Mastering Rigid Heddle Loom Weaving: A Comprehensive Guide from Setup to Finished Project
The rigid heddle loom is an accessible yet versatile tool for weavers of all skill levels, offering…….
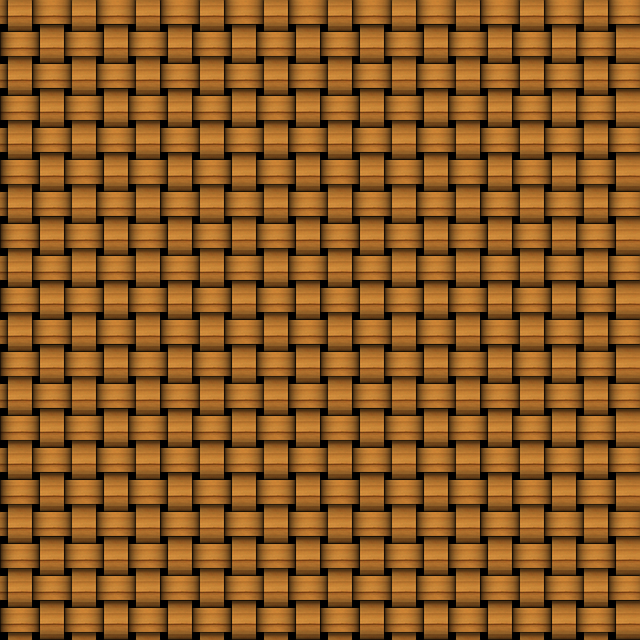
The rigid heddle loom is an accessible yet versatile tool for weavers of all skill levels, offering a reliable platform for creating a wide array of textiles through various techniques like plain weave, twill, and satin. Its straightforward design ensures ease of use, making it perfect for both beginners and experienced crafters looking to explore weaving without complex machinery. Understanding the mechanics of the heddle system is key for creating consistent tension and sheds in the fabric. As weavers develop their skills, the rigid heddle loom provides a solid foundation for producing high-quality hand-woven textiles with precise patterns, suitable for both personal use and commercial purposes.
The initial setup involves warping the loom with yarn, threading the heddle according to a draft pattern, securing warp threads to the apron rods, and attaching the heddle to the cloth or breast beam. Winding yarn onto the cloth beam, adjusting tension, and shedding layers of warp to accommodate the weft are all critical steps in the process. Maintenance of the loom and experimentation with different yarns can enhance both the technical aspects and artistic qualities of the fabric.
After weaving, finishing techniques such as washing, hemming, and applying final treatments are essential for transforming the raw fabric into a refined, durable, and aesthetically pleasing end product. These processes not only improve the fabric's handfeel but also ensure that the woven piece maintains its form and fit over time. Overall, mastery of the rigid heddle loom and these finishing techniques allows weavers to create a diverse range of textiles with both functionality and artistic flair.
Embark on a textile journey with “Weaving on a Rigid Heddle Loom,” an article designed to guide both novice and seasoned weavers through the intricacies of this versatile tool. Delve into the fundamental aspects of rigid heddle looms, essential for achieving precision and excellence in your handcrafted fabrics. This comprehensive guide offers a detailed walkthrough on setting up your loom, ensuring you’re well-prepared to explore the techniques of warping, threading, and shedding that will elevate your weaving skills. As you navigate through various patterns, discover how rigid heddle looms can be your canvas for creating rich textures and unique designs. Finally, perfect your craft by learning the finishing touches that transform raw fabric into a polished and complete project. Master the art of weaving with this insightful exploration of the rigid heddle loom’s capabilities.
- Understanding the Rigid Heddle Loom: A Foundation for Weaving Excellence
- Setting Up Your Rigid Heddle Loom: Step-by-Step Guide to Preparation
- Mastering the Craft: Techniques for Warping, Threading, and Shedding on a Rigid Heddle Loom
- Exploring Weaving Patterns: Creating Textural and Design Variety with Rigid Heddle Techniques
- Finishing Touches: From Weaving to Project Completion – Washing, Hemming, and Finalizing Your Creation
Understanding the Rigid Heddle Loom: A Foundation for Weaving Excellence
Engaging with a rigid heddle loom offers weavers a structured and reliable platform for crafting a wide array of textiles. This type of loom, distinguished by its fixed hammers that separate warp threads at regular intervals, is an excellent starting point for both beginners and experienced weavers alike. It allows for the creation of intricate patterns and structures, such as plain weave, twill, and satin, which can be foundational or complex depending on the desired outcome. The rigid heddle loom’s simplicity in design translates to ease of use, making it a versatile tool for exploring various weaving techniques and styles without the need for sophisticated equipment. Understanding its mechanics, such as the role of the heddle in lifting alternate threads to form shed spaces, is crucial for mastering the craft of weaving on this loom. As one gains proficiency, the rigid heddle loom becomes a foundation for weaving excellence, enabling the creation of textiles with consistent tension and precise patterns, which are hallmarks of high-quality hand-woven fabrics. Whether one is interested in producing samples for larger projects or crafting finished pieces for personal use or sale, the rigid heddle loom provides a solid foundation for weaving ventures that are both rewarding and expansive.
Setting Up Your Rigid Heddle Loom: Step-by-Step Guide to Preparation
Begin by carefully positioning your rigid heddman on its respective rod, ensuring that it moves freely up and down without obstruction. This component is crucial for raising and lowering the warp threads during the weaving process, allowing for the creation of different structures such as plain weave, twill, or satin. Next, thread your warp yarns through the heddman, aligning them according to your pattern design. Secure the ends of the warp by tying them to the front and back apron rods, making sure they are evenly distributed across the loom’s width for a consistent weaving surface. Attach the rigid heddle to the cloth beam or direct the yarns to the breast beam, depending on your weaving project requirements.
Once your warp is securely in place, you can proceed to wind the yarn onto the cloth beam, which will hold the woven fabric as you work. Adjust the tension of both the warp and the heddman using the tension adjusters or apron rods to prevent any unevenness that could affect the final fabric. With your loom properly set up, you’re ready to begin the weaving process, starting with tying in the first few threads by hand before proceeding to use the shuttle or a needle to bring the weft yarns through the warp. This careful preparation is essential for achieving even and consistent results in your weaving projects on a rigid heddle loom.
Mastering the Craft: Techniques for Warping, Threading, and Shedding on a Rigid Heddle Loom
Engaging with the rigid heddle loom unlocks the artistry of handweaving, a practice steeped in tradition yet ever-relevant in contemporary craftsmanship. To initiate the process, warping is the foundational step where yarns are strung across the loom to create the length of cloth that will eventually be woven. The accuracy and tension of the warp threads directly influence the quality of the final piece, so careful attention must be given to ensure a uniform and stable base for weaving. Beginners should select a manageable project for their first warping experience, using ample space between each warp thread to allow for easy threading and manipulation later on.
Once the warp is in place, threading follows, where individual yarns from the yarn gallery are inserted through specific holes in the heddle to set up the draft pattern that will dictate the interlacing of warp and weft threads. This step requires patience and precision; misthreads can lead to unevenness or pattern disruptions. To streamline this process, it’s beneficial to organize yarns by color and size beforehand. Additionally, utilizing a threading chart corresponding to the chosen pattern can aid in maintaining the correct order of threads. After threading, shedding is the action that separates layers of warp threads to create space for the weft to pass through, alternating between the upper and lower sets of threads. This movement is facilitated by the rigid heddle’s mechanism, which must be mastered to achieve consistent and even sheds. Practicing this technique will enhance control over the tightness and alignment of each row of woven fabric, leading to a professional-looking and structurally sound woven piece. Regular maintenance of the loom ensures its smooth operation, while experimenting with various yarn types and thicknesses can expand weaving capabilities and creativity. The art of rigid heddle weaving is both accessible and complex, offering a rich experience for weavers at all skill levels.
Exploring Weaving Patterns: Creating Textural and Design Variety with Rigid Heddle Techniques
When venturing into the realm of rigid heedle loom weaving, crafters discover a wealth of possibilities for creating textural and design variety in their woven fabrics. The rigid heddle loom, a versatile tool, allows weavers to manipulate yarn with precision to produce an array of patterns and structures. By understanding the interplay between warp threads held taut by the heddle and the weft threads inserted through this structure, weavers can control the density, elevation, and intricacy of their designs. This technique enables the creation of both simple and complex patterns, from plain weaves to more elaborate twills, satins, and picks. Experimenting with different yarn types and thicknesses further expands the potential for textural diversity, making each woven piece unique. Mastering rigid heddle weaving patterns not only enhances the aesthetic appeal of the finished fabric but also serves as a foundation for incorporating color through warp-wise or weft-wise techniques, adding yet another dimension to the craft. As weavers become more adept at navigating the loom’s capabilities, they can confidently explore and execute patterns that showcase their creativity and skill in producing textural and design variations on a rigid heddle loom.
Finishing Touches: From Weaving to Project Completion – Washing, Hemming, and Finalizing Your Creation
Engaging in the meticulous craft of weaving on a rigid heddle loom culminates in the application of finishing touches that transform raw fabric into complete projects. Post-weaving, the fabric often requires washing to remove any remaining sizing, which can inhibit the yarn’s natural texture and softness. This process not only enhances the handle but also prepares the fibers for subsequent treatments. Washing is typically done by hand in warm water with a gentle detergent, followed by a thorough rinse and careful drying.
Upon drying, hemming becomes the next critical step to ensure your woven piece maintains its shape and durability. Hemming secures loose threads and edges, providing clean and polished lines that showcase the craftsmanship of the weaving process. This step also allows for any necessary adjustments to the tension or fit of the project. Finally, to complete your creation, consider applying a suitable finish or treatment depending on the yarn type and desired outcome. For natural fibers like cotton or wool, a fabric sealant can protect against pests and environmental factors. Synthetic fibers may benefit from a heat-setting process to prevent stretching or distortion over time. These finishing touches are essential in bringing out the full potential of your weaving on a rigid heddle loom, resulting in a project that is both functional and aesthetically pleasing.