Mastering Vacuum Casting Techniques for Superior Jewelry Creation
Vacuum casting represents a significant advancement in the jewelry manufacturing process, enhancing …….
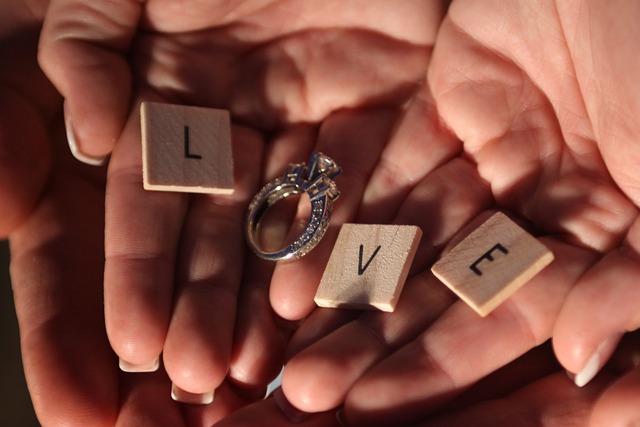
Vacuum casting represents a significant advancement in the jewelry manufacturing process, enhancing the precision and consistency of intricate jewelry designs through the integration of technology with artistry. This method, an advanced form of investment or lost-wax casting, involves sculpting a wax mold that captures every detail of the design, followed by applying a vacuum to the investment material to remove air bubbles, crucial for the integrity and quality of the final cast. The process continues with heat treatment to burn out the wax and allow molten metal to accurately fill the mold, resulting in high-fidelity jewelry with a superior surface finish. Gold, silver, and platinum are commonly used metals, each chosen for their unique properties that align with the design's requirements, market positioning, and wearer's needs. Vacuum casting's unparalleled accuracy, coupled with the selection of appropriate materials, allows jewelers to bring complex designs to life, pushing the boundaries of fine jewelry production. The fusion of modern technology, like CAD/CAM, with traditional techniques has revolutionized the industry, making it more accessible for designers at all levels to create high-quality, detailed, and durable pieces. This innovation continues to expand the range of exceptional jewelry designs available in the market today.
Discover the artistry behind exquisite jewelry with an in-depth exploration of vacuum casting, a technique revolutionizing the world of fine adornments. In our comprehensive guide, “Vacuum Casting in Jewelry,” we delve into the precision and elegance that this process affords. From selecting the optimal metal for your design to mastering the art of casting, learn how vacuum casting can elevate your jewelry designs and production quality. Join us as we examine the innovations driving this transformative technique and unlock new realms of creativity in the jewelry realm.
- Unlocking the Secrets of Precision: The Jewelry Casting Process
- Material Matters: Choosing the Right Metal for Vacuum Casting in Jewelry
- Mastering Vacuum Casting Techniques for Exquisite Jewelry Pieces
- Innovations in Vacuum Casting: Elevating Jewelry Design and Production
Unlocking the Secrets of Precision: The Jewelry Casting Process
Vacuum casting, a meticulous process within the realm of jewelry manufacture, epitomizes the fusion of technology and artistry. This technique, often referred to as lost-wax casting, has been refined through the introduction of vacuum systems that enhance precision and repeatability. The process begins with creating a wax mold that accurately reflects the intricate design of the intended piece of jewelry. Once the wax model is crafted, it undergoes a precise investment process where a slurry of silica particles and a binding agent is applied to the wax, filling every contour and ensuring a consistent thickness across the mold. Here, vacuum casting distinguishes itself by applying a vacuum to remove air bubbles from within the investment, which can otherwise compromise the integrity of the final cast. This step is crucial for achieving high-quality, detailed jewelry with a flawless finish.
Following the investment stage, the mold is heated in a controlled environment to burn out the wax, leaving an empty space that will be filled by molten metal. The vacuum casting process ensures that the metal fills the mold without voids or imperfections, resulting in a piece that is a near-perfect replica of the original design. This high degree of accuracy and consistency is what makes vacuum casting an indispensable tool for jewelry designers and manufacturers who prioritize quality and durability in their products. The ability to repeatedly produce identical pieces with this level of detail makes it a cornerstone technique in the modern jewelry industry, allowing artisans to bring their most intricate designs to life with unparalleled precision.
Material Matters: Choosing the Right Metal for Vacuum Casting in Jewelry
In the realm of fine jewelry, the material chosen for casting plays a pivotal role in determining the quality and durability of the final product. Vacuum casting, a precise and clean method of investment casting, demands metals that not only align with the intricate details required in jewelry design but also possess properties conducive to this specialized process. Gold, both yellow and white, is a popular choice for its luster and malleability, making it ideal for creating intricate pieces with fine details. Silver, with its affordability and natural shine, is another favorite for casting, particularly for mass-produced jewelry where cost efficiency is a key factor. Platinum, known for its strength and white color, is selected for high-end pieces that require greater resilience and a more premium appeal. Each of these metals has unique characteristics that contribute to the integrity and beauty of the finished jewelry. The choice between gold, silver, and platinum should be informed by the intended design, budget, and the desired longevity of the piece.
When opting for vacuum casting in jewelry production, it is crucial to consider not only the aesthetic appeal but also the practical aspects of the chosen metal. For instance, gold alloys, often containing a mix of silver, copper, and zinc, offer a balance between strength and ductility, essential for casting complex designs without compromising on the final product’s integrity. Silver, in its purest form (990), is ideal for detailed castings due to its high thermal conductivity, which ensures even heating and cooling during the casting process. Additionally, the choice of metal can influence the wearability and skin-friendliness of the jewelry. For example, hypoallergenic options like nickel-free white gold or palladium are preferred for sensitive skin. In jewelry casting, the selection of the right metal is a symphony of artistry and science, where the desired outcome is achieved through meticulous material choice and precise technical execution.
Mastering Vacuum Casting Techniques for Exquisite Jewelry Pieces
Mastering vacuum casting techniques in jewelry making opens a realm of creative possibilities for artisans and designers. This process, also known as investment casting, involves creating a wax mold that accurately reflects the intricate details of the desired jewelry piece. The vacuum casting method ensures that even the most delicate designs are faithfully replicated in metal, resulting in high-precision pieces with a flawless finish. The initial step involves crafting a master model, which serves as the blueprint for the final jewelry item. Artisans must possess a deep understanding of materials and the intricacies of wax modeling to ensure that the model is both durable and detailed enough for replication. Once the master model is complete, it undergoes a process where molten metal is introduced into the vacuum-formed wax mold. The vacuum casting technique facilitates the removal of air bubbles, leading to a higher quality final product with minimal porosity or surface defects. This process allows for consistent and repeatable results, which is essential for mass producing jewelry while maintaining the highest standards of quality and craftsmanship. Jewelry casting, particularly through vacuum casting, has revolutionized the industry by providing a means to produce pieces that are both exquisite and precise, making it an indispensable skill for modern jewelers.
Innovations in Vacuum Casting: Elevating Jewelry Design and Production
Vacuum casting, a process that has revolutionized the realm of jewelry design and production, continues to evolve with cutting-edge innovations. These advancements have significantly refined the intricacy, detail, and scalability of jewelry casting, enabling designers to bring their most elaborate concepts to fruition with unprecedented precision. The vacuum casting method involves creating a master model, producing a silicone mold through vacuum suction casting, and then injecting molten metal into it under a controlled vacuum environment. This technique not only yields high-quality castings but also reduces the porosity and defects typically found in traditional casting methods.
The integration of advanced materials in mold making and new alloys in jewelry manufacturing has further enhanced the durability and beauty of cast pieces. Additionally, the incorporation of computer-aided design (CAD) and computer-aided manufacturing (CAM) technologies has streamlined the design process, allowing for rapid prototyping and iteration. This synergy between modern technology and traditional craftsmanship has democratized high-quality jewelry production, making it accessible to artisans of all levels while pushing the boundaries of what is possible in fine jewelry design. The result is a diverse array of exquisite pieces that are both intricate and robust, showcasing the full potential of vacuum casting in the jewelry industry.