10 Practical Steps for Cost-Effective Jewelry Casting on a Budget
Jewelry casting offers artisans a range of cost-effective techniques and materials to create afforda…….
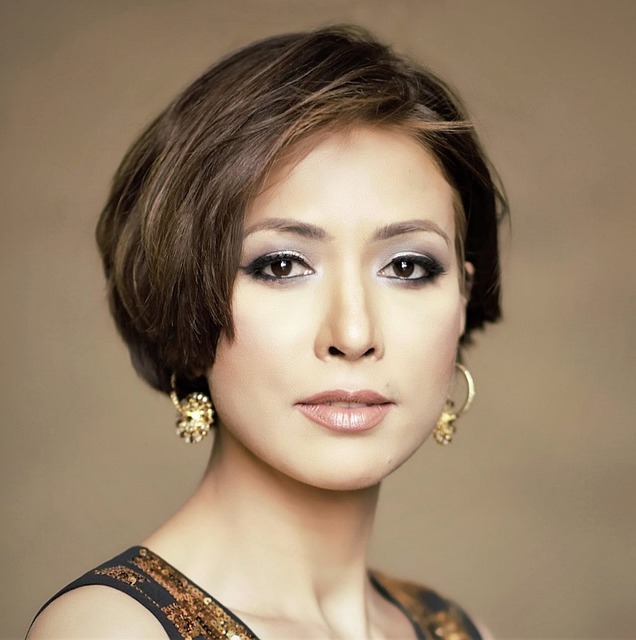
Jewelry casting offers artisans a range of cost-effective techniques and materials to create affordable yet quality pieces. The three main methods—lost-wax, cold-connection casting, and hand-fabrication—each offer different trade-offs in terms of precision, cost, and aesthetic appeal. Lost-wax casting is revered for its high precision but is more expensive due to its complex process. Cold-connection casting is a less costly alternative that involves soldering metal pieces together, offering similar visual results at a reduced price. For those looking to save even further, materials like zinc or titanium alloys can produce durable jewelry without the premium of precious metals. Sterling silver, an alloy with tarnish-resistant qualities, and base metal alloys like aluminum and zinc are favored for their affordability and design versatility. Simulants like cubic zirconia mimic the look of precious stones at a fraction of the cost, while pewter and bronze provide strength and distinctive textures. When choosing an affordable jewelry casting service, it's important to consider the foundry's expertise, material costs, labor, and equipment, as well as their portfolio, customer service, and turnaround times. For DIY enthusiasts, jewelry casting kits enable home casting with materials like sterling silver or simulated precious stones, allowing for personalized creations without substantial investment. Success in DIY casting depends on careful preparation of molds, patience during the curing process, and creative experimentation to optimize results. Recycling scrap metal can also save costs. As crafters advance, they can produce unique, artisanal pieces and potentially develop a profitable craft business.
Explore the art of jewelry casting without breaking the bank. Our comprehensive guide delves into cost-effective casting techniques, materials, and services for budget-conscious artisans. Whether you’re a seasoned crafter or new to the bench, this article provides valuable insights into affordable options in jewelry casting. Discover how to craft stunning pieces with a focus on sustainable materials and budget-friendly foundries. With our expert tips and tricks for DIY casting on a shoestring, you’ll elevate your jewelry line while maintaining financial flexibility. Dive into the world of accessible and quality jewelry casting now.
- Understanding Jewelry Casting Techniques for Budget-Conscious Artisans
- Overview of Cost-Effective Materials Suitable for Jewelry Casting
- Assessing Affordable Jewelry Casting Services and Foundries
- DIY Jewelry Casting on a Shoestring: Tips and Tricks for Savvy Crafters
Understanding Jewelry Casting Techniques for Budget-Conscious Artisans
When artisans are exploring affordable jewelry casting options, it’s crucial to have a foundational understanding of the various techniques available. Casting jewelry can range from lost-wax casting, also known as investment casting, to more cost-effective methods like cold-connection or hand-fabricated pieces. Each technique offers different advantages and considerations in terms of cost, material durability, and the level of detail achievable.
Lost-wax casting, while traditional, can be expensive due to its multi-step process involving creating a wax mold that is then covered with a ceramic slurry before melting out the wax to form the metal piece. However, for budget-conscious artisans looking for high-quality pieces, considering alternative processes like cold-connection casting can yield similar results at a lower cost. This method involves soldering multiple pieces of metal together to create a larger piece, which can then be polished and finished to resemble a single casting. It’s a technique that requires skill but offers a cost-effective solution for producing intricate designs without the higher expenses associated with full castings. Artisans should also look into the use of zinc or titanium alloys as alternative materials, which can be more economical than precious metals like gold or platinum while still offering durability and an attractive appearance. Understanding these casting techniques empowers jewelers to make informed decisions that align with their creative vision and budgetary constraints.
Overview of Cost-Effective Materials Suitable for Jewelry Casting
When exploring cost-effective materials for jewelry casting, caster jewelers often consider a variety of options that balance affordability with durability and aesthetic appeal. One such material is sterling silver, an alloy composed of 92.5% silver and 7.5% other metals, typically copper or gauge. Its tarnish-resistant nature makes it a popular choice for fine jewelry pieces. Another viable option is base metal alloys like aluminum and zinc, which can be cost-effective and offer versatility in design. These materials are often used for mass-produced items due to their relatively lower melting points and ease of casting. For those seeking a gemstone-bearing piece without the high cost of precious stones, cubic zirconia and other simulants provide an economical alternative that mimics the look of more expensive diamonds or sapphires. Additionally, materials like pewter and bronze are gaining traction among artisans for their strength and rich textures, which can add a unique touch to castings. Each of these materials offers a distinct look and feel, catering to different styles and budgets in the jewelry market. Jewelry casting using these cost-effective materials allows designers and makers to experiment with new designs and offer competitive pricing without compromising on quality. It’s important for jewelers to select materials that not only align with their budget but also meet the expectations of their clientele regarding wearability, longevity, and aesthetic value.
Assessing Affordable Jewelry Casting Services and Foundries
When exploring affordable jewelry casting options, it’s crucial to assess various services and foundries for their quality, reliability, and cost-effectiveness. Potential crafters should begin by researching the different types of casting methods available, such as lost-wax casting or investment casting, to determine which aligns with their budget and design requirements. Each method has its own set of costs associated with material, labor, and equipment use. It’s essential to consider the reputation and experience of the foundry in delivering precision and detail in castings, as this directly impacts the quality of the final piece.
In evaluating foundries for jewelry casting, one should examine their past work through portfolios or case studies. This allows for an understanding of their expertise in handling different types of metal, sizes, and intricacies of designs. Additionally, inquiries about their customer service, turnaround times, and willingness to collaborate on design refinements can provide insight into the level of support and partnership offered. By carefully assessing these aspects, artisans can select a foundry that not only meets their budgetary constraints but also upholds the integrity and aesthetics of their jewelry designs.
DIY Jewelry Casting on a Shoestring: Tips and Tricks for Savvy Crafters
For those with a passion for crafting and a penchant for jewelry, DIY jewelry casting offers an accessible route to transform your designs into wearable art without breaking the bank. On a shoestring budget, savvy crafters can leverage cost-effective materials and methods to achieve professional results. To begin with, sourcing materials is crucial; look for affordable investment options like sterling silver or base metals that mimic the appearance of more expensive materials. These can be found at craft stores or specialty suppliers, often at a fraction of the cost of fine metals. Additionally, opting for smaller scale casting processes, such as lost-wax casting, becomes more manageable when working with artisan or hobbyist jewelry casting kits designed for home use. These kits, while initially requiring an investment, can be used repeatedly, thus reducing costs over time.
When it comes to the technical aspects of DIY jewelry casting, a few key tips and tricks are invaluable. Ensure that your mold is well-prepared; a crisp, clean mold leads to a successful cast. Practice patience with the curing and cooling processes, as these steps significantly impact the integrity of the final piece. Experiment with different techniques to find what works best for your specific project. For instance, adjusting the packing of the investment material or fine-tuning the pour temperature can yield better results. Furthermore, consider recycling scrap metal to minimize waste and reduce costs even further. By embracing the learning curve associated with DIY jewelry casting, you’ll not only create unique pieces that reflect your creativity but also hone skills that could lead to a profitable crafting endeavor. With careful planning and attention to detail, the world of jewelry design is yours to explore, cast by cast.