Material Standards: Essential Guide to Hardware Bracket Quality & Innovation
Hardware brackets are vital in various applications, demanding understanding and adherence to materi…….
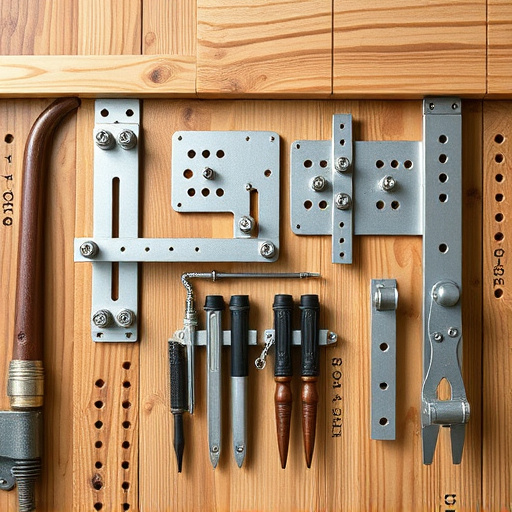
Hardware brackets are vital in various applications, demanding understanding and adherence to material standards for quality and durability. These standards dictate strength, corrosion resistance, and dimensional stability, crucial for reliable performance across industries. Material selection, from stainless steel to composites, is key based on environmental conditions and load capacity. Testing and certification ensure compliance, while best practices maintain material integrity during production. The future holds advancements like 3D printing and lightweight materials, revolutionizing hardware brackets' efficiency and functionality.
Hardware brackets, an essential component in various industries, rely heavily on material standards for durability and reliability. This article delves into the critical role materials play in crafting superior hardware brackets. From understanding foundational concepts to exploring innovative trends, we dissect key factors like material types, selection criteria, testing protocols, and best practices. By embracing these insights, manufacturers can ensure compliance with evolving material standards, ultimately enhancing bracket performance and longevity in diverse applications.
- Understanding Material Standards: A Foundation for Quality Hardware Brackets
- The Role of Materials in Ensuring Durability and Reliability
- Common Types of Materials Used in Hardware Bracket Manufacturing
- Factors to Consider When Selecting Materials for Hardware Brackets
- Testing and Certification: Ensuring Compliance with Material Standards
- Best Practices for Maintaining Material Integrity During Production
- Future Trends and Innovations in Material Standards for Hardware Brackets
Understanding Material Standards: A Foundation for Quality Hardware Brackets
Understanding material standards is paramount in ensuring the quality and durability of hardware brackets, which play a crucial role in various industrial and everyday applications. These standards dictate the properties that materials must meet, such as strength, resistance to corrosion, and dimensional stability, all vital aspects for reliable performance. By adhering to these guidelines, manufacturers can produce hardware brackets that are built to last, enhancing safety and efficiency across diverse sectors.
Material standards not only guarantee the integrity of the brackets but also enable predictability in design and manufacturing processes. This uniformity ensures that hardware brackets function optimally in different environments, from harsh industrial settings to everyday household uses. Ultimately, a solid grasp of material standards forms the foundation for creating robust hardware brackets, contributing to overall product quality and user satisfaction.
The Role of Materials in Ensuring Durability and Reliability
The selection and quality of materials play a pivotal role in determining the durability and reliability of any product, especially in demanding applications like industrial machinery or automotive components. When it comes to hardware brackets, for instance, the materials used significantly influence their structural integrity, load-bearing capacity, and longevity. High-quality metals like stainless steel, aluminium alloys, or even advanced composites are often chosen for their superior strength-to-weight ratios, corrosion resistance, and ability to withstand extreme conditions.
Using robust materials ensures that hardware brackets maintain their structural stability over time, preventing premature failure or deformation under stress. This is particularly crucial in environments where vibrations, temperature fluctuations, or harsh chemicals are present. By investing in the right materials, manufacturers can guarantee that the products they produce will perform reliably for extended periods, enhancing overall system durability and reducing maintenance costs.
Common Types of Materials Used in Hardware Bracket Manufacturing
In the manufacturing of hardware brackets, a variety of materials are commonly employed based on factors such as strength requirements, cost, and aesthetic considerations. Metal, in particular, is a primary choice for its exceptional durability and versatility. Steel, both stainless and carbon, is widely used due to its high tensile strength and resistance to corrosion. Aluminum is also popular, offering lightweight properties without compromising structural integrity. These metals are often chosen for their ability to withstand harsh environmental conditions, making them ideal for outdoor applications.
Other materials frequently utilized in hardware bracket production include plastic and composites. Plastic brackets, typically made from polypropylene or ABS, provide cost-effective alternatives with good impact resistance. Composites, such as fiberglass or carbon fiber reinforced plastics, offer lightweight and robust solutions suitable for demanding industries like aerospace and automotive. The selection of material depends on the specific needs of the application, ensuring optimal performance and longevity of the hardware brackets.
Factors to Consider When Selecting Materials for Hardware Brackets
When selecting materials for hardware brackets, several key factors come into play. First and foremost, consider the environment where the brackets will be used. Different materials offer varying levels of resistance to corrosion, wear, and tear, making some more suitable for outdoor or wet applications than others. For instance, stainless steel is a popular choice due to its high corrosion resistance, while aluminium might be preferable for lightweight, non-corrosive needs.
Another critical aspect is the load capacity required. The intended use of the hardware brackets determines the material’s strength and durability. High-stress applications may demand materials like steel or reinforced metal alloys that can withstand significant weight and pressure without compromising integrity. Conversely, for lighter tasks, cheaper alternatives like plastic or certain types of alloy might suffice, offering both cost-effectiveness and adequate performance.
Testing and Certification: Ensuring Compliance with Material Standards
Testing and certification play a pivotal role in ensuring that hardware brackets and other components adhere to strict material standards. This rigorous process involves a series of meticulous tests designed to verify the quality, durability, and safety of the materials used. From tensile strength assessments to fatigue testing, each component undergoes specialized evaluations to confirm its performance under various conditions. Independent certification bodies validate these results, issuing official documents that attest to the compliance of the hardware brackets with established industry standards.
This adherence to standards is non-negotiable, especially in industries where safety and reliability are paramount. For instance, automotive and aerospace sectors demand that every bracket meets stringent criteria to withstand extreme forces and environmental conditions. Regular retesting and recertification ensure that manufacturers maintain consistent quality control, instilling confidence in both industry professionals and end-users alike.
Best Practices for Maintaining Material Integrity During Production
Maintaining material integrity is paramount during production to ensure product quality and longevity. One of the best practices involves implementing rigorous quality control measures at each production stage, focusing on raw materials and components like hardware brackets. Regular inspections and testing ensure that materials meet predefined standards, identifying any deviations early in the process.
Additionally, proper storage and handling procedures are essential. Materials should be kept in controlled environments to prevent damage or degradation, especially for delicate parts like hardware brackets. Standardized handling protocols, including the use of protective packaging and specialized equipment, reduce the risk of physical harm during transportation and assembly, further safeguarding material integrity.
Future Trends and Innovations in Material Standards for Hardware Brackets
The future of hardware brackets is poised for significant advancements, driven by evolving material standards and innovative technologies. One prominent trend is the increasing adoption of lightweight yet robust materials such as advanced composites and high-strength alloys, which promise to enhance performance while reducing weight in various industries, including automotive and aerospace. These materials offer improved strength-to-weight ratios, enabling manufacturers to create more efficient and sustainable hardware brackets.
Furthermore, additive manufacturing (3D printing) is expected to play a pivotal role in shaping the future of hardware brackets. This technology allows for precise customization and complex geometries, leading to lighter, stronger, and more cost-effective bracket designs. As material science continues to advance, we can anticipate even more groundbreaking innovations that will further elevate the standards for hardware brackets, ensuring they meet the stringent demands of modern applications across diverse sectors.
In conclusion, understanding material standards is paramount for creating robust and reliable hardware brackets. From the foundational knowledge of material properties to best practices in production, each step ensures the longevity and performance of these essential components. As technology advances, continued innovation in materials will further enhance durability and open new possibilities in hardware bracket design. Staying informed about industry trends and adhering to strict testing and certification protocols remain key to maintaining quality standards in the manufacturing process.