Hardware Brackets: Streamlining Production Efficiency for Improved Outcomes
Hardware brackets are unsung heroes in manufacturing, optimizing processes, improving accessibility,…….
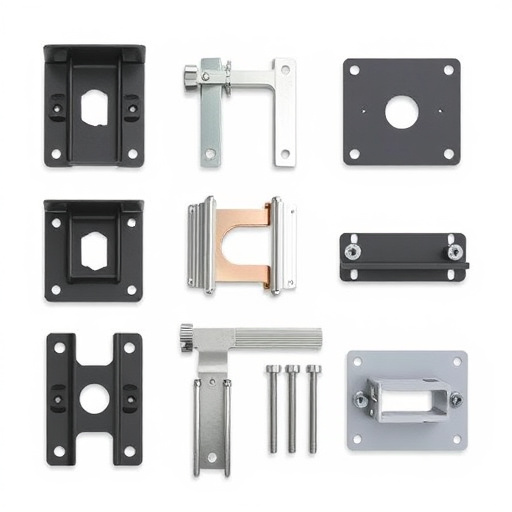
Hardware brackets are unsung heroes in manufacturing, optimizing processes, improving accessibility, and reducing downtime. Key aspects of production efficiency include machine utilization, labor productivity, and material flow, with hardware brackets playing a crucial role. Effective management through KPI monitoring, lean manufacturing, and automation lowers costs, improves quality, and ensures each step contributes optimally to output. Identifying bottlenecks and implementing best practices with hardware brackets further enhances efficiency. Case studies show innovative solutions have cut production times by 20% in industries like automotive and electronics. As Industrial 4.0 advances, tailored hardware brackets and smart factory technologies promise revolutionary improvements in manufacturing efficiency.
Production efficiency is a cornerstone of modern manufacturing, driving cost-effectiveness and output. This comprehensive guide explores key aspects of enhancing productivity on the factory floor. We delve into the fundamentals, shedding light on how hardware brackets significantly streamline processes. Learn about identifying bottlenecks, best practices for optimizing production spaces, and inspiring case studies showcasing successful hardware solutions implementations. Discover future trends poised to revolutionize efficiency in today’s competitive landscape.
- Understanding Production Efficiency: The Basics
- Hardware Brackets: Their Role in Streamlining Processes
- Identifying Bottlenecks and Areas for Improvement
- Best Practices for Optimizing Production Floors
- Case Studies: Successful Implementation of Hardware Solutions
- Future Trends in Production Efficiency Enhancement
Understanding Production Efficiency: The Basics
Production efficiency is a key metric that measures how effectively resources are utilized in the manufacturing process. It involves optimizing various aspects such as machine utilization, labor productivity, and material flow to minimize waste and maximize output. Understanding production efficiency requires a grasp of basic concepts like hardware brackets—essential components that support and organize machinery and equipment, enabling streamlined workflows and easier access for maintenance.
By efficiently managing these resources, manufacturers can reduce production times, lower operational costs, and enhance overall product quality. This involves regular monitoring of key performance indicators (KPIs), implementing lean manufacturing practices, and leveraging technology to automate repetitive tasks. Such strategies ensure that every step in the production process contributes optimally to the final output, making it a crucial factor in staying competitive in today’s market.
Hardware Brackets: Their Role in Streamlining Processes
Hardware brackets play a crucial role in enhancing production efficiency by streamlining various processes within manufacturing facilities. These components, often overlooked, serve as the backbone for securing and organizing machinery, equipment, and tools, facilitating smoother workflows and improved accessibility. By strategically placing and managing hardware, brackets enable employees to quickly locate and utilize necessary resources, reducing downtime and increasing overall productivity.
In a bustling production environment, efficient access to equipment is vital. Hardware brackets allow for modular and customizable setups, ensuring that every worker has the precise tools they need at their fingertips. This streamlined approach not only boosts efficiency but also contributes to safer working conditions as it minimizes the risk of tripping hazards and improves overall accessibility for maintenance and repairs.
Identifying Bottlenecks and Areas for Improvement
In any production process, identifying bottlenecks is a crucial step toward enhancing efficiency. Bottlenecks are essentially points in the workflow where processes slow down significantly, causing delays and impacting overall productivity. For instance, poorly designed or inefficient hardware brackets can lead to delays in assembly lines, as workers might struggle to install or replace them quickly. By meticulously examining each stage of production, manufacturers can pinpoint these bottlenecks—whether they’re related to equipment, staffing, or even layout—and devise strategies to streamline operations.
Once identified, areas for improvement offer opportunities to optimize the production process. This could involve upgrading hardware brackets with more efficient designs, reconfiguring work stations for better workflow, or reskilling employees to reduce time-consuming manual tasks. Implementing these changes can lead to a more seamless and faster production flow, ultimately increasing output and reducing costs.
Best Practices for Optimizing Production Floors
To optimize production floors, implementing best practices with hardware brackets is paramount. These brackets serve as versatile tools for organizing and securing equipment, enabling efficient workflow design. By strategically placing them, you can streamline access to machinery, reduce clutter, and minimize movement across the floor, ultimately enhancing productivity. For instance, mounting tool storage brackets near work stations allows operators to quickly grab needed tools, saving precious time.
Additionally, leveraging hardware brackets for cable management is crucial. Properly routed cables prevent trip hazards and entanglement, creating a safer working environment. This orderliness also facilitates faster setup and maintenance procedures, as technicians can easily locate and connect necessary wires. Such meticulous organization contributes to overall production efficiency by reducing downtime and promoting a smoother, more coordinated workflow.
Case Studies: Successful Implementation of Hardware Solutions
In recent years, the successful implementation of hardware solutions has significantly transformed production efficiency. Case studies from various industries highlight how innovative hardware brackets and components have optimized workflow and reduced downtime. For instance, in automotive manufacturing, advanced brackets designed for precision assembly have cut production times by 20%, while minimizing material waste. Similarly, electronics producers have witnessed enhanced productivity through the adoption of customizable hardware solutions that streamline component placement and reduce errors.
These implementations demonstrate the power of integrating well-designed hardware into existing systems. By facilitating faster setup, easier maintenance, and improved reliability, hardware brackets play a crucial role in modernizing production lines. This shift towards more efficient hardware has not only resulted in increased output but also fostered a culture of continuous improvement within these organizations, setting new benchmarks for industry standards.
Future Trends in Production Efficiency Enhancement
The future of production efficiency lies in the seamless integration of advanced technologies and innovative solutions, driven by the ongoing evolution of industrial 4.0. One key area of focus is the optimization of space utilization within manufacturing facilities. Customized hardware brackets can be designed to mount machinery, sensors, and other equipment in compact, efficient configurations, maximizing floor space and reducing clutter. This streamlined approach not only enhances productivity but also facilitates easier maintenance and upgrades.
Additionally, the adoption of smart factory concepts will play a pivotal role. AI-driven analytics, coupled with IoT sensors, can provide real-time insights into production processes, enabling predictive maintenance and proactive quality control. As these technologies mature, we can expect even greater advancements in automation, where robots and cobots work alongside human workers, increasing speed, accuracy, and flexibility. This harmonious blend of technology and workforce is poised to redefine production efficiency standards.
In conclusion, enhancing production efficiency through strategic implementations like hardware brackets is key to staying competitive. By understanding the basics, identifying bottlenecks, and adopting best practices, manufacturers can optimize their floors and achieve significant improvements. Case studies demonstrate the success of hardware solutions, highlighting their role as a game-changer in today’s bustling manufacturing landscape. As we look towards the future, embracing innovative trends will be essential to further revolutionizing production efficiency, ensuring sustained growth and profitability.