Protecting Knife Blades: Comprehensive Guide to Corrosion Resistance
Corrosion significantly impacts the durability and performance of knife blades, leading to rust form…….
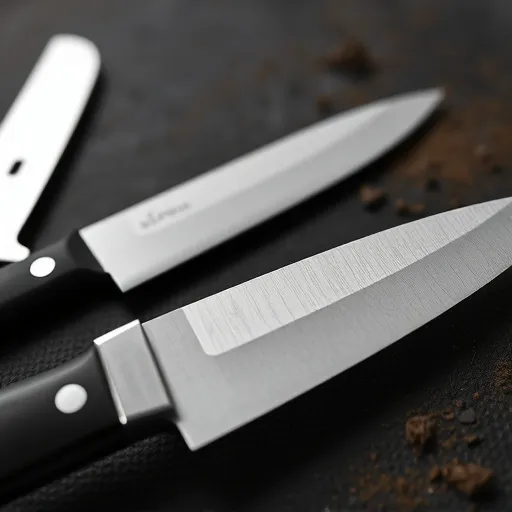
Corrosion significantly impacts the durability and performance of knife blades, leading to rust formation. To combat this, manufacturers use alloys, coatings, and innovative materials like stainless steel, titanium, and specialized plastics that offer exceptional corrosion resistance. Surface treatments such as coating and passivation further protect knife blades from moisture and chemicals. Designers should prioritize corrosion-resistant materials, strategic shaping, and protective coatings in the initial design phase to maximize blade lifespan. Advanced testing procedures ensure blade durability under various conditions. When selecting knife blades, consider specific application needs, material strength, and corrosion resistance, especially in environments with moisture or harsh chemicals.
Corrosion resistance is a critical factor in ensuring the longevity and performance of knife blades. This article delves into the intricate world of corrosion, exploring how it affects these sharp tools. We’ll uncover effective strategies to combat this ‘enemy’ by examining materials, surface treatments, design elements, and environmental influences.
Through an understanding of these aspects, you’ll learn to choose the right blade for your needs, ensuring durability and optimal performance, even in challenging conditions.
- Understanding Corrosion: The Enemy of Knife Blades
- Materials That Stand Strong Against Corrosion
- Surface Treatments for Enhanced Protection
- Design Considerations for Longer Lifespan
- Environmental Factors: Influence on Corrosion Resistance
- Testing Methods to Ensure Quality and Durability
- Choosing the Right Blade for Your Needs
Understanding Corrosion: The Enemy of Knife Blades
Corrosion, the silent enemy of many materials, poses a significant threat to the durability and performance of knife blades. When left unchecked, corrosion can lead to rust formation, compromising the sharp edge and overall functionality of the blade. Knife blades, with their critical role in various applications, demand robust protection against this destructive process. Understanding the mechanisms of corrosion is the first step towards ensuring longevity and optimal performance for these essential tools.
In the context of knife blades, corrosion resistance becomes a paramount consideration. Materials used in construction play a pivotal role; certain alloys and coatings offer superior defense against moisture, salt, and other corrosive elements prevalent in diverse environments. By employing innovative technologies and selecting appropriate materials, manufacturers can create knife blades that defy corrosion, ensuring they remain sharp, reliable, and ready for action in any setting.
Materials That Stand Strong Against Corrosion
In the battle against corrosion, certain materials emerge as champions, ensuring longevity and durability. Stainless steel, a popular choice, is renowned for its resistance to rust and oxidation, making it ideal for various applications, from culinary knife blades to industrial equipment. Its alloying elements, such as chromium, create a protective layer, hindering the degradation process.
Beyond stainless steel, other materials like titanium and certain types of plastic also exhibit remarkable corrosion resistance. Titanium’s high strength-to-weight ratio and robust oxide layer render it suitable for extreme environments, from aerospace to medical implants. Plastic materials, particularly those with added fillers or specialized coatings, can offer long-lasting protection against corrosive substances, making them valuable in sectors like packaging and plumbing.
Surface Treatments for Enhanced Protection
Knife blades, like any metal surface, are susceptible to corrosion, especially when exposed to moisture and certain chemicals. To combat this, various surface treatments have been developed to enhance their protection and prolong their lifespan. These treatments not only improve aesthetics but also fortify the blade against elements that could weaken its structural integrity.
One common method involves coating the knife blades with protective layers such as porcelain or polyurethane. These coatings create a barrier between the metal and potential corrosive substances, effectively reducing the rate of corrosion. Additionally, techniques like passivation, which involves immersing the blades in an acidic solution to remove free iron and other contaminants, offer another layer of defense against corrosion. Such treatments are particularly crucial for knives used in high-moisture environments or those exposed to harsh chemicals during food preparation.
Design Considerations for Longer Lifespan
To achieve a longer lifespan for knife blades, designers must consider several crucial factors from the outset. Material selection is paramount; choosing corrosion-resistant alloys like stainless steel or titanium can significantly prolong the blade’s life, especially in harsh environments. Additionally, designing with a focus on minimal surface exposure to corrosive elements, such as moisture or chemicals, will enhance durability.
Shape and structure also play a vital role. Smooth curves and well-defined edges minimize contact with potential contaminants, while strategic openings or vents can facilitate better air circulation, reducing humidity and preventing rust formation. Furthermore, incorporating protective coatings or treatments like passivation or powder coating adds an extra layer of defense against corrosion, ensuring the knife blade remains sharp and reliable over extended periods.
Environmental Factors: Influence on Corrosion Resistance
Environmental factors play a significant role in determining the corrosion resistance of materials, especially for items like knife blades designed to withstand various conditions. Exposure to moisture, for instance, is a primary catalyst for corrosion, leading to deterioration over time. Different environments offer unique challenges; humid climates or areas with high humidity levels significantly accelerate the process, making corrosion-resistant materials essential for durable knife blades.
Furthermore, temperature fluctuations and the presence of corrosive substances like salt water or industrial chemicals can severely impact blade integrity. These elements often necessitate the use of specialized coatings or treatments to enhance the resistance of knife blades, ensuring they remain functional and reliable in diverse settings.
Testing Methods to Ensure Quality and Durability
To ensure the quality and durability of knife blades, various testing methods are employed to simulate real-world conditions and assess their corrosion resistance. One common approach is salt spray testing, where blades are exposed to a mist of saline solution for a set period, mimicking corrosive environments. This method helps determine how well the blade material performs against rust and corrosion.
Another critical technique involves cyclic testing, which involves alternating between exposure to corrosive substances and neutral environments. This process simulates the constant changes in conditions that knife blades might encounter over time. By using these rigorous testing methods, manufacturers can guarantee that their products meet high standards of durability and performance, ensuring customer satisfaction and safety in various applications.
Choosing the Right Blade for Your Needs
When selecting knife blades, understanding your specific needs is key. Different applications require diverse blade designs and materials to ensure optimal performance and longevity. For instance, blades designed for cutting through metal may need robust, high-strength alloys like stainless steel or titanium, offering superior corrosion resistance. In contrast, kitchen knives often prioritize sharpness and edge retention over raw strength, with carbon steel or ceramic materials suiting these purposes.
Consider the tasks you’ll be tackling most frequently. If it’s heavy-duty industrial work, look for blades built to withstand extreme pressure and abrasion. For everyday use, a well-balanced blade with a comfortable grip can make all the difference. Always consider the material’s corrosion resistance, especially in environments where moisture or harsh chemicals are present, ensuring your chosen knife blades stand the test of time.
In conclusion, ensuring corrosion resistance in knife blades is paramount for their longevity and performance. By understanding the fundamentals of corrosion, selecting robust materials, employing effective surface treatments, considering design aspects, and accounting for environmental influences, you can significantly enhance the lifespan of your knife blades. Adhering to rigorous testing methods further guarantees quality and durability. Ultimately, choosing the right blade tailored to your specific needs will provide optimal cutting performance in various environments.