Unlocking Industrial Efficiency: Exploring Ring Terminals’ Power
Ring terminals are industrial wiring components renowned for their reliability and efficiency in dem…….
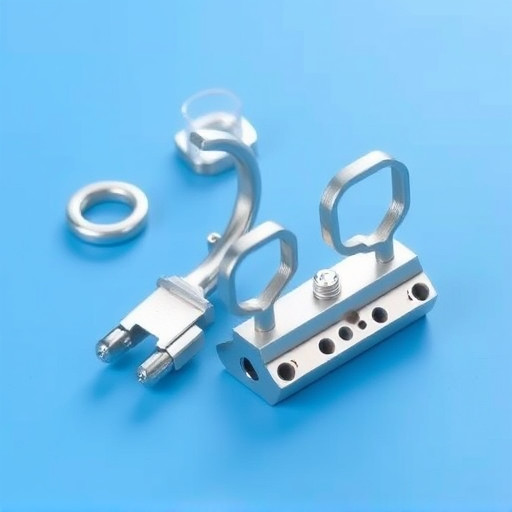
Ring terminals are industrial wiring components renowned for their reliability and efficiency in demanding applications. They securely terminate wires through crimping or soldering, offering robust connections that withstand extreme conditions. With various types catering to specific needs (crimping, soldering, screw, pressure-fit), ring terminals enhance operational productivity by minimizing maintenance downtime. Selection requires understanding voltage, current rating, environmental factors, and mechanical demands, while installation necessitates preparation, specialized tools, safety precautions, and regular maintenance. In industries like mining and manufacturing, ring terminals ensure smooth operation by securing wires, preventing failures, and enabling efficient assembly/disassembly.
Ring terminals have established themselves as indispensable components in industrial applications, offering a reliable and efficient means of electrical connection. This comprehensive guide delves into the world of ring terminals, exploring their definition, functionality, and myriad benefits for industries. From understanding the different types to crucial selection criteria, installation best practices, and real-world success stories, this article is your go-to resource for everything related to ring terminals.
- Understanding Ring Terminals: Definition and Basic Functionality
- Key Advantages of Using Ring Terminals in Industrial Settings
- Types of Ring Terminals: A Comprehensive Overview
- Selection Criteria for Choosing the Right Ring Terminal for Your Application
- Installation, Maintenance, and Safety Precautions for Ring Terminals
- Real-World Applications: Success Stories of Ring Terminals in Heavy Industries
Understanding Ring Terminals: Definition and Basic Functionality
Ring terminals are a type of electrical connection device used in industrial applications for reliable and efficient wiring. They are designed to terminate wires, providing a secure and durable joint that withstand high currents and severe environmental conditions. By crimping or soldering the wire to the terminal, these devices ensure consistent performance and minimize the risk of connections failing.
The basic functionality of ring terminals involves creating an electrical path by encircling the wire with a metal contact. This design allows for easy installation and removal, making them versatile for various industrial needs. Whether in machinery, automotive systems, or power distribution, ring terminals offer a reliable solution for managing wires, ensuring safety and efficiency in operation.
Key Advantages of Using Ring Terminals in Industrial Settings
In industrial settings, where reliability and efficiency are paramount, ring terminals offer significant advantages. Firstly, they provide a secure connection for wires, ensuring minimal risk of disconnection during operation, which is crucial for maintaining consistent performance in demanding environments. These terminals are designed to withstand harsh conditions, including high temperatures, extreme pressure, and exposure to corrosive substances, making them an ideal choice for various industrial applications.
Another key benefit is their speed and ease of installation. Ring terminals allow for quick and precise termination of wires without the need for specialized tools or extensive training. This efficiency reduces downtime during maintenance or upgrades, contributing to overall operational productivity. Moreover, their compact size and organized structure help in managing cable harnesses effectively, ensuring a neat and tidy workshop or facility layout.
Types of Ring Terminals: A Comprehensive Overview
Ring terminals, a fundamental component in industrial wiring, come in various types tailored for specific applications. Among them, crimping terminals offer quick and efficient connections, ideal for high-speed assembly lines where speed and reliability are paramount. Soldering terminals, on the other hand, provide robust bonds suitable for extreme temperatures or corrosive environments, often found in manufacturing facilities dealing with hazardous materials.
For applications requiring versatile connectivity, screw terminals stand out. They accommodate a wide range of wire sizes and offer secure, adjustable connections, making them popular in diverse industrial settings from electrical control panels to robotics assembly. Additionally, pressure-fit ring terminals excel in situations demanding compactness and high current ratings, such as in tight spaces or power distribution units.
Selection Criteria for Choosing the Right Ring Terminal for Your Application
When selecting the right ring terminal for industrial applications, several critical factors must be considered to ensure optimal performance and reliability. First and foremost, understand your application’s specific requirements, including voltage, current rating, environmental conditions (temperature, humidity), and mechanical demands like vibration or shock. Different materials – copper, aluminum, or steel – offer varying levels of conductivity, corrosion resistance, and durability, so choosing the right metal aligns with these needs.
Mechanical design is another key selection criterion. Consider factors such as terminal size, spacing, and the presence of lock mechanisms to prevent accidental disconnection. For harsh environments, sealed or waterproof ring terminals can protect against moisture intrusion. Additionally, understanding the compatibility with your existing wiring systems and tools will streamline installation and maintenance, making it easier to integrate the chosen ring terminals into your industrial setup.
Installation, Maintenance, and Safety Precautions for Ring Terminals
The installation of ring terminals involves careful planning and precision. Typically, this process begins with preparing the cable ends, ensuring they are clean and free from damage. The actual installation requires specialized tools to crimp the terminal onto the cable, creating a secure and reliable connection. It’s crucial to follow manufacturer guidelines and use appropriate crimping techniques to maintain the integrity of the ring terminals, which are designed for heavy-duty industrial applications.
Regular maintenance is vital to extend the lifespan of ring terminals. This includes periodic inspection to detect any signs of wear or damage. Cleaning the terminals and cables can prevent corrosion and ensure optimal conductivity. Safety precautions must be taken during both installation and maintenance, such as wearing protective gear and ensuring adequate ventilation to mitigate risks associated with crimping tools and chemicals used for cleaning. Proper training ensures that these tasks are executed safely and effectively, minimizing potential hazards in industrial settings.
Real-World Applications: Success Stories of Ring Terminals in Heavy Industries
In the demanding and often hazardous environments of heavy industries, reliable electrical connections are paramount for the smooth operation and safety of machinery. Ring terminals have proven their mettle in real-world applications, offering a robust solution for securing wires and cables in extreme conditions. Their versatility is evident across various sectors; from mining operations where harsh terrains and explosive atmospheres pose challenges, to manufacturing facilities with high-speed conveyer belts and powerful machinery, ring terminals ensure electrical continuity without compromise.
Success stories abound of ring terminals enhancing efficiency and safety. In the automotive industry, for instance, they facilitate quick assembly and disassembly of complex electrical systems, streamlining production lines. Similarly, in oil and gas extraction, these terminals contribute to the prevention of short circuits and equipment failures, ensuring the integrity of vital control systems. By withstanding extreme temperatures, corrosive substances, and mechanical stress, ring terminals play an indispensable role in maintaining operational reliability and preventing costly downtime.