Optimizing Electrical Performance: A Deep Dive into Ring Terminal Resistance
Ring terminals are essential components that ensure secure and reliable connections within electric…….
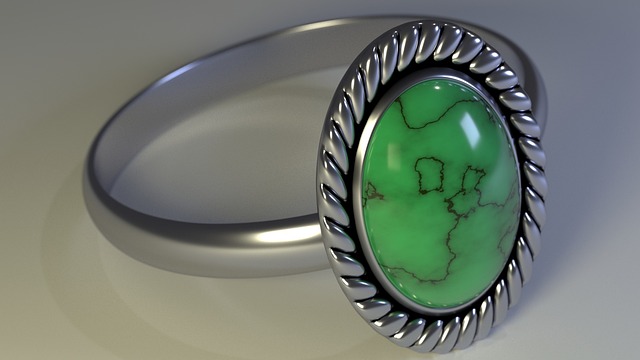
Ring terminals are essential components that ensure secure and reliable connections within electrical systems, significantly impacting their performance and safety. The choice of material for these terminals—such as copper alloys, brass, or stainless steel—is critical, as it affects resistance properties and the terminal's ability to maintain efficient power transmission in diverse environmental conditions. Factors like cross-sectional area, temperature extremes, current loads, and corrosion can alter electrical resistance, thus influencing the integrity of the electrical circuit. Proper selection and management of ring terminals, considering these factors, are essential to prevent issues like unexpected voltage drops or overheating. Advanced materials and design innovations have led to high-conductivity copper alloys that enhance durability, reduce resistance, and ensure long-term functionality in challenging environments. The evolution of ring terminals reflects a commitment to improving efficiency and performance across various sectors, including automotive, industrial, and renewable energy systems. Understanding and controlling electrical resistance in ring terminals is key to maintaining safe and effective electrical connections.
When electrical circuits are complete, the performance hinges on the integrity of their terminal connections. This article delves into the critical aspect of electrical resistance in ring terminals and its implications for circuit efficiency and reliability. We explore the impact of material composition on resistance levels and identify factors that contribute to this resistance. With a focus on practical application, we discuss methods for measuring and managing resistance within systems utilizing ring terminals. Furthermore, we outline best practices for selecting appropriate ring terminals based on resistance requirements. Advancements in ring terminal design are also examined, highlighting innovative solutions that minimize resistance and enhance overall system performance. Understanding these elements is paramount for engineers and technicians aiming to optimize electrical connections and ensure the longevity of their equipment.
- Understanding Electrical Resistance in Ring Terminals
- The Role of Material Composition in Ring Terminal Resistance
- Factors Influencing Resistance in Ring Terminals
- Measuring and Managing Resistance in Applications with Ring Terminals
- Best Practices for Selecting Ring Terminals Based on Resistance Requirements
- Advanced Technologies and Innovations in Ring Terminal Design to Minimize Resistance
Understanding Electrical Resistance in Ring Terminals
Ring terminals are critical components in electrical connections, serving as the interface between wires and various equipment or devices. The concept of electrical resistance within these terminals is pivotal to their performance and reliability. Electrical resistance refers to the opposition to the flow of electric current through a material. In ring terminals, this resistance can affect the amount of current that successfully transmits from one point to another. Several factors contribute to the resistance in ring terminals, including the material composition of the terminal, the cross-sectional area of the terminal’s conductor, and the environmental conditions under which the terminal operates.
The materials used in ring terminals, typically metals like copper or aluminum, have inherent electrical conductivities that influence their resistance properties. A larger cross-sectional area allows for less resistance due to the increased number of free electrons that can flow through the conductor. Additionally, environmental factors such as temperature and corrosion can significantly impact resistance. For instance, an increase in temperature generally decreases resistance, while corrosion can form an oxide layer on the metal surface, which can obstruct electron movement and thus increase resistance. To minimize these effects and ensure optimal performance, manufacturers often design ring terminals with considerations for material selection, dimensions, and protective coatings to mitigate environmental influences. Understanding and managing electrical resistance in ring terminals is essential for maintaining efficient and safe electrical connections across various applications, from industrial machinery to consumer electronics.
The Role of Material Composition in Ring Terminal Resistance
Electrical ring terminals play a pivotal role in establishing a secure and reliable connection between electrical conductors and devices. The resistance properties of these terminals are influenced significantly by the composition of their materials. Selection of material is critical as it dictates the terminal’s performance under various conditions, including temperature extremes and current loads. Common materials for ring terminals include copper alloys, brass, and stainless steel. Each material offers different resistance characteristics; for instance, copper alloys are renowned for their high conductivity and durability, which minimizes voltage drop and resists corrosion. Brass, a mix of copper and zinc, provides a balance between strength and conductivity, making it suitable for applications where both factors are important. Stainless steel, while less conductive than copper, is highly resistant to corrosion and ideal in harsh environments. The resistance value, which can range from milliohms to ohms, is a key determinant of the terminal’s efficiency and longevity, directly affecting the overall integrity of the electrical circuit it is part of. Manufacturers must carefully consider the material composition when designing ring terminals to ensure optimal performance and longevity, tailoring the choice to the specific application requirements for the best balance between conductivity, mechanical strength, and environmental durability.
Factors Influencing Resistance in Ring Terminals
The electrical resistance encountered in ring terminals is influenced by several critical factors that can affect their performance and reliability within an electrical circuit. Material composition plays a pivotal role; different metals, such as copper alloys, aluminum, or stainless steel, exhibit varying conductivity levels which directly impact the resistance values. The cross-sectional area of the terminal is another significant determinant; terminals with larger surface areas provide lower resistance paths for current flow compared to those with smaller sections.
Environmental conditions also significantly influence resistance in ring terminals. Exposure to high temperatures can cause some materials to expand, potentially increasing contact resistance at connection points. Conversely, low temperatures may lead to material contraction, affecting the pressure between mating surfaces and potentially raising resistance. Additionally, the presence of corrosion or oxidation on the terminal surfaces can form an insulating layer, substantially increasing electrical resistance and causing contact inconsistencies that degrade performance. It is essential to consider these factors when selecting and installing ring terminals to ensure optimal electrical connections and to prevent unexpected voltage drops or overheating issues in the circuit.
Measuring and Managing Resistance in Applications with Ring Terminals
In applications involving ring terminals, managing and measuring electrical resistance is a critical aspect to ensure optimal performance and safety. Ring terminals, which serve as the endpoint for electrical connections in industrial and automotive environments, must be engineered to handle various current levels without exceeding their thermal limits or compromising the integrity of the circuit. To effectively manage resistance within these terminals, manufacturers and engineers must consider the material composition of the ring, its gauge, and the quality of the terminal’s connection to conductive elements. Utilizing precise measurement tools such as multimeters and ohmmeters, one can accurately determine the electrical resistance of ring terminals under different conditions. This data is invaluable for predicting performance under load, selecting appropriate gauges for specific current requirements, and preventing overheating or potential failure points that could lead to safety hazards. Regular monitoring and maintenance are essential to maintain low resistance values, which in turn ensure efficient power transmission and prolong the lifespan of the ring terminals. By carefully selecting and managing ring terminals, industries can avoid costly downtime and enhance the reliability and efficiency of their electrical systems.
Best Practices for Selecting Ring Terminals Based on Resistance Requirements
When selecting ring terminals for applications with specific electrical resistance requirements, it is crucial to consider several factors to ensure optimal performance and safety. The first consideration should be the material composition of the ring terminal itself. Copper alloys are often preferred due to their superior conductivity, but stainless steel options are available for environments with corrosive elements or high mechanical stress. Additionally, the gauge or thickness of the ring terminal wire is a key determinant of resistance; thinner wires have higher resistance values. It’s also essential to match the ring terminal’s cross-sectional area with the cable’s AWG (American Wire Gauge) size to maintain consistent current flow and minimize voltage drop.
Furthermore, the environmental conditions in which the ring terminals will operate must be taken into account. Extreme temperatures can affect resistance values; therefore, selecting a terminal that maintains its conductivity within the expected temperature range is necessary. Environmental factors such as moisture, vibration, and exposure to solvents or chemicals can also degrade performance over time. Thus, choosing terminals with appropriate insulation and corrosion-resistant finishes will help ensure longevity and reliability. Manufacturers often provide datasheets that detail resistance values under different conditions, which should be referenced during the selection process to comply with industry standards and safety regulations. By carefully considering these factors, users can select ring terminals that meet their electrical resistance requirements and contribute to the overall efficiency and longevity of their electrical systems.
Advanced Technologies and Innovations in Ring Terminal Design to Minimize Resistance
The design and function of ring terminals have undergone significant advancements with the advent of cutting-edge technologies aimed at minimizing electrical resistance. Engineers have recognized that low resistance in ring terminals is paramount for maximizing efficiency and performance in electrical systems. Innovations in materials science have led to the development of high-conductivity alloys, such as copper alloys, which exhibit superior conductivity properties compared to traditional metals used in ring terminals. These advanced alloys not only reduce resistance but also enhance durability and corrosion resistance, ensuring longevity under harsh environmental conditions.
Furthermore, the geometry of ring terminals has been optimized through computational modeling and simulation techniques. By analyzing the current flow paths within the terminal, designers can fine-tune the cross-sectional area and overall shape to ensure minimal voltage drop across the connection. This approach, combined with the strategic placement of vents or cooling channels, further contributes to the reduction of resistance by dissipating heat generated during electrical transmission. These advancements in ring terminal design are critical for applications that require high reliability and consistent performance, such as automotive wiring harnesses, industrial machinery, and renewable energy systems.