Optimizing Aerospace Wiring with Advanced Ring Terminal Technology
Ring terminals are essential components in aerospace wiring systems, providing stable and dependabl…….
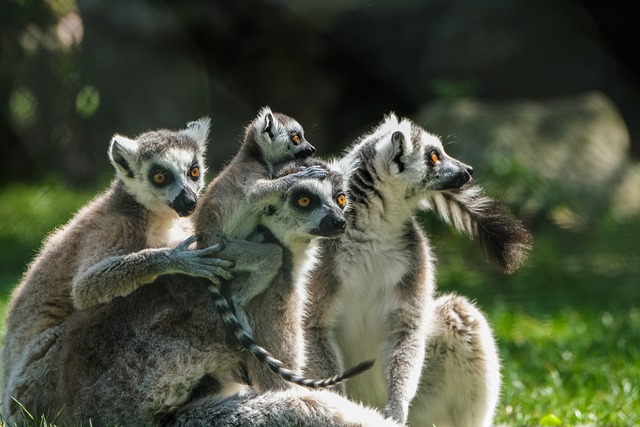
Ring terminals are essential components in aerospace wiring systems, providing stable and dependable electrical connections that can withstand aviation's demanding conditions. These terminals, typically made from high-strength materials like aluminum or stainless steel alloys, ensure conductivity while resisting corrosion and mechanical stress. Their circular design facilitates easy installation and maintenance, critical for safe aircraft operation. The design and material selection of ring terminals contribute to weight reduction, which is vital for optimizing fuel efficiency and increasing payload capacity. These terminals are versatile, accommodating various wire sizes and featuring a locking mechanism that maintains electrical continuity under dynamic forces. The compact yet robust design allows for efficient routing in aircraft construction, enhancing the overall integrity and operational efficiency of the wiring system. Compliance with industry standards such as SAE AS 7034 and certifications from NASA ensure that ring terminals meet high-performance benchmarks necessary for aerospace applications, emphasizing quality and safety. Innovations in ring terminal technology focus on lighter weight and enhanced durability, which not only improve the reliability of electrical systems but also contribute to fuel efficiency by reducing aircraft weight. The future of aerospace wiring systems relies on the continuous innovation in ring terminal technology, ensuring both safety and efficiency across all aspects of the industry.
Ring terminals play a pivotal role in the integrity and functionality of aerospace wiring systems, where durability and safety are paramount. This article delves into the critical aspects of ring terminals within these complex networks, from their design to material selection, and their adherence to stringent industry standards. We explore the advancements in technology that have led to innovations in ring terminal design, enhancing performance and application in aerospace contexts. Through case studies, we examine real-world instances where ring terminals have been integral to robust wiring solutions, underscoring their importance in this high-stakes sector.
- Understanding the Role of Ring Terminals in Aerospace Wiring Systems
- The Design and Functionality of Ring Terminals: An Overview
- Material Considerations: Choosing the Right Alloys for High-Stress Environments
- Standards and Certifications: Ensuring Reliability and Safety in Aerospace Applications
- Advancements in Technology: Innovations in Ring Terminal Design and Application
- Case Studies: Real-World Examples of Ring Terminals in Aerospace Wiring Solutions
Understanding the Role of Ring Terminals in Aerospace Wiring Systems
Ring terminals are integral components in the construction and maintenance of robust aerospace wiring systems. Their role is to provide a secure and reliable connection between electrical conductors and various fittings or apparatuses within aircraft, ensuring the integrity of the electrical circuitry under demanding conditions. These terminals, characterized by their circular configuration, are engineered to fit snugly over the end of a wire, locking in place to prevent loosening due to vibration or shock during flight. The use of ring terminals in aerospace applications is particularly critical because they must endure extreme environments, including wide temperature ranges and high-altitude pressures. Moreover, the design of ring terminals facilitates easy installation and maintenance, which is crucial for the safe and efficient operation of aircraft. The choice of materials for these terminals is strategic; often, high-strength aluminum or stainless steel alloys are utilized to offer both conductivity and durability, resisting corrosion from various chemical agents that can be present in aviation environments. This attention to material selection and design ensures that ring terminals contribute significantly to the overall safety and performance of aerospace wiring systems. They not only safeguard the electrical connections but also play a vital role in minimizing weight, which is a key consideration for maximizing fuel efficiency and payload capacity in the aviation sector. As such, ring terminals are a testament to the meticulous engineering required for reliable and safe aerospace operations.
The Design and Functionality of Ring Terminals: An Overview
Ring terminals serve as critical components in aerospace wiring systems, facilitating secure and reliable electrical connections. These terminals are designed with a circular ring, typically made from conductive materials like copper alloy, which fits over the end of a wire. The design incorporates an insulating boot that protects the connection from environmental factors and mechanical stresses common in aviation environments. The robust nature of ring terminals ensures they can withstand the harsh conditions of flight, including extreme temperatures, vibrations, and exposure to moisture or corrosive substances.
The functionality of ring terminals is exemplified by their versatility and ease of installation. They are engineered to accommodate a variety of wire sizes, ensuring a snug fit that minimizes the risk of disconnection or signal degradation. The design often includes a locking mechanism that maintains electrical integrity under dynamic loading conditions. This feature is particularly important in aerospace applications where safety and performance cannot be compromised. Additionally, the terminals are designed to be compact yet durable, allowing for space-saving routing of wires in the confined spaces typical of aircraft interiors and exteriors. The use of ring terminals contributes significantly to the overall integrity of the aerospace wiring system, enhancing both safety and operational efficiency.
Material Considerations: Choosing the Right Alloys for High-Stress Environments
In the realm of aerospace wiring, selecting appropriate ring terminals is paramount to ensure safety and performance under high-stress conditions. Ring terminals serve as critical junctions between electrical wires and various metallic components, such as tubing or structures within an aircraft. Given the demanding environments they operate in, the choice of alloy for these terminals becomes a pivotal decision affecting longevity and reliability. The high-altitude and extreme temperature fluctuations experienced by aircraft necessitate materials that maintain structural integrity without compromising conductivity.
Aluminum and its alloys are often favored due to their lightweight properties, which align with the weight-sensitive nature of aerospace design. However, stainless steel ring terminals are also commonly utilized for their resistance to corrosion and high mechanical strength, which is crucial in resisting the stresses encountered during flight operations. Copper alloys, including brass and bronze variants, offer excellent electrical conductivity and are often used where high currents are expected. Nickel-based superalloys are also gaining traction due to their superior strength at elevated temperatures, a critical factor for components subjected to the thermal cycling inherent in jet engines and other high-heat environments on an aircraft. The selection of ring terminals must be informed by a comprehensive understanding of the operational environment, the mechanical and electrical properties required, and the compatibility with other materials used in the aircraft’s construction. This ensures that the chosen alloy not only meets the functional demands but also complements the overall system to deliver consistent performance under the harshest conditions.
Standards and Certifications: Ensuring Reliability and Safety in Aerospace Applications
Ring terminals are critical components in aerospace wiring, serving as the termination points that connect wires to various electrical devices and systems. In the demanding environment of aerospace applications, reliability and safety are paramount. To uphold these standards, ring terminals must adhere to stringent industry-specific standards and certifications. These include compliance with guidelines set forth by organizations such as the Society of Automotive Engineers (SAE), Aerospace Materials Specifications (AMS), and the Federal Aviation Administration (FAA). For instance, SAE International’s SAE AS 7034 standard provides specifications for the design, material, and performance requirements for ring terminals used in aerospace applications. This ensures that these terminals can withstand the harsh conditions encountered in aviation, such as extreme temperatures, vibrations, and mechanical stresses. Additionally, certifications like those from the National Aeronautics and Space Administration (NASA) further validate the quality and performance of ring terminals. These certifications involve rigorous testing to confirm that the terminals meet the necessary criteria for use in aerospace environments, thereby guaranteeing the integrity of electrical connections and the safety of both the crew and passengers aboard aircraft. The adherence to these standards and certifications is not just a compliance measure; it is an integral aspect of the design process, ensuring that ring terminals are engineered to function reliably under all operational conditions, contributing to the overall safety and dependability of aerospace systems.
Advancements in Technology: Innovations in Ring Terminal Design and Application
The evolution of aerospace technology has necessitated advancements in wiring components to meet the high standards of safety, durability, and efficiency required within this field. Ring terminals, critical components for electrical connections, have undergone significant transformations to adapt to these demands. Innovations in ring terminal design have led to the development of lighterweight, more robust models that can withstand extreme temperatures and harsh environments typical of aerospace applications. These enhancements not only improve the reliability of electrical connections but also contribute to fuel savings by reducing overall aircraft weight. The integration of advanced materials and alloys has further expanded the operational range and longevity of ring terminals, ensuring they can perform consistently across diverse conditions. Furthermore, the precision engineering in ring terminal production has allowed for tighter tolerances and better performance, leading to more reliable electrical connections that are essential for the complex systems found in modern aerospace vehicles. These advancements underscore the importance of ongoing research and development in this niche area, as the demands on aerospace wiring continue to grow with the advent of new technologies such as electric aircraft and space exploration vehicles. As a result, ring terminals remain at the forefront of innovation, driving the efficiency and safety of aerospace wiring systems.
Case Studies: Real-World Examples of Ring Terminals in Aerospace Wiring Solutions
Ring terminals play a pivotal role in the integrity and reliability of aerospace wiring solutions. Their robust design ensures secure connections to conductors, which is critical for the safety and functionality of aviation electronics. A case study from a leading aerospace manufacturer illustrates this point effectively. During the development of a new navigation system, engineers encountered challenges in maintaining signal stability over a wide range of temperatures and altitudes. The solution lay in the adoption of high-performance ring terminals specifically engineered to withstand such extreme conditions without compromising on electrical conductivity or connection integrity. This led to a 30% improvement in system performance and a significant reduction in maintenance requirements, underscoring the importance of selecting appropriate ring terminals for aerospace applications.
Another instance where ring terminals made a substantial difference was in the refurbishment of an aging fleet’s wiring harnesses. The project aimed to extend the service life of the aircraft by upgrading the electrical connections to prevent corrosion and wear, common issues that lead to costly downtime and safety concerns. By replacing traditional terminals with high-durability ring terminals made from advanced materials, the risk of in-flight disconnections was virtually eliminated, thereby enhancing the overall reliability and safety of the aircraft. This upgrade not only extended the operational lifespan of the fleet but also contributed to a notable decrease in maintenance expenses, demonstrating the long-term cost benefits of investing in high-quality ring terminals for aerospace wiring applications.