Mastering Jewelry Casting with Lost-Wax Techniques and Essential Tools
The lost-wax casting method is a venerable technique in jewelry making, renowned for its ability to …….
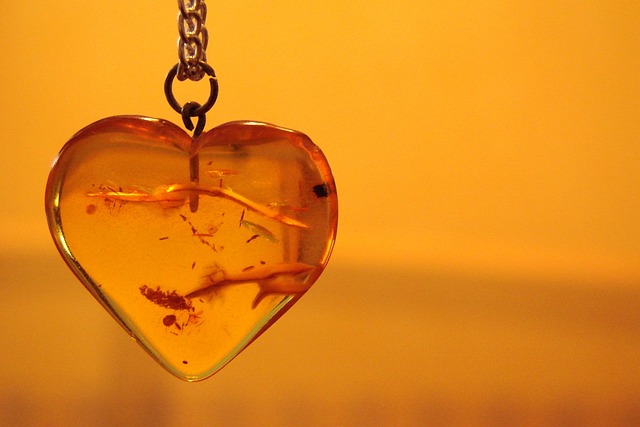
The lost-wax casting method is a venerable technique in jewelry making, renowned for its ability to produce intricate and detailed pieces. With origins from ancient Mesopotamia around 3700 BCE, this process has consistently been a cornerstone in the creation of exquisite jewelry. The technique involves crafting a wax model that represents the desired piece, then creating a mold around it, which is later filled with molten metal to form an accurate casting. Mastery of lost-wax casting requires familiarity with specialized tools and materials, including various types of flasks, investment material, casting equipment, safety gear, and post-casting tools for cleaning, filing, and refining the jewelry. The choice of investment material is critical, as it must withstand extreme temperatures to ensure the integrity and quality of the final piece. This ancient craft amalgamates artistic creativity with precise technical skills, making it a benchmark in the fine jewelry industry. In the realm of business, selecting the right lost-wax casting system is crucial for jewelry brands aiming to stand out in the competitive market by delivering high-quality products with complex designs. Factors such as precision, reliability, and efficiency are key when choosing among top brands like Compact II or PrecisionII, ensuring consistency, durability, and overall product quality. Investing in a high-performance lost-wax casting system is essential for elevating the artistry and efficiency of jewelry production, enhancing the reputation and success of businesses within the fine jewelry sector.
Explore the intricate art of jewelry casting with our comprehensive guide on lost-wax casting, a process that transforms intricate wax designs into exquisite metal pieces. This article demystifies the techniques and tools involved in this craft, from the essential equipment needed to create detailed wax models to the investment materials that complete the mold. We’ll walk you through each step of the process, offering insights into the lost-wax casting methodology that professionals use to bring their designs to life. Additionally, we provide a comparative analysis of leading lost-wax casting systems in the market, helping you select the ideal setup for your jewelry business. Whether you’re a novice or an experienced artisan, this guide will enhance your understanding and mastery of jewelry casting techniques.
- Mastering Jewelry Casting: An Overview of Lost-Wax Techniques and Essential Tools
- The Anatomy of Lost-Wax Casting Equipment: From Wax Models to Investment Materials
- Step-by-Step Guide to the Lost-Wax Casting Process in Jewelry Making
- Selecting the Best Lost-Wax Casting System for Your Jewelry Business: A Comparative Analysis of Top Brands and Tools
Mastering Jewelry Casting: An Overview of Lost-Wax Techniques and Essential Tools
In the realm of jewelry making, mastering the lost-wax casting technique is a pivotal skill for artisans and designers alike. This intricate process, which dates back to 3700 BCE in Mesopotamia, remains integral to the creation of fine jewelry pieces today. The lost-wax casting method involves creating a mold from a wax model that accurately represents the intended final piece. Once the mold is complete and the wax is removed, molten metal is poured into the cavity, resulting in a precision casting that requires minimal post-processing. This technique allows for intricate details to be preserved, making it suitable for complex designs.
To embark on this craft with confidence, one must acquaint themselves with essential tools and materials. A comprehensive set of equipment includes a wax modeling kit, flasks of varying sizes, investment material for creating the mold, a crucible for melting metal, a centrifugal casting machine or a hand-pouring setup, safety gear such as gloves and goggles, and a ventilated workspace. Additionally, tools for cleaning, filing, and refining the cast pieces are crucial for achieving the desired finish. Understanding the specifics of each tool and its role in the process is key to producing high-quality jewelry through lost-wax casting. With practice and precision, this age-old technique remains a benchmark for excellence in the fine jewelry industry.
The Anatomy of Lost-Wax Casting Equipment: From Wax Models to Investment Materials
In the realm of jewelry casting, the lost-wax casting process is a meticulous technique that has been refined over centuries to produce intricate and precise pieces. This method begins with the creation of a wax model, which accurately represents the desired final piece of jewelry. The artisan sculptor uses specialized tools to carve or mold the wax into the desired shape and design, ensuring every detail is perfectly captured. Once the wax model is complete, it undergoes a series of preparatory steps. It is coated with a refractory material, which, upon heating, will form the investment mold. This material is crucial as it must be able to withstand high temperatures without deforming and provide a durable matrix that encapsulates the wax model completely. The type of investment material used can affect the quality and integrity of the final casting, as different materials have varying properties and melting points. Once the investment material hardens, typically through a curing process, the resulting mold is prepared for the next stage of jewelry casting. The mold is then heated to a high temperature in a specialized furnace, causing the wax to vaporize and leave a void that will be filled by the molten metal—usually precious metals like gold or silver—which takes the place of the wax, resulting in a detailed replica of the original model. This process, from the intricate crafting of the wax model to the precise application of investment material and the final casting, requires a delicate balance of artistry and technical precision, making it a cornerstone of the jewelry-making industry and an essential skill for artisans and jewelers alike.
Step-by-Step Guide to the Lost-Wax Casting Process in Jewelry Making
The lost-wax casting process, a technique pivotal in jewelry crafting, involves several precise steps crucial for the production of intricate and detailed pieces. To initiate the process, artisans begin by designing a model that captures the desired final appearance of the jewelry item. This model serves as the original, from which a mold will be created. The model is then coated with a refractory material, such as investment, to form a durable shell that will retain the details of the original design when heated.
Once the investment has set and fully covers the model, it is placed in a flask and positioned within a casting chamber. The flask is filled with molten metal, typically silver, gold, or another alloy suitable for jewelry, and then the chamber is sealed. Controlled heating allows the investment to vaporize, leaving behind a cavity shaped precisely like the original model. The molten metal cools and solidifies in this cavity, resulting in a casting that closely resembles the intended piece of jewelry. After cooling, the casting is carefully removed from the flask, and any excess material or investment remnants are finished by hand to achieve the final product, ready for polishing and finishing touches. This method, known as ‘investment casting’ in the broader manufacturing field, is a testament to the precision and artistry involved in jewelry casting, enabling crafters to produce high-quality, consistent pieces with complex designs.
Selecting the Best Lost-Wax Casting System for Your Jewelry Business: A Comparative Analysis of Top Brands and Tools
In the realm of fine jewelry creation, lost-wax casting stands out as a pivotal technique for artisans and businesses alike. Selecting the best system within this process is crucial for achieving high-quality results that can set a brand apart in a competitive market. When evaluating systems for jewelry casting, it’s important to consider factors such as precision, reliability, and efficiency. The top brands in lost-wax casting offer a range of tools and technologies, each with its own strengths. For instance, some systems may excel in their ability to produce intricate details, while others might be preferred for their speed or user-friendliness. It’s essential to analyze the specific needs of your jewelry business, including the scale of production, the complexity of designs, and the budget constraints. By comparing leading brands like Compact II or PrecisionII, one can discern which system aligns with the unique requirements of your creations. Consider aspects such as the consistency of casting, the durability of molds, and the quality of the final product. Ultimately, investing in a lost-wax casting system that offers superior performance and reliability will contribute significantly to the success and reputation of your jewelry business. Make an informed decision by weighing the pros and cons of each option, ensuring that your choice enhances the artistry and efficiency of your jewelry casting endeavors.