Mastering Jewelry Casting: Defect Prevention and Quality Assurance
???????????????????????????????In the intricate world of jewelry production, casting defects can mar…….
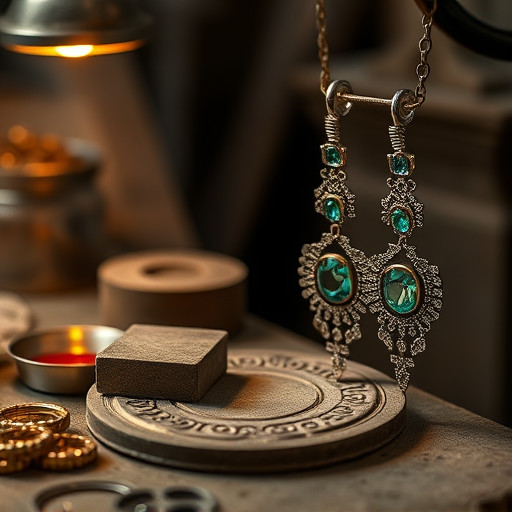
In the intricate world of jewelry production, casting defects can mar perfection. This comprehensive guide delves into the heart of this pervasive issue, exploring common causes and diverse types of jewelry casting defects. We analyze the significant impact on quality and customer satisfaction, highlighting advanced techniques to minimize and detect these flaws. Furthermore, best practices for stringent quality control in jewelry production are dissected, empowering artisans to achieve unparalleled craftsmanship.
- Understanding Jewelry Casting Defects: Common Causes and Types
- The Impact of Defects on Jewelry Quality and Customer Satisfaction
- Advanced Techniques to Minimize and Detect Casting Defects
- Best Practices for Quality Control in Jewelry Production
Understanding Jewelry Casting Defects: Common Causes and Types
Understanding jewelry casting defects is crucial for any jeweler or manufacturer. These defects can arise from various factors during the casting process, leading to imperfections in the final product. Common causes include issues with mold preparation, such as air pockets or improper material selection, which can result in porosity and surface flaws. Additionally, temperature control and metal flow play significant roles; inaccurate temperatures or uneven metal distribution can cause defects like misalignment, voids, or even cracking.
The types of casting defects are diverse. Porosities, for instance, appear as tiny holes or cavities within the metal, often due to trapped air. Misalignments happen when parts of the cast piece fail to fit perfectly together. Other common issues include surface imperfections like roughness or unevenness, and structural weaknesses like voids or cracks that can compromise the integrity of the jewelry piece. Identifying these defects requires careful inspection and understanding of casting techniques to ensure high-quality, defect-free jewelry production.
The Impact of Defects on Jewelry Quality and Customer Satisfaction
Defects in jewelry casting can significantly impact the overall quality and customer satisfaction. Even minor imperfections, such as air bubbles or uneven wall thickness, can detract from the aesthetics and durability of a piece, affecting its market value. In the highly competitive luxury goods industry, where craftsmanship and attention to detail are paramount, these defects can lead to loss of trust among discerning customers who expect perfection in their purchases.
When casting defects go unnoticed or unaddressed, they can result in inconsistent product quality, damaging the reputation of the jewelry brand or manufacturer. Ensuring high-quality castings through meticulous techniques and rigorous quality control measures is essential to maintaining customer satisfaction and fostering long-term loyalty. By minimizing casting defects, jewelry makers can deliver superior products that meet or exceed expectations, solidifying their position in a competitive market.
Advanced Techniques to Minimize and Detect Casting Defects
Best Practices for Quality Control in Jewelry Production
In the meticulous world of jewelry casting, quality control is paramount. The best practices involve a multi-step process that begins with material selection and ends with stringent post-production checks. Skilled artisans should adhere to precise recipes for metal alloys, ensuring consistency in composition to maintain cast integrity. Cleanliness is next to godliness; maintaining a sterile environment prevents unwanted contaminants from infiltrating the molten metal.
Visual inspections are crucial after casting, looking for any visible imperfections such as air bubbles, misalignments, or structural weaknesses. Ultrasonic testing and X-ray imaging can detect subtler issues. Furthermore, regular calibration and maintenance of casting equipment ensure accurate temperature control and precise mold replication. These stringent measures guarantee that each piece of jewelry produced meets high-quality standards.