Durability Checks: Light Guards, Tests, & Future Trends for Quality Assurance
Durability checks, including real-world simulations with light guards, are essential for product qua…….
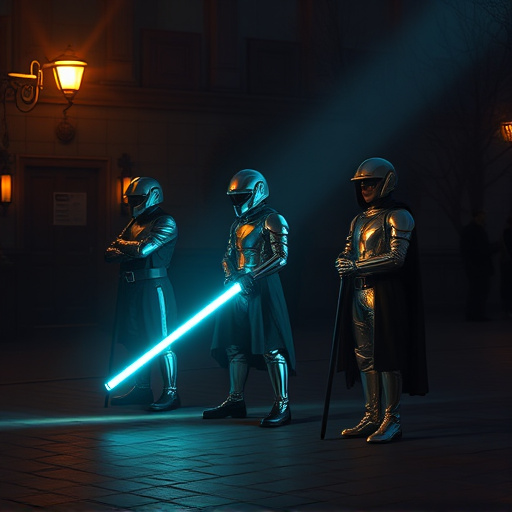
Durability checks, including real-world simulations with light guards, are essential for product quality assurance. These tests identify weaknesses, ensuring products like light guards last in various environments. Light guard technologies enhance test accuracy in industries like automotive and electronics, where they protect against damage and improve performance. Effective durability assessments using tools like LCA and advanced testing methods predict failures, guide improvements, and lead to superior, long-lasting products. Standardization, controlled environments, and leveraging smart materials will further revolutionize durability testing, benefiting manufacturers and consumers alike.
Durability checks are an integral part of ensuring product quality and longevity. In this comprehensive guide, we explore the intricacies of durability testing, from understanding its foundational role in quality assurance to delving into various test types and best practices. Key focus areas include the indispensable role of light guards in enhancing test accuracy, addressing common challenges, and presenting real-world case studies. Additionally, we cast our gaze towards future trends, highlighting innovations shaping the landscape of durability testing.
- Understanding Durability Checks: The Foundation of Quality Assurance
- Why Light Guards Are Essential in Durability Testing
- Types of Durability Tests: A Comprehensive Overview
- Best Practices for Conducting Effective Durability Checks
- Common Challenges in Durability Assessment and How to Overcome Them
- Case Studies: Real-World Applications of Durability Checks
- Future Trends in Durability Testing: Embracing Innovation
Understanding Durability Checks: The Foundation of Quality Assurance
Durability checks are an essential foundation for quality assurance in manufacturing and product development. These tests go beyond basic functionality to ensure that products can withstand real-world conditions over extended periods. By simulating various environmental factors, such as temperature extremes, humidity, and physical stress, durability checks help identify potential weaknesses or failure points. This proactive approach is crucial in creating long-lasting, reliable products that meet customer expectations.
In the context of light guards, for instance, these checks ensure not only that the guard itself remains intact but also that its optical properties remain unaltered over time. Regular durability assessments help maintain consistency and performance, whether it’s a protective shield on a high-tech device or an automotive headlight. This commitment to quality is what fosters customer trust and ensures products deliver consistent value for years to come.
Why Light Guards Are Essential in Durability Testing
In durability testing, light guards play a pivotal role by simulating real-world conditions and protecting test specimens from external damage. These guards are essential because they mimic natural exposure to light, heat, and other environmental factors, ensuring that products are assessed under realistic scenarios. Without proper light guards, tests may not accurately reflect how items perform over time, leading to potentially unreliable results.
By incorporating light guards, testers can evaluate the resilience of materials and finishes, identify potential weaknesses, and predict long-term performance. This is crucial for industries where aesthetics and functionality are paramount, such as automotive, electronics, and construction. Effective light guard usage enhances the integrity of durability tests, enabling manufacturers to make informed decisions and ultimately improve product quality and longevity.
Types of Durability Tests: A Comprehensive Overview
Durability tests are an integral part of product development, ensuring that goods can withstand the rigors of daily use and varying environmental conditions. These tests go beyond basic performance checks to evaluate a product’s longevity and resilience. Among various types, stress testing, exposure testing, and life cycle assessment stand out as comprehensive methods to assess durability.
Stress testing subjects products to intense forces and extreme conditions to simulate accelerated wear and tear. Exposure testing involves subjecting items to specific environmental factors like temperature, humidity, and UV light for prolonged periods, mimicking real-world scenarios. Life cycle assessment (LCA) takes a holistic approach by considering the entire product lifecycle—from raw material extraction to disposal or recycling—to determine its overall environmental impact and durability. Moreover, light guards, protective coatings, and reinforced materials are often employed in these tests to enhance a product’s resistance against wear, tear, and degradation.
Best Practices for Conducting Effective Durability Checks
Conducting effective durability checks is an essential practice for ensuring product longevity and consumer satisfaction. To begin, it’s crucial to develop a comprehensive test strategy that aligns with the product’s design and intended use. This involves identifying critical components and stress points where failures are most likely to occur. Incorporating light guards during the initial design phase can significantly enhance durability; these protective elements safeguard vulnerable parts from impact, scratches, and debris, ensuring they withstand rigorous testing conditions.
Regularly simulating real-world scenarios is vital for accurate assessments. This includes varying environmental conditions, such as temperature extremes and humidity levels. Additionally, cyclic testing—where components are subjected to repeated stress cycles—reproduces the effects of wear and tear over time. By combining these methods, manufacturers can uncover potential weaknesses and make data-driven adjustments to design or material choices, ultimately producing superior quality products that stand the test of time.
Common Challenges in Durability Assessment and How to Overcome Them
Durability assessment often faces several challenges, each requiring strategic solutions. One significant hurdle is light guards—the protection against artificial lighting during testing conditions can significantly skew results. To overcome this, standardization and controlled environments are essential. Testing facilities should adhere to defined guidelines for light levels, ensuring consistency across all samples. Regular calibration of equipment and training for staff on proper procedures further mitigate light-related errors.
Another common challenge is the complexity of simulating real-world conditions. Materials and finishes might perform differently in lab settings compared to their behavior under various climates and uses. To address this, assessors must employ advanced testing methodologies like cyclic testing (to mimic environmental changes) and functional testing (replicating actual use cases). Additionally, leveraging historical data and industry best practices can provide valuable insights into expected performance, enhancing the accuracy of durability assessments.
Case Studies: Real-World Applications of Durability Checks
Durability checks have found real-world applications in various industries, demonstrating their importance in ensuring product longevity. Case studies show that implementing light guards has significantly extended the lifespan of electronic devices and automotive components. In one study, a leading smartphone manufacturer identified weak points in their device enclosures, which led to the introduction of advanced light guard mechanisms. These guards not only enhanced protection against drops but also withstood extreme temperature variations, ensuring the device’s functionality over time.
Similarly, automobile manufacturers have utilized durability checks and light guard technologies to combat issues like corrosion and impact damage. By strategically placing light guards in critical areas, such as underbody panels and wheel arches, they’ve achieved remarkable results. These measures have reduced repair costs and increased customer satisfaction, proving that thorough durability assessments are key to successful product development and longevity.
Future Trends in Durability Testing: Embracing Innovation
As technology advances, future durability testing will incorporate innovative approaches to simulate real-world conditions more effectively. One exciting trend is the integration of smart materials and sensors that can mimic environmental factors like temperature fluctuations, humidity, and impact forces. These advanced light guards offer unparalleled precision in monitoring product performance during tests.
Additionally, artificial intelligence (AI) and machine learning algorithms will play a significant role in data analysis and interpretation. By learning from historical test results, AI systems can predict potential failures and identify areas for improvement. This predictive analytics approach allows manufacturers to optimize their products’ durability before they even reach the market, ensuring consumer satisfaction and reducing waste.
Durability checks, encompassing various testing methods and best practices, are pivotal for ensuring product longevity. From understanding fundamental concepts to leveraging innovative trends like advanced material science and digital simulation, organizations can optimize their quality assurance processes. Incorporating light guards as essential tools in durability testing plays a significant role in this regard, providing robust protection against environmental stressors. By studying real-world case studies and addressing common challenges head-on, industry professionals can continue refining durability assessment practices, ultimately fostering the development of more resilient products.