Maximizing Electrical Connections: Navigating Ring Terminals and Wire Gauge Compatibility
Ring terminals offer versatile, reliable electrical connections, with a circular design allowing eas…….
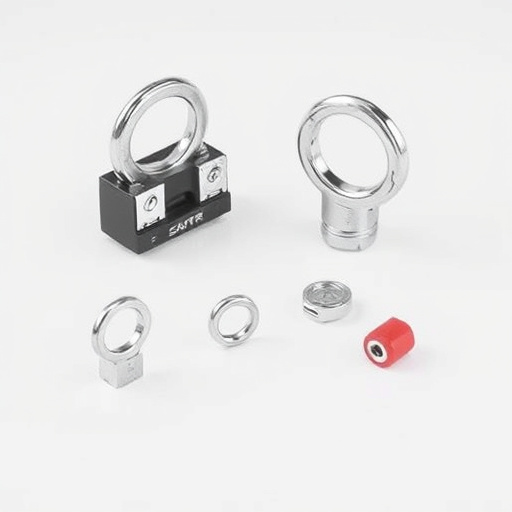
Ring terminals offer versatile, reliable electrical connections, with a circular design allowing easy wire insertion and crimping. Crafted from metals like copper or steel, they ensure superior conductivity and corrosion resistance. Wire gauge (AWG standards) is critical for optimal performance; smaller gauges (e.g., AWG 10-12) for flexibility, larger ones (e.g., AWG 4-2) for higher currents. Correct pairing with terminals prevents issues like loose connections or overheating. Different types of ring terminals cater to diverse applications: crimp rings for flexible bundles, soldered rings for fixed installations. Proper wire gauge selection ensures strong, reliable connections, preventing resistance, heat, and potential insulation damage. Using the correct ring terminals and gauge is vital for safety and system functionality in automotive and DIY projects.
“Ring terminals are essential components in electrical wiring, offering a secure connection point for wires. Understanding their functionality and compatibility with wire gauge is crucial for reliable installations. This article delves into the intricacies of ring terminal wire gauge compatibility, exploring key factors like different wire gauges’ roles in electrical connections and how to match them with appropriate terminal types. By understanding these considerations, you can ensure robust and long-lasting wiring solutions.”
- Understanding Ring Terminals: Definition and Basic Functionality
- The Role of Wire Gauge in Electrical Connections
- Compatibility Considerations: Matching Wire Gauge to Ring Terminals
- Common Types of Ring Terminals and Their Application
- How Wire Gauge Affects Connection Strength and Reliability
- Troubleshooting Issues Related to Incompatible Wire Gauge and Ring Terminals
- Best Practices for Ensuring Ring Terminal Wire Gauge Compatibility
Understanding Ring Terminals: Definition and Basic Functionality
Ring terminals are a type of electrical connection used to terminate wires, providing a reliable and secure joint for various applications. They are designed with a unique circular shape, featuring a gap that allows for easy insertion and crimping of wires. This simple yet effective design enables rapid assembly and disassembly, making ring terminals a popular choice among professionals and DIY enthusiasts alike.
The basic functionality of ring terminals involves creating an electrical path by bridging two or more wires. These terminals are typically made from durable metals like copper or steel, ensuring excellent conductivity and corrosion resistance. By using the right gauge (thickness) of wire for these terminals, one can guarantee optimal performance and safety in wiring systems, be it automotive, marine, or industrial settings.
The Role of Wire Gauge in Electrical Connections
Wire gauge plays a pivotal role in ensuring reliable and safe electrical connections, especially when using ring terminals. The gauge, measured in American Wire Gauge (AWG) standards, determines the cross-sectional area of the wire, which directly impacts its ability to conduct electricity efficiently. Smaller gauge wires, like AWG 10 or 12, are ideal for fine, delicate applications and offer superior flexibility, making them suitable for tight spaces where ring terminals are often used.
In contrast, larger gauge wires, such as AWG 4 or 2, are designed to handle higher currents and provide robust connections. When connecting electrical components using ring terminals, matching the wire gauge to the terminal’s specification is crucial. Using a smaller gauge wire in a terminal designed for larger gauges may result in poor contact, increased resistance, and potential overheating, while employing a larger gauge in a smaller terminal could compromise its mechanical strength and integrity.
Compatibility Considerations: Matching Wire Gauge to Ring Terminals
When selecting ring terminals for your application, it’s crucial to consider compatibility with your chosen wire gauge. Using the correct gauge ensures a secure and reliable connection. Mismatched gauge can lead to loose connections, increased resistance, or even potential failure of the circuit.
For instance, using a small-gauge wire with larger ring terminals may result in insufficient mechanical support, while employing a thick gauge wire with smaller terminals could cause excessive tension. Always refer to manufacturer specifications and industry standards for optimal compatibility between ring terminals and wires.
Common Types of Ring Terminals and Their Application
Ring terminals are a fundamental component in electrical wiring, offering a reliable way to connect wires and ensure secure connections. There are several common types designed for various applications. For instance, crimp ring terminals are widely used due to their ease of installation, allowing for quick connection and disconnection. These are ideal for flexible wire bundles in automotive and industrial settings. On the other hand, soldered ring terminals provide a more permanent solution, commonly employed in fixed installations like home wiring or commercial electronics.
Each type serves specific needs, catering to different environments and requirements. The versatility of ring terminals makes them an indispensable tool for electricians and technicians, ensuring proper wiring and system functionality. Their compatibility with various wire gauges is another advantage, allowing for customized applications across diverse industries.
How Wire Gauge Affects Connection Strength and Reliability
The wire gauge plays a pivotal role in determining the strength and reliability of connections made with ring terminals. In electrical systems, different gauges represent varying thicknesses and conductivity levels of wires, each optimized for specific applications. When connecting wires to terminals, using a wire gauge that matches or exceeds the terminal’s specification is crucial.
Smaller gauge wires, while more flexible, may offer weaker connections due to their lower current-carrying capacity. This can lead to increased resistance at the joint, generating heat and potentially damaging the insulation over time. Conversely, larger gauge wires provide more robust connections as they distribute the load evenly, ensuring better conductivity and reducing the risk of loose connections or overheating. Therefore, selecting the appropriate wire gauge for ring terminals is essential to guarantee optimal performance and longevity in any electrical setup.
Troubleshooting Issues Related to Incompatible Wire Gauge and Ring Terminals
When working with electrical systems, especially in automotive or DIY projects, ensuring compatibility between ring terminals and wire gauge is paramount to prevent issues. Using the wrong gauge can lead to loose connections, overheating, or even short circuits. These problems may manifest as dim lighting, faulty equipment operation, or, in severe cases, fire hazards.
Troubleshooting these issues often starts with a thorough check of the wiring diagram to confirm the specified wire gauge and terminal type. If incompatible ring terminals are already installed, the next step is to replace them with the correct size, ensuring a tight connection. Using a wire stripper and pliers, carefully remove the old terminals, clean the wire ends, and insert the new ones, tightening securely. This process requires precision and attention to detail to maintain the integrity of the circuit.
Best Practices for Ensuring Ring Terminal Wire Gauge Compatibility
When working with electrical systems, especially those employing ring terminals, ensuring wire gauge compatibility is paramount for safety and performance. Start by identifying the specific current rating required for your application; this will dictate the appropriate wire gauge. Refer to industry standards and manufacturer guidelines to cross-reference the intended use with recommended wiring practices.
Best practice includes using a gauge that matches or exceeds the current capacity specified for the terminal. Insulate wires securely within the terminals to prevent short circuits, ensuring a clean fit without excess slack. Regularly inspect connections for signs of wear or damage and maintain proper spacing between wires to prevent arcing. Always use high-quality wiring materials designed for compatibility with ring terminals to guarantee long-lasting, reliable performance.