Composites Explored: From Hardware Washers to Diverse Applications
Composite types, combining simple data types into complex structures, offer significant advantages i…….
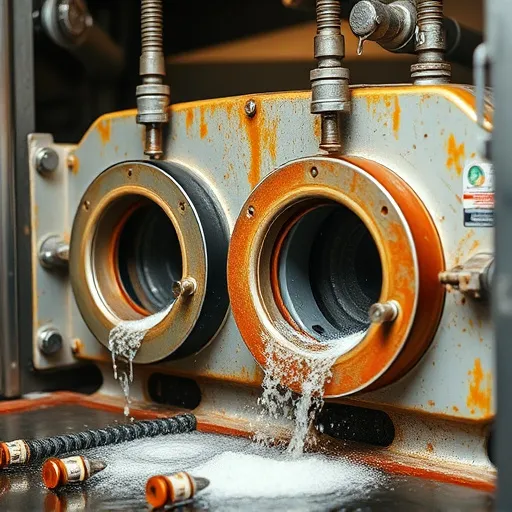
Composite types, combining simple data types into complex structures, offer significant advantages in software development, especially for managing real-world relationships. Hardware washers, composed primarily of metal alloys with specialized additives, provide robust performance across multiple industries. Using composites in manufacturing offers benefits like lightweight design, increased durability, and superior corrosion resistance, making them ideal for fuel-efficient automotive, aerospace, marine, and sports equipment. Despite challenges in integration and material quality, the future of composite materials looks innovative, with smart materials, sustainable resources, and advanced structural monitoring trends promising enhanced performance, reduced weights, and extended lifespans, particularly in hardware washers.
“Composite Types: Redefining Material Science for Modern Manufacturing delves into the multifaceted world of composite materials, offering a comprehensive overview. From the fundamental concept to practical applications, this article explores how these advanced composites revolutionize industries. We dissect their physical composition, particularly focusing on hardware washers, and highlight advantages in manufacturing.
Beyond traditional uses, we uncover diverse applications, while also addressing challenges and future trends shaping this game-changing technology, with a special focus on hardware washer innovations.”
- Understanding Composite Types: An Overview
- Hardware Washers: The Physical Composition
- Advantages of Using Composites in Manufacturing
- Applications Beyond Hardware: Diversifying Use Cases
- Challenges and Limitations to Consider
- Future Trends Shaping Composite Innovation
Understanding Composite Types: An Overview
Composite types, in the realm of programming and data structures, refer to a powerful concept where simple, fundamental types are combined to create more complex data types. This approach offers several advantages, particularly in managing intricate data relationships within software systems. By using composite types, developers can model real-world entities more accurately, enabling efficient storage and manipulation of data.
One practical application of composite types is seen in hardware washers, where various components like screws, bolts, and washers themselves are not just individual units but part of a larger assembly. Modeling these relationships with composites allows for easier tracking, maintenance, and updates. This concept streamlines code, enhances readability, and promotes modular design, making it a cornerstone in modern software development practices.
Hardware Washers: The Physical Composition
Hardware washers, a fundamental composite type, encompass a diverse array of materials combined to create a robust and versatile component. These washers are typically crafted from a blend of metal alloys, such as steel or brass, infused with specialized additives to enhance their structural integrity and resistance to corrosion. The physical composition involves meticulously balancing these elements to achieve optimal performance in various applications.
The design of hardware washers varies based on the specific requirements of different projects. Some common compositions include carbon steel for general-purpose uses, offering a balance between strength and cost-effectiveness. For environments demanding higher corrosion resistance, stainless steel washers are preferred, featuring chromium and nickel content to safeguard against rust formation. This attention to material selection and customization ensures that hardware washers cater to diverse needs, making them indispensable in industries ranging from automotive to construction.
Advantages of Using Composites in Manufacturing
Using composites in manufacturing offers numerous advantages, particularly in enhancing product performance and efficiency. One of the key benefits is their lightweight nature; composite materials can be designed to have a lower density than traditional metals, which reduces weight without compromising strength. This is especially advantageous in industries like automotive and aerospace, where fuel efficiency and maneuverability are paramount.
Moreover, hardware washers made from composites can provide superior corrosion resistance, making them ideal for outdoor or wet environments. Composites also offer increased durability and longevity compared to conventional materials. They are less susceptible to fatigue and wear, ensuring products last longer even under heavy usage. This reduces the need for frequent replacements, saving costs in the long run.
Applications Beyond Hardware: Diversifying Use Cases
Composite types, initially designed for hardware washers and similar engineering applications, have diversified their use cases far beyond traditional industrial settings. This versatility is driven by the unique properties that composites offer, such as lightweight construction, superior strength-to-weight ratio, and resistance to corrosion and wear. These advantages are now being leveraged in sectors like aerospace, automotive, marine, and even sports equipment, where performance and durability are paramount.
From advanced aircraft components requiring extreme precision to high-performance sailing yachts demanding longevity under harsh conditions, composites provide innovative solutions. Their ability to be tailored for specific functions and environments opens up a world of possibilities, transforming industries and challenging traditional material choices. This expansion into new territories highlights the potential of composite types as game-changers not just in hardware, but across diverse fields demanding advanced materials.
Challenges and Limitations to Consider
When exploring composite types, it’s crucial to acknowledge the challenges and limitations inherent in their design and implementation. One significant hurdle is ensuring compatibility with existing hardware washers and systems. Composite materials, by their nature, often require specialized equipment and processes for manufacturing and assembly, which can be a barrier to integration into established industrial practices.
Moreover, the performance and durability of composite types depend heavily on the quality of raw materials, production techniques, and construction methods. Variabilities in these factors can lead to unpredictable outcomes, affecting structural integrity, resistance to wear and tear, and overall longevity—especially when dealing with demanding applications like those found in automotive or aerospace sectors where robust hardware washers are indispensable.
Future Trends Shaping Composite Innovation
The future of composite types is poised for significant innovation, driven by advancements in materials science and technology. One notable trend is the increased integration of smart materials into composite structures, enabling them to adapt and respond to external stimuli. For instance, self-healing composites that can repair microscopic damages are being developed, extending the lifespan of these materials. Additionally, the incorporation of sensors and actuators into composite hardware washers is opening new possibilities in structural monitoring and control.
Another emerging trend is the exploration of sustainable and eco-friendly composites, leveraging renewable resources to reduce environmental impact. This shift towards sustainability is not only beneficial for the planet but also presents opportunities for innovation in industries like aerospace and automotive, where lightweight and durable materials are highly sought after. As research progresses, we can expect composite technology to become more sophisticated, offering enhanced performance, reduced weights, and improved longevity across various applications.
Composite types have evolved from their initial application in hardware washers to become a versatile material across various sectors. Their unique properties, such as strength-to-weight ratio and durability, offer significant advantages in manufacturing processes. As research progresses, we can expect further innovations, pushing the boundaries of composite use cases even wider. However, understanding the challenges associated with these materials is crucial for their successful implementation. By addressing limitations and exploring new trends, the future of composites looks promising, revolutionizing industries from aerospace to automotive and beyond.