Platinum Casting Excellence: Techniques, Innovations, and Safety in Jewelry Production
The lost-wax casting process is a traditional yet sophisticated technique in fine jewelry making, pa…….
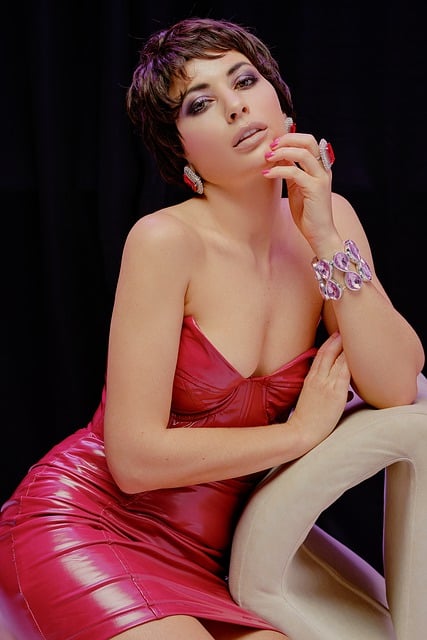
The lost-wax casting process is a traditional yet sophisticated technique in fine jewelry making, particularly for creating durable and detailed platinum jewelry. This method involves sculpting a wax model that captures the design's intricacies, which is then encased in a refractory material to withstand the high temperatures required for melting metal. The wax model is placed within a flask and covered with a hardened investment mold, typically made of sand and binder. Once heated, the wax melts away, revealing a cavity that accurately reflects the jewelry design. Platinum is then carefully poured into this cavity, adhering to the design's contours as it solidifies. The resulting piece undergoes meticulous finishing processes, including cleaning, filing, and polishing, followed by gemstone setting if required. The entire process has been enhanced with modern technologies like digital modeling and 3D printing, ensuring precise models that closely resemble the final product. These advancements, combined with high-purity platinum alloys and rigorous quality control, guarantee pieces of superior quality. Safety and environmental stewardship are paramount in platinum jewelry casting; artisans adhere to strict health and safety protocols and increasingly adopt eco-friendly practices, including non-toxic materials and recycling, to minimize the environmental impact and promote sustainability within the industry.
Explore the intricate world of platinum casting techniques, a niche yet significant field within jewelry manufacturing. This article delves into mastering the art of creating platinum jewelry, detailing the essential techniques and materials required. It guides you through the meticulous lost-wax process, offering a step-by-step insight into this age-old craft. Additionally, it unveils the latest advancements in investment casting for platinum, emphasizing best practices to ensure superior quality pieces. Safety and environmental considerations are also paramount, ensuring responsible operations in the jewelry casting industry. Join us as we shed light on these practices that elevate platinum jewelry casting to an art form.
- Mastering the Art of Platinum Jewelry Casting: An Overview of Techniques and Materials
- The Lost-Wax Process in Platinum Casting: A Step-by-Step Guide
- Innovations in Platinum Investment Casting: Advancements and Best Practices
- Safety and Environmental Considerations in Platinum Jewelry Casting Operations
Mastering the Art of Platinum Jewelry Casting: An Overview of Techniques and Materials
The Lost-Wax Process in Platinum Casting: A Step-by-Step Guide
In the realm of fine jewelry making, the lost-wax process stands out as a premier technique for casting platinum. This meticulous method, integral to high-quality jewelry casting, involves several critical steps that ensure the creation of intricate and durable pieces. The process commences with the designer conceptualizing and modeling the piece in wax, capturing every detail and contour desired. This model is then coated with a refractory material, which acts as an insulator, preventing the wax from melting during the casting process.
Once the wax is encased, it is positioned within a flask that holds it in place. The flask, along with its wax contents, is placed in a investment mold composed of sand and a binder. This mold hardens to form a matrix around the wax model, securing it for the subsequent steps. The setup is then heated to a precise temperature, allowing the wax to melt and drain away, leaving an exact cavity shaped like the original jewelry piece. Molten platinum is then poured into this cavity. As the metal cools and solidifies, it takes on the form of the cavity, resulting in a replica of the initial design in platinum. The final product is then finished through processes such as cleaning, filing, polishing, and setting with gemstones, if applicable, to achieve the exceptional standards of jewelry casting associated with platinum pieces.
Innovations in Platinum Investment Casting: Advancements and Best Practices
Innovations in platinum investment casting have significantly advanced, offering superior quality and intricate design capabilities for the jewelry industry. The traditional lost-wax casting method has been refined through technological advancements, such as the implementation of digital modeling and 3D printing. These techniques enable designers to create highly detailed models that accurately represent the final piece before casting, leading to a more precise mold and a higher-quality end product. The integration of high-resolution 3D scanners has also allowed for reverse engineering of existing platinum jewelry, facilitating the replication of unique pieces with exceptional accuracy.
Best practices in platinum investment casting emphasize the importance of material selection, precision in mold making, and meticulous attention to detail throughout the casting process. The use of high-purity platinum alloys ensures the durability and longevity that consumers expect from such precious jewelry. Additionally, controlling the pouring temperature and rate is crucial to minimize turbulence and porosity. Post-casting processes such as pickling, tumbling, and polishing are optimized to enhance the surface finish and bring out the luster inherent to platinum. Quality control at each stage of the casting process ensures that each piece meets the high standards set for platinum jewelry, ultimately providing customers with a product that is both beautiful and long-lasting.
Safety and Environmental Considerations in Platinum Jewelry Casting Operations
In platinum jewelry casting operations, safety and environmental considerations are paramount to ensure both the well-being of artisans and the preservation of the natural world. The process of casting platinum involves melting the precious metal at high temperatures, which requires stringent adherence to health and safety protocols. Protective gear such as heat-resistant gloves, eye protection, and respirators are essential to shield casters from the intense heat and potential inhalation of harmful particles or fumes. Additionally, the use of molds made from silicon, wax, or plaster necessitates careful handling to avoid chemical exposure or physical injury.
From an environmental standpoint, the casting process must be managed responsibly due to the toxic nature of some materials traditionally used in casting. The introduction of more environmentally friendly practices, such as utilizing non-toxic investment materials and recycling platinum scrap, has become a cornerstone of sustainable casting techniques. Proper waste management and disposal are critical to prevent pollution and protect local ecosystems. Moreover, energy consumption is another factor that must be considered; energy-efficient equipment and processes can significantly reduce the carbon footprint associated with platinum jewelry casting operations. These practices not only comply with environmental regulations but also contribute to a sustainable future for the industry.