Optimizing Ring Terminal Selection: A Sizing and Application Guide
Ring terminals are essential components for securely and safely connecting wires to various electri…….
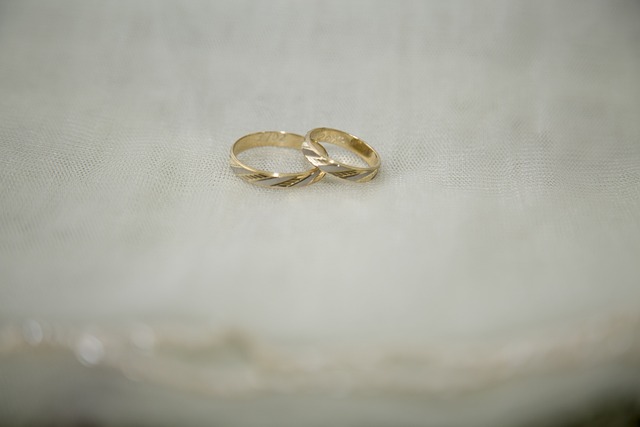
Ring terminals are essential components for securely and safely connecting wires to various electrical systems, ensuring both functional integrity under diverse conditions and protection against environmental threats. The appropriate size of a ring terminal is critical, as it must match the wire's American Wire Gauge (AWG) or circular millimeter (cmil) rating to handle the correct current without overheating or connection failure. Proper sizing also affects contact pressure between the wire and the terminal, which is vital for maintaining efficient electrical connections. It's important to select materials that can endure the mechanical stresses of temperature extremes, vibration, and exposure to corrosive elements for long-term reliability. In selecting a ring terminal, consider the wire gauge compatibility and ensure the internal diameter accommodates the wire's outer diameter for a secure and arcing-free connection. For residential wiring, a 14 gauge ring terminal may be sufficient, while industrial applications might require larger 2/0 gauge ring terminals to manage higher amperage safely. Ring terminals are indispensable in automotive electronics, heavy-duty power supplies, and even harsh environments like marine settings due to their durability and corrosion resistance. Ensuring the right application of ring terminals is essential for adhering to safety standards and maintaining system integrity across various sectors. Regular inspection and proper installation are key to preventing issues such as overheating or damage, which can lead to electrical hazards. Using ring terminals correctly not only upholds industry safety standards but also protects equipment and personnel from potential risks, highlighting their importance in the field of electrical connections.
When working with electrical systems, selecting the appropriate ring terminal is paramount for both functionality and safety. This article serves as a comprehensive guide to understanding ring terminal sizes and their diverse applications. From the impact of conductor size on selection to a detailed step-by-step process for accurate measurement and choice, we delve into the essentials of ring terminal sizing. Additionally, we provide a comparative analysis of common sizes with practical use cases, ensuring you have the knowledge to select the best fit for your needs. Finally, we offer valuable tips to adhere to installation and safety standards when working with these crucial components of electrical connections. Mastering ring terminal sizing is not just about making connections; it’s about guaranteeing reliable and safe power distribution in any application.
- Understanding Ring Terminal Sizes and Their Applications
- Key Factors Influencing Ring Terminal Selection Based on Conductor Size
- Step-by-Step Guide to Measuring and Selecting the Correct Ring Terminal
- Comparative Analysis of Common Ring Terminal Sizes and Use Cases
- Tips for Ensuring Proper Installation and Safety Standards with Ring Terminals
Understanding Ring Terminal Sizes and Their Applications
When selecting ring terminals for electrical connections, it’s crucial to understand the various sizes and applications they cater to. Ring terminals are essential components that connect the ends of wires or cables to electrical terminals or conductors. They ensure a secure and weatherproof connection, critical for both safety and reliability in various environments. The size of a ring terminal is determined by its diameter, which dictates the gauge of wire it can safely accommodate. Typically, these come in standardized sizes ranging from fine gauge for small-scale applications to robust dimensions suitable for heavy-duty use. For instance, a larger ring terminal with a higher diameter might be necessary for applications involving higher currents or where there’s a risk of mechanical stress. Conversely, smaller ring terminals are ideal for low-current circuits or space-constrained installations. Understanding the wire gauge compatibility and the environmental conditions the terminal will face is essential to select the appropriate size. Properly sized ring terminals not only enhance performance but also comply with safety standards and regulations, ensuring that electrical connections remain reliable over time. Whether for industrial machinery, automotive electronics, or residential wiring, the right ring terminal size optimizes both functionality and protection against environmental factors such as moisture, corrosion, and physical wear.
Key Factors Influencing Ring Terminal Selection Based on Conductor Size
When selecting ring terminals, the size of the conductor is a critical factor that influences both the appropriate terminal and its performance within an electrical circuit. The American Wire Gauge (AWG) or the circular millimeter (cmil) rating of the conductor determines its cross-sectional area and current-carrying capacity. For conductors with larger AWG or cmil ratings, ring terminals must be proportionally sized to accommodate the increased current flow without overheating or causing connection failure. This is due to Ohm’s Law, which dictates that voltage, current, and resistance are interrelated; thus, a higher current requires a lower resistance path for safe and efficient power transfer.
Moreover, the diameter of the conductor affects the contact pressure between the ring terminal and the wire, which in turn impacts the quality of the electrical connection. Insufficient contact pressure can lead to poor conductivity and potential electrical risks, while excessive pressure might damage the insulation or the conductor itself. It is imperative to select a ring terminal that provides optimal contact without causing harm to the wire. Additionally, the mechanical environment where the ring terminal will be used must be considered. Factors such as temperature extremes, vibration, and exposure to corrosive substances can affect both the conductor and the terminal’s performance over time. Therefore, it is crucial to choose materials for both the conductor and the ring terminal that are compatible with these conditions to ensure long-term reliability and safety in the application. Proper sizing of ring terminals based on conductor size is essential for maintaining efficient and safe electrical connections across various industries, from residential electrical systems to heavy machinery and beyond.
Step-by-Step Guide to Measuring and Selecting the Correct Ring Terminal
When selecting the appropriate ring terminal for your electrical project, it’s crucial to consider several factors to ensure a secure and reliable connection. To begin with, assess the gauge of the wire you will be using. Ring terminals come in various sizes, typically ranging from 14 to 4/0 gauge, and the correct size is determined by the wire diameter that corresponds to it. Measure your wire’s diameter with a wire gauge tool to select the compatible ring terminal. For instance, if your wire is 12 gauge, you should pair it with a ring terminal designed for 12 gauge wires.
Once you have determined the correct gauge, the next step involves selecting the appropriate ring terminal size based on the conductor size and insulation type. Ensure that the terminal’s inside diameter matches the wire’s outer diameter to prevent any risk of electrical arcing or connection failure. Additionally, consider the installation environment; for example, if the terminal will be subjected to high temperatures, opt for a material with a suitable temperature rating. If you’re working with heavy-gauge wires, look for ring terminals with larger contact areas to distribute stress evenly and prevent deformation under load. Always refer to the manufacturer’s specifications for compatibility and performance data to select the most appropriate ring terminal for your specific application.
Comparative Analysis of Common Ring Terminal Sizes and Use Cases
When selecting ring terminals, understanding the comparative sizing and application-specific requirements is crucial for ensuring electrical connections are both safe and reliable. Ring terminals come in various sizes, from small types designed for low-amperage applications to robust options suitable for high-current demands. For instance, a 14 gauge ring terminal might be used for household wiring where the currents are relatively low, while a larger 2/0 gauge is more appropriate for industrial machinery or heavy-duty power supplies. The size of the ring terminal is determined by its American Wire Gauge (AWG) rating, which dictates the wire diameter it can safely enclose and the maximum current it can handle. This sizing guide is essential for electricians and engineers to select the correct terminal for the intended application, as using a terminal with an incorrect gauge can lead to overheating, connection failure, or even electrical fires.
In practical use cases, ring terminals are employed across a wide range of industries and applications. In automotive electronics, for example, ring terminals secure battery cables and high-current connections like starter motors and alternators. In residential construction, they provide weatherproof exits for wiring from service panels to devices. Industrial settings often utilize larger ring terminals for motors, pumps, and heavy machinery, where they must endure demanding conditions and deliver consistent performance over time. Additionally, in marine environments, stainless-steel ring terminals are preferred due to their corrosion resistance, ensuring the longevity of electrical connections on boats and other watercraft. Properly sizing and applying ring terminals according to these use cases is paramount for maintaining safety standards and system integrity across all sectors where they are used.
Tips for Ensuring Proper Installation and Safety Standards with Ring Terminals
When working with electrical systems, ensuring the proper installation and adherence to safety standards is paramount. Ring terminals play a critical role in this process as they provide secure connections between wires and various components such as terminals, switches, and circuit breakers. To guarantee the longevity and reliability of these connections, it is essential to select the correct ring terminal size for the wire gauge you are using. The terminal should be able to accommodate the wire without causing any deformation or over-tightening, which could lead to poor conductivity or damage to the insulation.
Proper installation involves careful measurement and sizing. The ring terminal should fit snugly around the wire; not too tight as to compromise the integrity of the wire’s insulation, nor too loose that it becomes a hazardous disconnection risk. Use pliers designed for this purpose to twist the ring terminal onto the wire, ensuring an even and secure connection. It is also important to follow the manufacturer’s guidelines for the specific type of wire and gauge you are working with. Additionally, inspect the connection for any signs of overheating or damage after installation, and periodically thereafter, especially in environments subject to high temperatures or vibrations. Adhering to these tips not only ensures a safe electrical system but also contributes to the longevity and performance of the ring terminals themselves. Safety should always be at the forefront when handling electrical installations, making the correct use of ring terminals a key aspect in upholding industry standards and protecting both equipment and personnel from potential harm.