Insulated vs Non-Insulated Ring Terminals: Pros, Cons & Choosing
Ring terminals provide essential electrical connections, available as insulated or non-insulated var…….
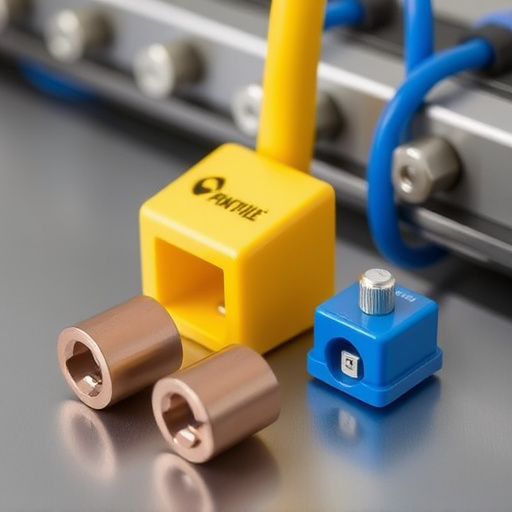
Ring terminals provide essential electrical connections, available as insulated or non-insulated varieties. Insulated options protect against shorts and moisture, ideal for challenging environments, while non-insulated terminals are better for dry, accessible locations. Choosing the right type ensures reliable wiring and safety in diverse applications, with insulated terminals offering enhanced durability, safety, and reliability compared to non-insulated alternatives, especially in demanding settings. Consider environmental factors: insulated for outdoor/moist use and non-insulated for dry indoor conductivity.
“Ring terminals, essential components in electrical wiring, come in two main varieties: insulated and non-insulated. Understanding these differences is crucial for any project, from automotive repairs to residential installations. This article provides a comprehensive guide, delving into the basics of ring terminals, exploring the role of insulation, comparing advantages and disadvantages, and offering insights to help you choose between insulated and non-insulated options for your specific needs.”
- Understanding Ring Terminals: A Basic Overview
- The Role of Insulation in Electrical Connections
- Advantages of Insulated Ring Terminals
- Disadvantages and Considerations for Non-Insulated Terminals
- Choosing Between Insulated and Non-Insulated Ring Terminals for Your Project
Understanding Ring Terminals: A Basic Overview
Ring terminals are a type of electrical connection used in various wiring applications, offering a reliable and secure way to join wires together. They come in two primary types: insulated and non-insulated. The key difference lies in their design and intended use; both serve different purposes in electrical systems.
Insulated ring terminals have a protective covering or insulation around the terminal’s body, which helps prevent accidental shorts and provides added safety when handling. These terminals are commonly used in applications where moisture or corrosion could be an issue, ensuring long-lasting connections. On the other hand, non-insulated terminals lack this protective layer, making them more suitable for dry environments and internal wiring where access and maintenance are easier. Understanding these variations is essential when selecting the right ring terminal for specific electrical projects, ensuring optimal performance and safety.
The Role of Insulation in Electrical Connections
Insulation plays a critical role in electrical connections, especially with ring terminals, by providing protection against current leakage and voltage spikes. When used correctly, insulated ring terminals help maintain the integrity of an electrical circuit, ensuring that power flows efficiently and safely between components. This is particularly important in environments where moisture or other contaminants could compromise the connection.
Non-insulated terminals, while more straightforward in design, are prone to short circuits and voltage surges. In contrast, insulated ring terminals offer a barrier that prevents arcing and electrical discharge, making them ideal for applications requiring high reliability and longevity. This added insulation also contributes to the overall durability of the terminal, reducing the risk of damage or failure over time, especially in harsh conditions.
Advantages of Insulated Ring Terminals
Insulated ring terminals offer several advantages that set them apart from their non-insulated counterparts. One of the primary benefits is enhanced safety. The insulating layer prevents short circuits and reduces the risk of electrical hazards, making them ideal for high-voltage applications. This feature ensures the integrity of connections, especially in harsh environments where moisture or corrosion could compromise the system.
Additionally, insulated ring terminals provide better durability and reliability. The insulation protects against damage caused by vibration, impact, and extreme temperatures, ensuring a stable connection over time. These terminals are versatile and suitable for various industries, including automotive, aerospace, and marine, where reliable and secure connections are paramount.
Disadvantages and Considerations for Non-Insulated Terminals
Non-insulated ring terminals, while offering a straightforward and cost-effective solution for electrical connections, come with several disadvantages. One of the primary concerns is their lack of protection against electrical hazards. Without insulation, there’s an increased risk of electric shock or fires, especially in moist environments or when dealing with high-voltage systems. This makes non-insulated terminals less suitable for applications where safety is paramount.
When considering non-insulated ring terminals, it’s crucial to assess the specific use case and environmental conditions. They might be adequate for low-voltage, dry environments where access for maintenance is frequent. However, in industrial settings or outdoor installations, their lack of insulation can lead to performance issues and safety hazards. Always prioritize proper grounding and regular inspection to mitigate these risks when using non-insulated ring terminals.
Choosing Between Insulated and Non-Insulated Ring Terminals for Your Project
When selecting between insulated and non-insulated ring terminals for your project, consider the specific environment and conditions where they’ll be used. Insulated ring terminals are ideal for applications where components are exposed to moisture or corrosive substances. Their protective insulation barrier prevents electrical current from leaking and reduces the risk of short circuits, making them a safe choice for outdoor installations, humid environments, and applications with frequently accessed connections.
Non-insulated ring terminals, on the other hand, offer better conductivity and are suitable for dry, indoor settings where the risk of moisture exposure is minimal. They’re often preferred in automotive repairs, electrical panels, and other enclosed systems. While they don’t have insulation, non-insulated terminals provide direct contact between the wire and the connection point, ensuring optimal current flow.