Mastering Maintenance Budgets: Light Guards for Efficient Cost Management
Light guards, often overlooked, are crucial components in facility management's maintenance bud…….
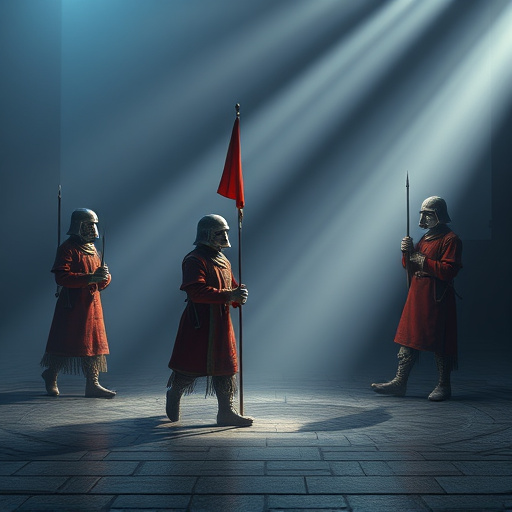
Light guards, often overlooked, are crucial components in facility management's maintenance budgeting strategy. They protect lighting fixtures, extend system lifespans, reduce costs, and enhance efficiency. By integrating light guard solutions into budgets, managers can optimize expense tracking, categorize maintenance tasks, and minimize unexpected downtime. Regular inspections, strategic planning, and proactive measures like light guard checks ensure optimal operational efficiency while balancing short-term needs with long-term sustainability. Effective budgeting includes regular reviews, updates, and cost-saving initiatives like energy-efficient lighting, preventing budget overruns.
In the realm of facility management, a well-crafted maintenance budget is a game-changer. This comprehensive guide delves into the essentials of budgeting for maintenance, equipping you with strategies to navigate this intricate process effectively. From understanding the core concepts to leveraging light guards—essential components in optimizing costs—we explore best practices. Learn how to identify maintenance needs, set realistic financial goals, and steer clear of common pitfalls. Embrace these insights to revolutionize your facility’s upkeep and budget management.
- Understanding Maintenance Budgets: A Comprehensive Guide
- The Role of Light Guards in Effective Budgeting
- Identifying Maintenance Needs: An Overview
- Setting Realistic Financial Goals
- Strategies for Efficient Cost Management
- Common Pitfalls to Avoid in Maintenance Budgeting
- Best Practices for Continuous Improvement
Understanding Maintenance Budgets: A Comprehensive Guide
Maintenance budgets are a critical aspect of facility management, ensuring that buildings and equipment remain in optimal condition. These budgets allocate financial resources for regular upkeep, repairs, and replacements, preventing costly emergencies. A well-planned maintenance budget considers various factors, including asset age, usage patterns, and environmental conditions, to predict and schedule necessary work.
One key element often overlooked but crucial for effective budgeting is the implementation of light guards. These protective devices safeguard lighting fixtures from damage caused by external elements like dust, debris, or vandalism. By incorporating light guard solutions into the maintenance plan, facilities can extend the lifespan of their lighting systems, reduce replacement costs, and maintain a safe, well-lit environment. This strategic approach to budgeting ensures that resources are allocated efficiently, enhancing the overall efficiency and sustainability of maintenance operations.
The Role of Light Guards in Effective Budgeting
In the realm of maintenance budgeting, light guards play a pivotal role in ensuring efficient allocation and optimization. These strategic tools facilitate meticulous tracking of expenses related to various equipment and facilities, thereby enhancing overall cost control. By segregating budgeted amounts for specific areas, light guards enable facility managers to closely monitor spending patterns and promptly identify discrepancies or areas for potential savings.
Moreover, light guards foster transparency and accountability within the budgeting process. They simplify the task of distributing financial resources across diverse maintenance categories, such as routine upkeep, emergency repairs, and capital improvements. This structured approach not only promotes responsible stewardship of funds but also aids in making informed decisions about long-term asset management and strategic planning for future projects.
Identifying Maintenance Needs: An Overview
Identifying Maintenance Needs begins with a thorough inspection of all facility components, from roofing and plumbing to electrical systems and light guards. This process involves assessing both visible wear and tear as well as potential hidden issues that could lead to future breakdowns or safety hazards. For example, regular checks on light guards—often overlooked but critical for preventing energy loss and enhancing security—can save significant costs in the long run by avoiding costly repairs or replacement.
Effective maintenance planning requires a proactive approach, where facilities managers anticipate needs based on historical data, industry standards, and expert insights. By scheduling routine inspections and implementing preventive measures, organizations can minimize unexpected downtime, reduce the impact of emergencies, and ensure optimal operational efficiency.
Setting Realistic Financial Goals
Setting realistic financial goals is a crucial step in creating an effective maintenance budget. It’s important to consider all aspects of your facility, including its size, age, and specific needs, such as light guard systems for energy efficiency. Start by evaluating past expenses and identifying areas where costs can be optimized without compromising quality or safety.
One effective strategy is to break down long-term goals into smaller, manageable milestones. For instance, if replacing old lighting with energy-efficient models is a priority, allocate a portion of your budget each quarter towards this goal. This approach ensures consistent progress and allows for flexibility in case unexpected maintenance issues arise. Remember, setting realistic financial goals means balancing short-term needs with long-term sustainability, ensuring your facility remains well-maintained without straining your resources.
Strategies for Efficient Cost Management
Efficient cost management in a maintenance budget is crucial for any organization aiming to optimize its expenses. A strategic approach can help reduce costs without compromising the quality of services. One effective strategy involves regular audits and assessments, where facilities managers identify areas of potential savings. For instance, implementing light guards on windows and doors not only improves energy efficiency but also reduces unnecessary lighting usage, contributing to significant cost cuts over time.
Additionally, prioritizing preventive maintenance can significantly impact long-term savings. By scheduling routine checks and repairs, organizations can avoid costly emergency fixes. This proactive approach ensures that equipment and facilities are well-maintained, increasing their lifespan and reducing the need for frequent replacements. It’s a smart way to manage budgets by focusing on efficient practices that save money in the long run.
Common Pitfalls to Avoid in Maintenance Budgeting
Many businesses fall into common pitfalls when creating their maintenance budgets, often overlooking essential aspects that can lead to costly surprises down the line. One major mistake is neglecting to account for unexpected repairs or replacement parts, such as light guards, which are crucial for protecting equipment and ensuring longevity. Regular maintenance plans should factor in these unforeseen expenses to avoid significant budget overruns.
Another pitfall involves underestimating the frequency of routine maintenance tasks. Light guards, for instance, may require more frequent cleaning or replacement than initially anticipated due to environmental factors or wear and tear. Budgets should be dynamic and flexible to accommodate these regular yet often overlooked costs, ensuring that maintenance efforts remain effective and efficient without stretching financial resources too thin.
Best Practices for Continuous Improvement
Regularly reviewing and updating your maintenance budget is crucial for continuous improvement. One effective practice is to implement light guard systems, which track equipment usage and identify maintenance needs before failures occur. By monitoring key performance indicators (KPIs) and analyzing trends, you can optimize scheduling and reduce unexpected downtime.
Additionally, fostering a culture of proactive maintenance among your team can significantly enhance efficiency. Training employees to recognize early signs of wear and tear, conducting regular inspections, and encouraging feedback loops ensure that potential issues are addressed promptly. These practices not only contribute to cost savings but also extend equipment lifespan, creating a more sustainable maintenance strategy.
In navigating the complexities of maintenance budgeting, understanding the interplay between light guards and efficient practices is key. By integrating these strategies – from identifying needs, setting realistic goals, and adopting best practices – organizations can minimize common pitfalls and optimize their financial resources. The role of light guards in this context proves invaluable, offering a systematic approach to budget management that fosters continuous improvement and ensures long-term sustainability.