Mastering Jewelry Casting: Overcoming Challenges and Technological Advances
The jewelry casting process is a complex interplay of artistry and precision, central to crafting h…….
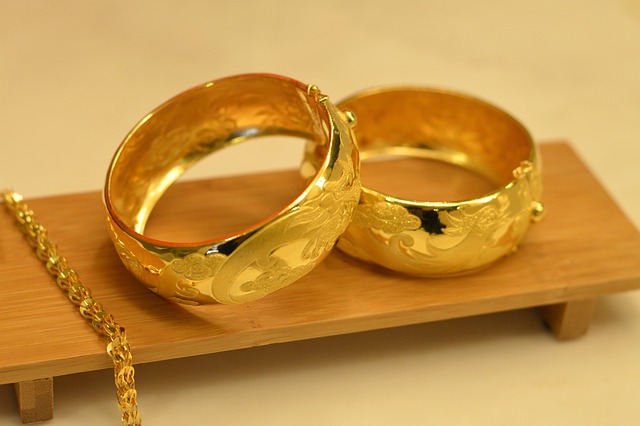
The jewelry casting process is a complex interplay of artistry and precision, central to crafting high-quality fine jewelry. It encompasses a meticulous sequence of steps from designing the initial model to the precise execution of mold making, metal melting, and solidification, with an emphasis on selecting appropriate metal alloys and mastering foundry techniques. The integrity and beauty of the final product are significantly influenced by materials science knowledge, as the choice of material dictates the casting approach and affects durability and aesthetic quality. Wax manipulation skills are crucial for replicating intricate designs within the mold, and controlling the flow of molten metal is essential to avoid defects like air pockets or incomplete filling. Post-casting, jewelry undergoes cleaning, finishing, and polishing to achieve a flawless surface. The discipline of jewelry casting demands a delicate balance of artistic sensibility with meticulous technical expertise, consistently producing high-quality outcomes.
The selection of materials for casting is critical, with gold, silver, platinum, and palladium being popular choices, each with distinct properties that impact castability. Gold's lower melting point requires precise temperature control to prevent surface oxidation, while silver's rapid cooling rate can lead to porosity if not managed correctly. The choice between casting methods—lost-wax, investment, or sand casting—depends on the thermal properties and compatibility of these materials with the process. Emerging materials like titanium introduce new challenges due to their higher melting points and reactive nature.
Recent advancements in 3D printing technologies have revolutionized the jewelry casting process, enhancing both slip casting and investment casting techniques. Slip casting now benefits from more precise, high-quality molds, which mitigate traditional issues of warping or cracking. Investment casting has been transformed by CAD software and 3D printing, enabling rapid prototyping and the creation of detailed wax models, streamlining the transition from design to final product. These innovations have led to a wider array of finely crafted jewelry options at potentially lower production costs, enriching the market with diverse designs and alloy combinations.
The challenges of achieving high-quality castings are addressed by preventing issues such as misruns, air pockets, and uneven material thickness. Careful alloy selection, optimal working temperatures, and vented flask designs are employed to reduce misruns and air pockets. Precise mold preparation, incorporating advancements in modeling software, helps compensate for material shrinkage during cooling, enhancing the durability and aesthetic appeal of cast jewelry pieces. These techniques significantly contribute to the excellence within the jewelry casting sector.
Craftsmanship and artistry converge in the intricate process of jewelry casting, a technique pivotal to bringing designers’ visions to life. This article delves into the nuances of jewelry casting, exploring the complexities inherent in the process, the critical role of material selection, and the transformative impact of technological advancements. We will compare traditional methods like slip casting with cutting-edge investment casting, offering insights into their distinct applications and benefits. Moreover, we provide a troubleshooting guide to help artisans overcome the common challenges faced in this delicate craft, ensuring each piece of jewelry is cast with precision and elegance.
- Understanding the Jewelry Casting Process and Its Complexities
- Material Selection and Its Impact on Casting Outcomes
- Technological Advancements in Jewelry Casting: Slip Casting vs. Investment Casting
- Overcoming Challenges: A Comprehensive Guide to Troubleshooting Common Issues in Jewelry Casting
Understanding the Jewelry Casting Process and Its Complexities
The jewelry casting process is a finely tuned craft that blends artistry with technical precision. At its core, jewelry casting involves creating a mold from a model of the desired piece, melting metal to fill this mold, and then removing the metal once it has solidified to reveal the finished jewelry item. This intricate process requires a deep understanding of materials science and foundry techniques. The choice of material—be it gold, silver, or another precious metal—influences the casting method and affects the final product’s quality and durability. A critical aspect of jewelry casting is the creation of the mold, which must accurately reflect the piece’s intricate design. This requires the caster to have a high level of skill in manipulating wax or other mold materials to replicate every detail, including textures and fine lines. The fluidity of the molten metal as it fills the mold is also paramount; too slow and the metal may solidify before filling the mold completely, too fast and it could cause turbulence leading to air pockets or imperfections. After casting, the piece must be cleaned, finished, and polished to achieve a high-quality, wearable jewelry item. Throughout this process, the caster must navigate various challenges such as alloy composition, mold material selection, and the manipulation of heat to ensure consistency and quality in each cast piece. Mastery of jewelry casting requires a blend of artistic intuition and technical know-how, making it a complex but rewarding endeavor for those skilled in this craft.
Material Selection and Its Impact on Casting Outcomes
In the realm of jewelry casting, material selection is a pivotal factor that influences the outcome of the final piece significantly. Not all materials respond equally to the heat and pressure applied during the casting process. Metals commonly used in jewelry casting include gold, silver, platinum, and palladium, each with distinct properties that affect how they flow into molds. Gold, for instance, has a lower melting point than platinum but requires precise temperature control to avoid surface oxidation and ensure a high-quality cast. Silver, with its faster cooling rate, can trap porosity if not cooled adequately, which is critical for the integrity of the jewelry. The choice between lost-wax casting, investment casting, or sand casting methods also depends on the material’s behavior at elevated temperatures and its compatibility with these processes. For example, materials like titanium, while not traditionally used in jewelry, are gaining attention for their strength and unique aesthetic; however, they present unique challenges due to their higher melting points and reactivity. Understanding the nuances of each material is essential for jewelry caster’s success, as it directly influences the durability, appearance, and overall quality of the finished piece. Jewelry makers must consider factors such as material density, thermal conductivity, and the potential for alloying with other metals to achieve the desired outcome in their casting endeavors. This careful selection process ensures that each piece not only meets the high standards expected in fine jewelry but also allows artisans to innovate and create unique designs that reflect the quality and craftsmanship of the jewelry casting process.
Technological Advancements in Jewelry Casting: Slip Casting vs. Investment Casting
In the realm of jewelry creation, technological advancements have significantly influenced the art of casting. Jewelry casting techniques like slip casting and investment casting offer distinct advantages and challenges. Slip casting, which involves molding an object from a liquid clay slurry that is poured into a plaster cast and allowed to dry, has traditionally been used for smaller jewelry pieces. This method allows for the creation of intricate designs with complex geometries. However, it requires precise control over the slip’s composition and drying process to avoid warping or cracking. The advent of technological innovations in 3D printing has revolutionized slip casting by enabling more accurate and detailed molds, leading to higher-quality castings and reducing trial and error in the production process.
In contrast, investment casting, also known as lost-wax casting, is a more intricate technique where a wax model of the desired jewelry piece is created, coated with a refractory material, and then heated to burn out the wax, leaving a mold into which molten metal is poured. This method is capable of producing highly detailed and complex pieces with fine finishes. The integration of advanced computer-aided design (CAD) software and 3D printing technology has enhanced investment casting by allowing for rapid prototyping and precise model making. These advancements have shortened the time from design to finished product, enabling jewelry artisans to experiment with new designs and alloy compositions that were previously not feasible. This has led to a surge in the variety and quality of jewelry available on the market, as well as a reduction in production costs over time.
Overcoming Challenges: A Comprehensive Guide to Troubleshooting Common Issues in Jewelry Casting
In the intricate process of jewelry casting, artisans and professionals often encounter a variety of challenges that can affect the quality, integrity, and aesthetics of the final piece. To ensure successful outcomes in jewelry casting, it is crucial to address issues promptly and effectively. Common difficulties such as misruns, air pockets, and inconsistent material thickness can be resolved through meticulous preparation and technique refinement. Misruns, where metal does not fill a mold cavity completely or partially, are often due to improper temperature control or incompatible materials. To prevent this, it is essential to carefully select alloy compositions that match the specific characteristics of the casting process being used. Additionally, maintaining an optimal working temperature and allowing the material to reach equilibrium before pouring can significantly reduce the likelihood of misruns.
Air pockets, another frequent problem, occur when vapors or gases are trapped within the molten metal as it solidifies. This issue can be mitigated by using a vented flask design or by implementing ‘slush’ casting techniques that allow for the removal of air before the metal solidifies. For thickness inconsistencies, which can lead to weak points in the jewelry item, attention must be given to the mold preparation. Ensuring accurate dimensions and a uniform wall thickness are key. Utilizing advanced modeling software can aid in designing molds with precise specifications that account for material shrinkage during cooling. By mastering these troubleshooting techniques, jewelers can enhance the quality of their cast pieces, leading to more durable, attractive, and high-quality finished products in the jewelry casting industry.