Mastering Quality Control for Insulated Tumbler Excellence
Quality control is paramount for insulated tumbler manufacturers, ensuring premium products in a com…….
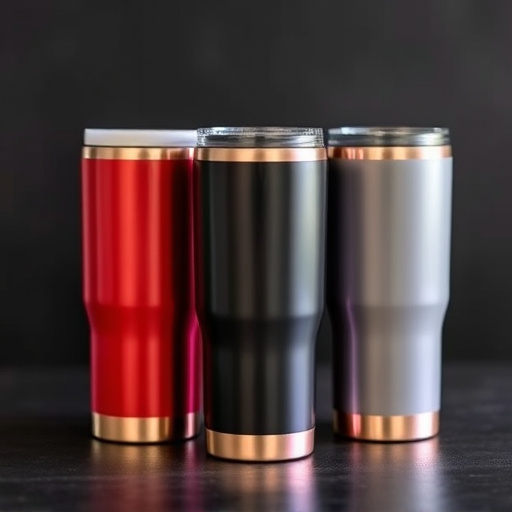
Quality control is paramount for insulated tumbler manufacturers, ensuring premium products in a competitive market. Through rigorous checks from material selection to final inspection, manufacturers guarantee superior insulation efficiency, durability, and safety. This multi-step process includes detailed documentation for early defect identification and corrective actions, leading to consistent temperature retention, enhanced durability, and safe use—crucial factors for building consumer trust and brand loyalty. Inspection, testing (including material integrity, thermal retention, and leak prevention), and standardization are key aspects of this quality control, ultimately driving customer satisfaction and market success in the bustling insulated tumbler industry.
Quality control is the cornerstone of insulated tumbler excellence, ensuring these beverages remain at optimal temperatures for extended periods. This article delves into the essential practices that shape the industry standard for insulated tumblers. We explore key aspects like thorough inspection, rigorous testing procedures, and standardized production processes to maintain consistency. By fostering a culture of continuous improvement, manufacturers stay ahead in the market, providing consumers with durable, high-performing insulated tumblers that keep drinks fresh longer.
- Understanding Quality Control: The Foundation of Insulated Tumblers' Excellence
- The Role of Inspection in Ensuring Durability and Performance
- Testing Procedures for Insulated Tumblers: A Comprehensive Approach
- Maintaining Consistency: Standardization in Production Processes
- Continuous Improvement: Staying Ahead in the Market with Quality Control
Understanding Quality Control: The Foundation of Insulated Tumblers' Excellence
Quality Control is the cornerstone that upholds the superior reputation of insulated tumblers in today’s market. For products designed to keep beverages hot or cold for extended periods, like insulated tumblers, meticulous quality control processes are vital. These rigorous checks ensure each tumbler meets stringent criteria for insulation efficiency, durability, and safety—from material selection to final inspection. By implementing robust quality control measures, manufacturers guarantee that every tumbler leaving their facility performs optimally, retains its aesthetic appeal, and provides consumers with a satisfying experience.
This foundational practice involves a multi-step process encompassing raw material testing, manufacturing surveillance, and comprehensive product assessments. Every stage is meticulously documented to identify potential issues early on, allowing for prompt corrective actions. The result? Insulated tumblers that consistently deliver on their promise of superior temperature retention, enhanced durability, and safe use—a key factor in building consumer trust and fostering brand loyalty.
The Role of Inspection in Ensuring Durability and Performance
Inspection plays a critical role in quality control, especially for products designed for durability and performance like insulated tumblers. A thorough inspection process ensures that each tumbler meets stringent standards for materials, construction, and functionality. By examining factors such as insulation effectiveness, leak-proofing, and structural integrity, manufacturers can identify and rectify defects before the products reach consumers.
This meticulous approach not only guarantees a higher quality product but also enhances customer satisfaction and safety. For insulated tumblers, proper inspection can prevent issues like thermal leaks, poor insulation performance, or flimsy construction, which could render the product unusable or even hazardous. Ultimately, a well-conducted inspection process is key to maintaining consistent quality and ensuring that every insulated tumbler performs optimally over time.
Testing Procedures for Insulated Tumblers: A Comprehensive Approach
When it comes to testing procedures for insulated tumblers, a comprehensive approach is essential to ensure product quality and customer satisfaction. The process begins with rigorous material inspection, checking for any defects or inconsistencies in the insulation material, seals, and overall construction. This step is vital as even minor issues can compromise the tumbler’s performance.
Subsequent testing involves filling the tumblers with hot and cold beverages to simulate real-world conditions. This includes evaluating thermal retention capabilities, ensuring the insulated tumbler maintains the desired temperature for extended periods. Additionally, leak tests are conducted to verify the integrity of seals and connections. By combining these meticulous procedures, manufacturers can deliver top-quality insulated tumblers that provide excellent temperature control and prevent leaks, enhancing consumer experience.
Maintaining Consistency: Standardization in Production Processes
In the quest for unparalleled product quality, maintaining consistency across production processes is paramount. Standardization plays a pivotal role in this regard, ensuring every item, be it an insulated tumbler, meets predefined specifications and standards. By implementing consistent methods and protocols, manufacturers can guarantee that each tumbler produced adheres to the same high-quality threshold. This standardization not only streamlines manufacturing but also fosters reliability among consumers who expect uniform performance from every product they purchase.
For instance, in the production of insulated tumblers, standardization might involve meticulous temperature control during the insulation process, precise measurements for material composition, and consistent assembly techniques. These standardized procedures ensure that each tumbler offers the same level of insulation, durability, and overall user experience. This commitment to consistency is what builds brand reputation and fosters customer loyalty in a competitive market.
Continuous Improvement: Staying Ahead in the Market with Quality Control
In today’s competitive market, continuous improvement is key to staying ahead—especially in industries like insulated tumblers. Quality control isn’t just about meeting initial standards; it’s a dynamic process that involves regular assessments and adjustments to ensure superior products. By implementing robust quality control measures, manufacturers of insulated tumblers can identify and rectify issues early on, leading to enhanced product reliability and customer satisfaction.
This proactive approach fosters innovation and adaptation, allowing companies to respond swiftly to changing consumer preferences and market trends. Continuous improvement in quality control enables businesses to produce insulated tumblers that not only meet but exceed expectations, solidifying their position in a crowded marketplace.
In conclusion, quality control is paramount for maintaining and enhancing the excellence of insulated tumblers. Through a comprehensive understanding of this process, rigorous inspection protocols, meticulous testing procedures, and consistent production standards, manufacturers can ensure these tumblers deliver optimal performance and durability. By embracing continuous improvement, industry leaders not only stay ahead in the market but also provide consumers with superior products that cater to their needs, solidifying the reputation of insulated tumblers as indispensable companions for various lifestyle occasions.