Unveiling Advanced Dental Bur Manufacturing Techniques and Future Trends
Dental burs, versatile tools used across various dental procedures, come in multiple types designed…….
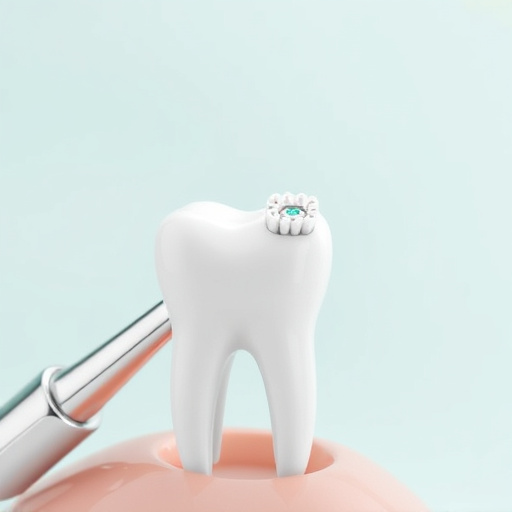
Dental burs, versatile tools used across various dental procedures, come in multiple types designed for specific tasks like cutting, drilling, grinding, and finishing tooth structures. Traditionally manufactured through precise methods including machining, casting, and sintering, modern techniques have enhanced efficiency and accuracy. Integrating dental burs into broader industrial settings and utilizing advanced materials and CAD software improve manufacturing quality and speed. Rigorous manual inspections and standardized testing ensure top-tier tools for dentists, ultimately enhancing patient care. The industry is shifting towards sustainability with eco-friendly materials and efficient production methods like 3D printing and CNC machining with green coolants. Future advancements promise improved performance, longer lifespans, and enhanced accuracy in dental surgeries.
Dental burs are integral tools in dental procedures, offering precise cutting and shaping capabilities. This article delves into the world of manufacturing methods for these intricate devices, exploring traditional processes and modern advancements. From understanding the diverse types of dental burs and their applications to uncovering innovative production techniques, quality control measures, and sustainable approaches, we provide an in-depth look at the evolution of dental bur manufacturing.
- Understanding Dental Burs: Types and Their Applications
- Traditional Manufacturing Processes for Dental Burs
- Modern Production Techniques: Advancements in Technology
- Quality Control Measures in Dental Bur Manufacturing
- Sustainability and Eco-Friendly Approaches in Making Dental Burs
- The Future of Dental Bur Manufacturing: Trends to Watch
Understanding Dental Burs: Types and Their Applications
Dental burs are tiny, rotating tools used in dental procedures for shaping, carving, and polishing tooth structures. They come in various types, each designed for specific tasks. These include cutting, drilling, grinding, and finishing burs, catering to different needs during dental work. Cutting burs, for instance, have a sharp, toothed design for aggressive material removal, while grinding burs are used for more precise shaping and smoothing.
The applications of dental burs span across various dental procedures. They are indispensable in drills, allowing dentists to create complex shapes and remove significant amounts of tooth tissue. In restorative work, they shape and define fillings or crowns. During root canal treatments, specific burs help clean out the pulp chamber and shape the root canal walls. Moreover, polishing burs ensure a smooth finish on restored teeth, enhancing both aesthetics and patient comfort.
Traditional Manufacturing Processes for Dental Burs
Traditional manufacturing processes for dental burs involve a series of precise steps that have been honed over decades. These methods often include machining, where high-speed tools cut and shape metal or ceramic materials to create the intricate designs needed for these small, yet critical instruments. The process demands meticulous attention to detail, as even slight variations can impact the bur’s performance during dental procedures.
One common approach is subtractive manufacturing, which begins with a solid block of material that is gradually reduced through cutting and grinding to form the desired shape. This technique allows for customization and ensures the production of high-quality, precise dental burs tailored to specific surgical needs. Alternative methods may incorporate casting or sintering, offering unique advantages in terms of material composition and complexity of design.
Modern Production Techniques: Advancements in Technology
Modern manufacturing techniques have been revolutionized by advancements in technology, bringing about efficient and precise production processes. One notable example is the integration of dental burs into machining operations. These tiny, specialized cutting tools are designed for intricate dental procedures and have found their way into broader industrial applications. By enabling highly accurate shaping and polishing, dental bur technology enhances the quality and speed of various manufacturing tasks.
Automated systems now utilize these burs to perform complex tasks with minimal human intervention. This not only increases productivity but also ensures consistency in product quality. Advanced materials and computer-aided design (CAD) software further complement these techniques, allowing manufacturers to create intricate parts and components with ease. As technology continues to evolve, we can expect even more innovative manufacturing methods, pushing the boundaries of what’s possible across industries.
Quality Control Measures in Dental Bur Manufacturing
In the intricate world of dental bur manufacturing, ensuring precision and quality is paramount. Quality control measures play a pivotal role in upholding the highest standards for these tiny yet crucial tools. Advanced manufacturing techniques employ sophisticated machinery to cut, shape, and finish dental burs with microscopic accuracy. However, beyond technological prowess, meticulous manual inspections are integral to detect even the slightest imperfections.
Standardized testing protocols verify the integrity of dental burs’ cutting edges, shank dimensions, and material consistency. Each bur undergoes rigorous evaluation to meet stringent quality criteria, guaranteeing their effectiveness during dental procedures. This meticulous attention to detail ensures that dentists receive top-tier tools capable of delivering precise results, ultimately enhancing patient care and treatment outcomes.
Sustainability and Eco-Friendly Approaches in Making Dental Burs
In recent years, the manufacturing industry has witnessed a growing emphasis on sustainability and eco-friendly practices, and dental bur production is no exception. Dental burs, small cutting tools used in various dental procedures, have traditionally been made from hard metal alloys, raising environmental concerns due to their difficult recycling process and potential toxicity. However, manufacturers are now adopting more sustainable approaches. One prominent method involves utilizing bio-based materials, such as biodegradable polymers, to create dental burs. These innovative products not only reduce the environmental impact but also offer excellent performance in terms of cutting efficiency and precision.
Additionally, traditional manufacturing processes often involve high energy consumption and hazardous chemical usage. To counter this, modern producers are exploring green manufacturing techniques like 3D printing and CNC machining with eco-friendly coolants. These technologies minimize material waste, reduce energy requirements, and lower the release of harmful substances into the environment. Furthermore, adopting recycling programs for metal by-products and implementing closed-loop systems ensures that dental bur production contributes positively to sustainability goals, aligning with the growing demand for environmentally conscious manufacturing practices.
The Future of Dental Bur Manufacturing: Trends to Watch
The future of dental bur manufacturing is poised for significant advancements, driven by evolving technologies and an increasing demand for precise, high-quality dental procedures. One prominent trend involves the integration of advanced materials and design techniques to create more durable and precise dental burs. These next-generation tools are expected to offer improved performance, longer lifespans, and enhanced accuracy in intricate dental surgeries. 3D printing, for instance, is emerging as a game-changer, enabling the customization of dental burs tailored to specific patient needs and complex oral geometries.
Additionally, there’s a growing emphasis on minimizing the environmental impact of manufacturing processes. Sustainable practices, such as the use of eco-friendly materials and efficient production methods, are likely to become more prevalent in dental bur production. As technology continues to advance, we can anticipate even more innovative solutions that prioritize both performance and sustainability, shaping a brighter future for dental care.
Dental bur manufacturing has evolved significantly, transitioning from traditional methods to modern, tech-driven production. Understanding the diverse applications of different bur types and adhering to strict quality control measures ensures optimal performance and patient safety. As the industry focuses on sustainability, eco-friendly approaches are gaining traction. Looking ahead, advancements in materials, design, and automation will continue to shape the future of dental bur manufacturing, ultimately enhancing precision and efficiency in dental procedures.