaving Techniques
The automotive industry has significantly advanced with the adoption of composite materials, particu…….
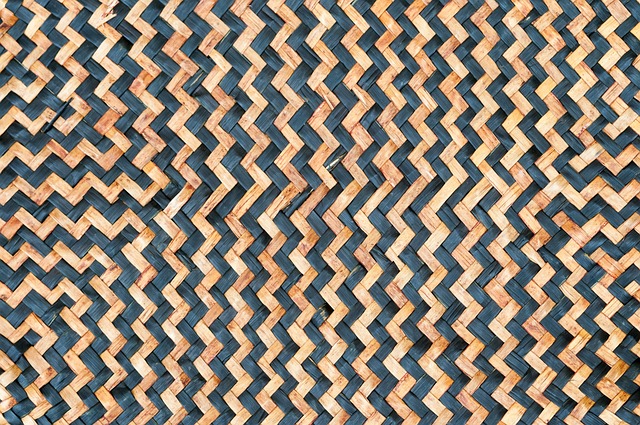
The automotive industry has significantly advanced with the adoption of composite materials, particularly through the enhancement of weaving technology. This evolution has been driven by the need for stronger, lighter vehicles that improve fuel efficiency and align with environmental standards. Sophisticated weaving techniques like Automated Fiber Placement (AFP) and Automated Tape Laying (ATL) have revolutionized production, enabling precise and efficient manufacturing of complex shapes that were previously difficult to fabricate. These methods not only optimize material usage but also contribute to the production of high-performance composite parts integral to vehicle safety and performance. Innovations in weaving, such as 3D textile manufacturing and smart textiles, are poised to further transform automotive engineering, offering new design possibilities and enhancements in performance. The future of automotive weaving technology looks promising, with a continued significant impact on advancements, including the integration of sustainable materials like hemp and flax, and the embedding of functionalities such as sensors directly into textiles. This trajectory indicates a commitment to innovation and sustainability, shaping the next generation of vehicles that are both technologically advanced and environmentally friendly. Keywords: composite materials, weaving technology, automotive manufacturing, lightweighting, efficiency, environmental resilience, advanced weaving methods, smart textiles, sustainable materials.
The interplay of traditional weaving with cutting-edge technology has redefined the automotive industry, leading to safer, more efficient vehicles. This article delves into the transformative impact of advanced composites and weaving techniques on automotive manufacturing. It explores how high-performance fabrics are revolutionizing vehicle design and adherence to safety standards, while also highlighting the innovative strides in weaving that contribute to lightweighting and overall efficiency. Furthermore, it offers a glimpse into the future of sustainable materials and weaving methods poised to reshape the automotive landscape. Join us as we unravel the intricate tapestry of weaving’s role in propelling the industry forward.
- The Evolution of Composites and Weaving Techniques in Automotive Manufacturing
- Integration of Advanced Weaving Technologies in Automotive Part Production
- The Role of High-Performance Fabrics in Vehicle Design and Safety Standards
- Innovations in Weaving for Lightweighting and Efficiency in Automotive Applications
- Future Trends: Sustainable Materials and Weaving Methods in the Automotive Industry
The Evolution of Composites and Weaving Techniques in Automotive Manufacturing
The integration of composites into automotive manufacturing has been a transformative journey marked by significant advancements in weaving techniques. Initially, composites were used sparingly, primarily for niche applications due to their high strength-to-weight ratio and resistance to environmental stressors. As the industry progressed, the demand for lighter yet stronger materials to improve vehicle performance and fuel efficiency propelled innovation. Traditional weaving methods gave way to advanced techniques such as automated fiber placement (AFP) and automated tape laying (ATL), which significantly enhanced the precision and efficiency of composite part production. These methodologies not only optimize material usage but also allow for complex geometries that were previously unattainable with traditional materials like steel and aluminum. The evolution of weaving techniques has been instrumental in enabling the automotive sector to meet stringent weight reduction targets while maintaining high standards of safety and durability. Today, sophisticated weaving technologies, including 3D textile manufacturing and smart textile systems, are being explored for their potential to further revolutionize the automotive industry, offering new possibilities for design and performance. The ongoing development in this field suggests that composites and their associated weaving techniques will continue to play a pivotal role in shaping the future of automotive engineering.
Integration of Advanced Weaving Technologies in Automotive Part Production
The automotive industry’s evolution has been marked by a relentless pursuit of innovation, with advanced weaving technologies playing a pivotal role in this transformation. These sophisticated weaving techniques have revolutionized the production of automotive parts, enhancing their performance and durability. Traditional weaving methods have given way to high-speed, high-precision machinery that can create complex geometries and materials with unprecedented consistency. This integration enables the manufacturing of lightweight yet robust components, such as composite car body panels and seat structures, which are critical for improving fuel efficiency and reducing emissions in line with environmental regulations. The precision of modern weaving systems also facilitates the incorporation of multifunctional elements within the fabric, allowing for parts that not only serve a structural purpose but can also integrate sensors and electronic components, thus paving the way for the development of smart vehicles with adaptive capabilities.
Furthermore, the adoption of advanced weaving technologies has significantly reduced production times and costs, making it a cost-effective solution for mass manufacturing. These technologies are not limited to the production of textile-based parts; they also extend to the creation of metallic components through techniques like metal weaving, which offers new design possibilities and material properties that were previously unattainable. The automotive sector’s embrace of these advanced weaving methods underscores a commitment to innovation and excellence, ensuring that vehicles are not only safe and reliable but also at the forefront of technological integration, setting new standards in the industry.
The Role of High-Performance Fabrics in Vehicle Design and Safety Standards
High-performance fabrics have become integral components in vehicle design, offering solutions that enhance both aesthetics and functionality. The intricate process of weaving these materials involves the precise interlacing of yarns to achieve specific properties tailored for automotive applications. These advanced textiles are engineered to meet rigorous safety standards, providing occupants with protection against various environmental factors and potential impacts. In the automotive sector, weaving techniques contribute to the creation of airbags that deploy with precision and absorb energy during a collision. The fabrics used in these critical systems must withstand high speeds and forces, ensuring passenger safety without compromising on weight or space. Moreover, the weaving patterns are designed to be both resilient and durable, allowing for repeated use without degradation. This durability is not only crucial for safety-critical components but also extends to other areas within the vehicle where high-performance fabrics are employed, such as in seating, acoustic management, and even in the design of advanced driver-assistance systems (ADAS). The integration of these engineered textiles into various aspects of vehicle construction underscores their significance in modern automotive design and the continuous innovation within the industry to meet evolving safety and performance demands.
Innovations in Weaving for Lightweighting and Efficiency in Automotive Applications
The integration of advanced weaving techniques has significantly impacted the automotive industry, particularly in the realm of lightweighting and efficiency. Innovations in weaving technology have led to the development of composite materials that offer remarkable strength-to-weight ratios, essential for reducing vehicle weight without compromising on durability. These high-performance fabrics are woven with precision to include reinforcements such as carbon fiber and aramid yarns, which are then used in critical components like body panels, chassis, and even the structural elements of electric vehicle batteries. The weaving process is meticulously controlled to optimize material orientation, thereby enhancing the material’s properties to withstand high stresses and environmental challenges. This not only contributes to the overall efficiency of the vehicles but also extends their lifespan, making the automotive applications more sustainable.
The evolution of weaving techniques in the automotive sector is a testament to the continuous pursuit of innovation aimed at improving vehicle performance and fuel efficiency. Manufacturers are increasingly adopting these advanced woven materials due to their superior properties, including lower density and higher specific strength. The weaving industry has risen to this challenge by leveraging technologies such as automated fiber placement (AFP) and automated tape laying (ATL), which ensure consistent and precise material layering. These processes allow for the production of complex geometries with minimal waste, further enhancing efficiency. As a result, the automotive industry benefits from lighter vehicles that consume less fuel, emit fewer emissions, and offer superior handling and safety features, all of which are critical in today’s eco-conscious market.
Future Trends: Sustainable Materials and Weaving Methods in the Automotive Industry
The automotive industry is poised on the cusp of a significant transformation, with sustainable materials and advanced weaving methods at the forefront of innovation. As environmental concerns escalate, the demand for eco-friendly vehicles has surged, prompting manufacturers to explore alternative materials that are both durable and sustainable. Hemp, flax, and recycled plastics are gaining traction as viable alternatives to traditional fibers and petroleum-based products. These materials not only reduce the carbon footprint but also offer a unique texture and strength that can enhance the structural integrity of vehicles.
Concurrently, the integration of cutting-edge weaving techniques is revolutionizing the production of automotive components. Automated looms and smart textile technologies are enabling manufacturers to create complex fabric structures with precision and efficiency. These advanced weaving methods allow for the incorporation of functional elements such as sensors and electronic components directly into the fabrics. This synergy between sustainable materials and sophisticated weaving techniques is paving the way for a new era in automotive design, where safety, performance, and environmental responsibility are seamlessly interwoven. The automotive industry’s commitment to these trends underscores a shift towards a more sustainable and technologically advanced future.