Hardware Brackets: Essential Support in Industrial Settings
Hardware brackets are essential components in industrial support systems, offering stability and str…….
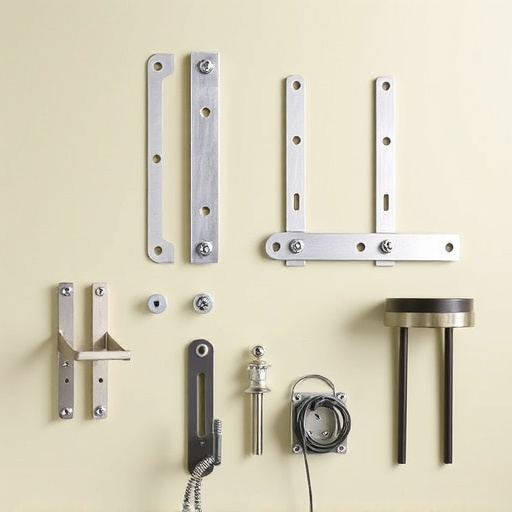
Hardware brackets are essential components in industrial support systems, offering stability and structural integrity for machinery and equipment. They come in various types (L-brackets, I-beam, U-brackets) catering to diverse attachment needs on manufacturing floors and construction sites. Material selection, such as stainless steel or heat-treated steels, ensures durability against environmental challenges. Regular safety testing, inspections, and maintenance by certified professionals guarantee structural integrity and operational safety. Recent advancements provide customizable, innovative solutions optimizing space, performance, stability, and efficiency. Best practices for hardware bracket placement, secure fastening, regular inspections, and structured maintenance plans ensure long-lasting industrial equipment operation.
Industrial settings demand robust support systems, and at the heart of these solutions are hardware brackets—essential components that ensure equipment stability. This article delves into the critical role of hardware brackets in industrial environments, exploring their diverse types, material choices, safety standards, and innovative designs. From customization options to installation best practices, learn how these unassuming brackets drive operational efficiency and safety in demanding industrial applications.
- The Role of Hardware Brackets in Industrial Equipment Support
- Types and Applications of Different Bracket Designs
- Material Considerations for Durability in Harsh Environments
- Safety Standards and Regulations for Industrial Mounting Solutions
- Innovations in Hardware Brackets: Customization and Functionality
- Best Practices for Installation and Maintenance Strategies
The Role of Hardware Brackets in Industrial Equipment Support
Hardware brackets play a pivotal role in industrial equipment support, offering crucial stability and structural integrity in demanding environments. These essential components are designed to securely attach and position various parts within machines, ensuring optimal performance and longevity. By distributing weight evenly and preventing unwanted movement, hardware brackets minimize the risk of mechanical failures and enhance overall equipment effectiveness.
In industrial settings, where machinery often operates at high speeds and under intense conditions, reliable hardware brackets become even more critical. They are versatile tools, accommodating a wide range of attachment needs and allowing for easy adjustments to accommodate different machine configurations. This adaptability contributes significantly to the flexibility and maintainability of industrial systems, making them indispensable for various applications, from manufacturing floors to construction sites.
Types and Applications of Different Bracket Designs
In industrial settings, hardware brackets serve as essential components for securing and supporting various structures, machinery, and equipment. These versatile pieces of metal or plastic come in diverse types, each designed to cater to specific needs. One common category is the L-brackets, known for their simple yet effective design, often used for mounting shelves, guards, or panels onto walls or other surfaces. Another type, the angle brackets, offer added stability due to their inclined shape, making them ideal for bearing heavy loads and connecting structural elements.
Custom bracket designs are also prevalent in industries requiring specialized support systems. For instance, custom I-beam brackets can be crafted to hold and reinforce specific types of machinery, ensuring safety and longevity. Similarly, U-brackets find application in creating adjustable mounting solutions for dynamic industrial environments, allowing for easy rearrangement or expansion. The choice of bracket design depends on factors like the weight and dimensions of the load, space constraints, and the environment’s demands, ultimately contributing to efficient workplace layout and equipment functionality.
Material Considerations for Durability in Harsh Environments
In industrial settings, where equipment is subjected to harsh conditions like extreme temperatures, humidity, and constant wear, selecting durable materials is paramount. Hardware brackets, integral components often overlooked, play a crucial role in ensuring machinery longevity. The right choice of materials for these brackets can significantly mitigate environmental factors’ detrimental effects. For instance, corrosion-resistant metals like stainless steel or aluminum alloys are ideal for wet or salty environments to prevent rust and maintain structural integrity.
Additionally, considering factors such as fatigue resistance and impact strength is essential. High-quality, heat-treated steels can withstand frequent loading and unloading, preventing bracket failure over time. These material considerations, when applied to hardware brackets, contribute to the overall durability of industrial equipment, reducing maintenance needs and operational downtime in challenging environments.
Safety Standards and Regulations for Industrial Mounting Solutions
In industrial settings, ensuring safety through robust mounting solutions is paramount. Hardware brackets play a crucial role in securing equipment and machinery, preventing accidents and potential damage. To maintain a safe environment, adhering to stringent safety standards and regulations is imperative. These guidelines encompass rigorous testing for load capacity, structural integrity, and compliance with industry-specific requirements.
Regular inspections and proper maintenance of hardware brackets are essential practices. Employing certified professionals ensures that mounting solutions meet the necessary safety benchmarks. By prioritizing these standards, industrial facilities can create a secure working environment, minimize risks, and optimize the lifespan of their equipment.
Innovations in Hardware Brackets: Customization and Functionality
In recent years, innovations in hardware brackets have brought a new level of customization and functionality to industrial settings. These advanced brackets are designed to cater to the diverse needs of modern machinery, allowing for easier installation, maintenance, and upgrades. With customizable dimensions, materials, and mounting options, manufacturers can now create tailored solutions that optimize space and enhance performance.
The use of innovative hardware brackets offers numerous benefits, including improved stability and weight distribution, enhanced safety features, and reduced assembly times. By incorporating these brackets into industrial designs, companies are able to streamline their operations, increase efficiency, and ensure the longevity of their equipment. This evolution in hardware technology is revolutionizing the way industries approach machinery setup and maintenance.
Best Practices for Installation and Maintenance Strategies
When implementing installation and maintenance strategies in industrial settings, adhering to best practices is paramount for ensuring efficiency, safety, and longevity of equipment. One critical aspect is proper hardware bracket placement. Brackets should be securely fastened, aligned with manufacturer recommendations, and installed by trained personnel using appropriate tools to prevent damage or instability. Regular inspections are vital to identify wear and tear, loose connections, or corrosion, allowing for timely replacement or reinforcement.
For maintenance, a structured plan including preventive measures is key. This involves regular cleaning, lubrication, and part checks. Utilizing hardware brackets for secure storage of spare parts during maintenance reduces the risk of damage or misplacement. Additionally, implementing digital tracking systems for inventory management enhances efficiency, ensuring quick access to necessary parts when repairs are required.
In industrial settings, hardware brackets play a pivotal role in supporting and securing equipment. This article has explored various aspects of these essential components, from different bracket designs and material choices to safety standards and innovative customization options. By adhering to best practices during installation and maintenance, industries can maximize the durability and functionality of their hardware brackets, ensuring reliable operations even in harsh environments. Understanding these key considerations is crucial for optimizing industrial mounting solutions.