Ring Terminals for Heavy-Duty Applications: Design, Installation, and Real-World Success
Ring terminals are vital connectors in construction, automotive, and maritime industries, ensuring s…….
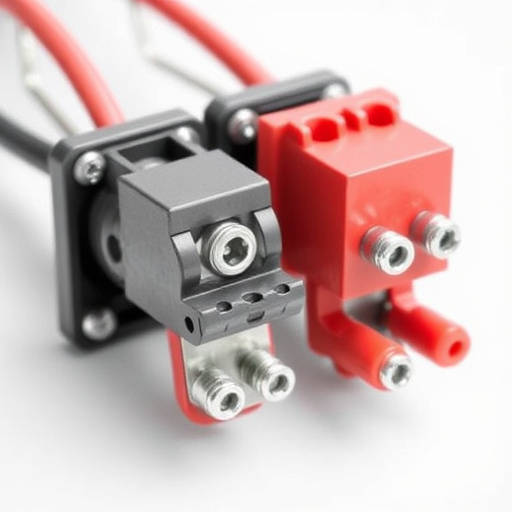
Ring terminals are vital connectors in construction, automotive, and maritime industries, ensuring secure electrical connections for machinery and vehicles. They offer fast installation, superior conductivity, and robust durability against corrosion and wear. Versatile designs cater to diverse needs, from high-current loads to waterproof applications. Choosing the right terminals involves understanding wire gauge requirements and terminal types. Regular cleaning, inspection, and proper crimping techniques extend their lifespan. In corrosive environments, using durable materials like stainless steel is recommended. A structured maintenance program ensures optimal performance in demanding conditions.
“Ring terminals are essential components for heavy-duty applications, offering reliable electrical connections in demanding environments. This comprehensive guide explores the multifaceted world of ring terminals, their role in enhancing industrial efficiency, and the diverse benefits they bring. From understanding terminal types tailored to specific industries to installation best practices and real-world success stories, this article delves into crucial design considerations, ensuring optimal performance. Discover how the right ring terminal selection can revolutionize your heavy-duty operations.”
- Understanding Ring Terminals: Their Role and Benefits in Heavy-Duty Applications
- Types of Ring Terminals for Diverse Heavy-Duty Industries
- Design Considerations: Strength, Durability, and Corrosion Resistance
- Installation and Safety Guidelines for Optimal Performance
- Real-World Applications: Success Stories from Various Sectors
- Choosing the Right Size and Type for Specific Electrical Needs
- Maintenance and Longevity: Tips to Maximize Lifespan in Demanding Environments
Understanding Ring Terminals: Their Role and Benefits in Heavy-Duty Applications
Ring terminals are essential components in heavy-duty applications, offering a reliable and efficient way to connect wires and cables. These terminals are designed to withstand extreme conditions, making them indispensable in industries like construction, automotive manufacturing, and maritime transportation. Their primary role is to facilitate secure electrical connections, ensuring the smooth operation of machinery and vehicles.
The benefits of ring terminals in heavy-duty settings are numerous. They provide a fast and simple installation process, reducing downtime and labor costs. Moreover, these terminals offer superior conductivity, minimizing resistance and maximizing energy transmission. Their durable construction also ensures longevity, even in harsh environments, where corrosion and wear are common challenges.
Types of Ring Terminals for Diverse Heavy-Duty Industries
In the diverse landscape of heavy-duty industries, ring terminals play a pivotal role in ensuring reliable electrical connections. These versatile connectors come in various types tailored to meet the unique demands of different sectors. For instance, within the construction industry, robust ring terminals designed to withstand extreme conditions and frequent vibrations are essential for securing power supplies to heavy machinery. Conversely, in marine applications, waterproof and corrosion-resistant ring terminals are crucial for maintaining the reliability of electrical systems in salty, humid environments.
Industrial settings, such as manufacturing plants and power generation facilities, require ring terminals that can handle high current loads and harsh chemical exposures. Specially engineered terminals with enhanced durability and safety features ensure these applications remain operational under adverse conditions. This diversity in ring terminal types underscores their significance, making them indispensable for the seamless operation of heavy-duty industries worldwide.
Design Considerations: Strength, Durability, and Corrosion Resistance
When designing heavy-duty applications that rely on ring terminals, strength is paramount. These connectors are often subjected to extreme tensile forces, vibration, and varying environmental conditions. Therefore, manufacturers must use high-grade materials like copper or aluminum alloy, treated with robust coatings or plating to enhance their resistance. The design should prioritize a strong, sturdy build capable of withstanding the demands of heavy machinery, industrial vehicles, and harsh weather without compromising integrity.
Durability is another critical aspect. Ring terminals in such applications need to endure repeated connections and disconnections, often in challenging settings where oils, greases, or other contaminants may be present. The design should incorporate features that prevent corrosion and wear, ensuring longevity and reliable performance over extended periods. Additionally, a focus on seamless manufacturing processes ensures that each terminal is free from flaws or imperfections that could lead to failure points under stress.
Installation and Safety Guidelines for Optimal Performance
When installing ring terminals for heavy-duty applications, it’s crucial to adhere to safety guidelines for optimal performance. Begin by preparing the surface, ensuring it is clean and free from debris or oil. Use appropriate tools designed for this purpose to avoid damage during installation. Tighten the terminals securely according to manufacturer recommendations, applying the correct torque to prevent loose connections that could lead to short circuits or equipment failure.
Safety should be a top priority throughout the process. Wear protective gear such as gloves and safety glasses to shield against any potential hazards. Additionally, ensure proper ventilation in the work area, especially when dealing with electrical components. Regularly inspect installed ring terminals for signs of damage or wear, replacing them as needed to maintain reliable performance and adherence to safety standards.
Real-World Applications: Success Stories from Various Sectors
In the realm of heavy-duty applications, where reliability and durability are paramount, ring terminals have proven to be indispensable. These versatile connectors are not just a buzzword in the industry; they are the unsung heroes behind many successful projects across diverse sectors. From robust machinery in manufacturing plants to complex automotive systems, ring terminals ensure secure electrical connections that withstand harsh conditions.
One notable success story involves a leading automotive manufacturer who adopted ring terminals for their high-performance vehicles. By replacing traditional connectors with these innovative terminals, the company achieved significant improvements in power distribution efficiency and reduced electrical resistance. This enhancement not only improved vehicle performance but also extended the lifespan of critical components, showcasing the tangible benefits of incorporating ring terminals in real-world applications.
Choosing the Right Size and Type for Specific Electrical Needs
When selecting ring terminals for heavy-duty applications, understanding your specific electrical needs is paramount. Different sizes and types of ring terminals cater to various wire gauge ranges and current capacities. For instance, larger gauge wires require terminals with sufficient space and strength to accommodate their diameter, ensuring a secure connection. Conversely, smaller gauge wires demand precision to avoid over-tightening and potential damage.
Choosing the appropriate type is equally crucial. Some ring terminals feature multiple tines or fingers, ideal for high-current applications as they provide enhanced conductivity and mechanical strength. Others may incorporate specific features like crimping mechanisms or strain relief areas, tailored to different manufacturing processes and environmental conditions. Matching these attributes with your electrical requirements ensures optimal performance and longevity of the terminal in heavy-duty settings.
Maintenance and Longevity: Tips to Maximize Lifespan in Demanding Environments
In heavy-duty applications, maintaining and extending the lifespan of ring terminals is paramount. Regular cleaning and inspection are crucial to prevent corrosion and ensure reliable electrical connections. Corrosive environments demand the use of high-quality, durable ring terminals treated with protective coatings or made from corrosion-resistant materials like stainless steel. Additionally, proper crimping techniques significantly enhance longevity by ensuring a secure fit within the wire.
To further maximize lifespan, consider implementing a structured maintenance program. This includes periodic replacement of worn-out or damaged terminals and keeping an inventory of spare parts. Ideal storage conditions—dry, cool, and organized—also play a vital role in preserving ring terminals’ integrity. By adhering to these tips, users can expect their heavy-duty ring terminals to withstand demanding environments for extended periods, ensuring optimal performance and reliability.