Mastering Complex Jewelry Shapes: A Guide to Advanced Casting Techniques
Jewelry casting has undergone significant transformations with the integration of advanced technolog…….
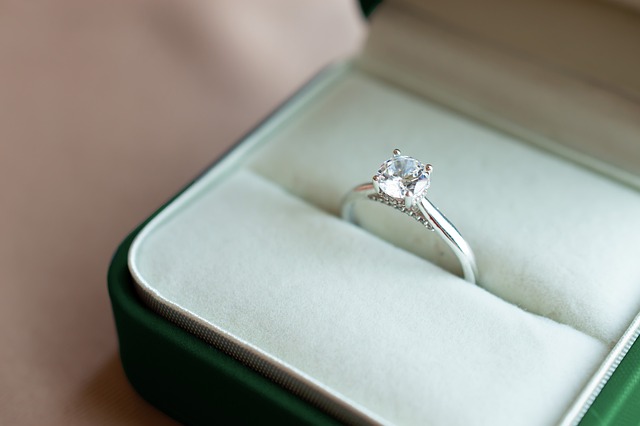
Jewelry casting has undergone significant transformations with the integration of advanced technologies like computer-aided design (CAD) and modern casting methods such as 3D printing of molds and investment casting. These innovations have allowed for precise reproduction of intricate jewelry designs, capturing fine details with minimal distortion. The process begins with virtual prototyping using CAD software, enabling designers to make detailed adjustments before the actual mold is produced. The choice between casting methods depends on design complexity, material selection, and desired surface finish, ensuring each piece is crafted with fidelity to its original design. Investment casting stands out for its ability to preserve delicate details like filigree and engravings, making it particularly suited for luxury jewelry. The use of advanced alloys has enhanced the quality, durability, and luster of cast pieces, catering to both daily wear and heirloom-quality jewelry. The ongoing advancements in casting processes continue to expand the possibilities for artists, offering a richer medium for artistic expression. The article emphasizes the critical role of material selection, with metals like gold, silver, platinum, and palladium chosen for their specific properties, contributing to the visual appeal, structural integrity, and longevity of the jewelry. The precision and accuracy in mold making are paramount to accurately translate artistic visions into physical form, ensuring that the final product reflects the designer's intent with exactness. These advancements have revolutionized the industry, creating a harmonious blend of traditional craftsmanship with cutting-edge technology, resulting in jewelry pieces that capture the essence of both artistic mastery and technical precision.
Jewelry casting transforms intricate designs into wearable art, a process as rich in history as it is in technical complexity. This article delves into the nuances of casting complex shapes in jewelry making, highlighting the evolution and advancements in this craft. From selecting the optimal materials and alloys to mastering the art of mold making for detailed designs, we explore the intricacies that elevate jewelry casting to an art form. Additionally, we examine cutting-edge techniques ensuring high-quality finishes that capture every facet of a designer’s vision. Discover the intersection of creativity and precision in the world of fine jewelry casting.
- Overview of Jewelry Casting Techniques for Complex Shapes
- Material Considerations and Alloy Selection in Jewelry Casting
- Precision and Accuracy in Mold Making for Intricate Jewelry Designs
- Innovative Approaches to Achieving High-Quality Finishes in Cast Jewelry
Overview of Jewelry Casting Techniques for Complex Shapes
Jewelry casting is a meticulous process that allows artisans to bring intricate and elaborate designs into tangible reality. This technique involves creating molds capable of capturing the nuanced details inherent in complex shapes, which are often challenging to replicate with precision. Traditional lost-wax casting remains a cornerstone method within the jewelry industry, particularly for its ability to accurately produce fine details while ensuring minimal distortion in the final piece. Modern advancements in casting techniques have introduced new technologies such as 3D printing of molds and investment casting, which have expanded the possibilities for designers and jewelers to innovate with geometrically intricate and organic forms that were once difficult or impossible to cast.
The process of jewelry casting for complex shapes begins with a detailed design that is often modeled in digital form using computer-aided design (CAD) software. This virtual prototype allows for precise adjustments and optimizations before the physical mold is created. The choice between different casting methods depends on factors such as the complexity of the design, the material used, and the desired surface finish. For instance, investment casting allows for a high degree of detail preservation due to its precision in creating a ceramic shell that closely follows the intricate pattern of the original wax model. This technique is particularly adept at reproducing fine filigree work and delicate engravings that are characteristic of high-end jewelry pieces. Additionally, the integration of advanced alloying techniques has enhanced the durability and luster of cast jewelry, making it suitable for everyday wear or heirloom-quality pieces. The evolution of casting processes continues to push the boundaries of what is possible in jewelry design, offering artists a broader palette with which to express their creativity.
Material Considerations and Alloy Selection in Jewelry Casting
In the realm of jewelry casting, material considerations and alloy selection are paramount for achieving both aesthetic appeal and durability in intricate designs. The choice of material directly influences the final outcome, as different metals offer distinct properties and characteristics. Gold, silver, platinum, and palladium are common precious metals used in jewelry casting, each with its own composition and attributes. For instance, gold alloys are known for their luster and malleability, making them ideal for creating complex shapes that require a softer metal to mold without losing structural integrity. The karat value of gold—ranging from 10k to 24k—determines its strength and the proportion of other metals like copper or nickel it contains. Similarly, silver casting can benefit from alloys such as argentium or sterling silver, which include a higher percentage of another metal, typically germanium or copper, enhancing the metal’s workability and wear resistance.
Alloy selection in jewelry casting extends beyond mere aesthetics; it also involves considerations for wearability and longevity. For example, adding palladium to white gold alloys can improve durability, as it has a natural whiteness and is less prone to tarnish. Additionally, the choice of alloy affects the casting process itself, with some alloys requiring specific temperatures and techniques for optimal results. Casting complex shapes demands an understanding of how different metals behave under heat and during cooling processes. The precision of the investment casting method, commonly used in jewelry manufacturing, relies on the accurate melting and pouring of these alloys to capture the fine details of the design. Consequently, jewelers must carefully select alloys that not only complement the design but also align with the technical aspects of the casting process to ensure the final product meets the high standards expected in fine jewelry.
Precision and Accuracy in Mold Making for Intricate Jewelry Designs
In the realm of jewelry casting, precision and accuracy in mold making are paramount for the creation of intricate designs. The process begins with meticulous modeling, where the artist’s vision is translated into a three-dimensional form using advanced CAD (Computer-Aided Design) software. This digital prototype allows for minute adjustments to be made before the physical mold is constructed, ensuring that every facet of the design is captured with exactitude. The mold itself, crafted from materials such as silicon or polyurethane, must adhere closely to the dimensions specified in the digital model to facilitate a casting process that yields high-fidelity results. The complexity of the jewelry piece, with its myriad of curves and details, demands a mold that is both durable and precise, to accommodate the intricate patterns and textures without distortion or loss of detail. The skillful union of jewelry casting techniques with the precision of modern technology in mold making ensures that each piece, from an elegant ring to a stunning piece of wearable art, emerges with the intended beauty and craftsmanship, ready to captivate its future admirer.
Innovative Approaches to Achieving High-Quality Finishes in Cast Jewelry
Innovations in jewelry casting have significantly advanced, allowing for intricate and complex shapes to be cast with high-quality finishes. The traditional lost-wax casting method has been refined through the incorporation of digital modeling techniques. Designers now leverage computer-aided design (CAD) software to create detailed 3D models of their jewelry pieces. These models are then transformed into physical molds using 3D printing technology, ensuring precision and consistency in each cast. The high-resolution printers used for this purpose can produce fine details that were previously unattainable, enabling a level of complexity and sophistication in the finished pieces.
Furthermore, advancements in casting materials have expanded beyond traditional alloys to include novel composites that offer superior durability and luster. The integration of rare earth metals has led to enhanced mechanical properties and improved surface finishes. Post-casting processes such as tumbling and polishing are also being optimized with automated systems that maintain a consistent finish, removing the need for manual labor which can introduce inconsistencies. These automated processes not only ensure a high-quality finish but also reduce production time, allowing jewelers to meet the increasing demand for handcrafted, yet technically precise, cast jewelry. The synergy of cutting-edge technology and traditional craftsmanship in jewelry casting continues to push the boundaries of what is possible, resulting in exquisite pieces that showcase the pinnacle of artisan skill and technical innovation.